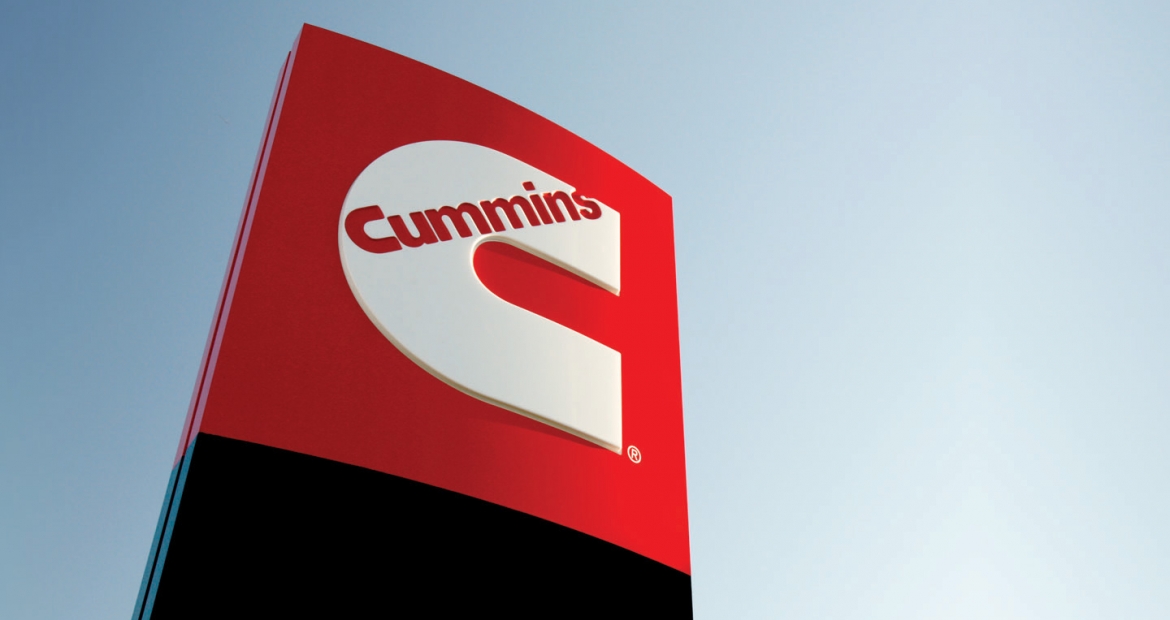
Cummins Vessel Reference #601
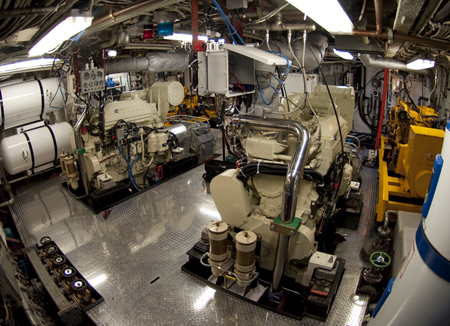
A couple of months ago I sent out a longer article on Island Tug’s repower of their vessel Island Defender. At the time I promised some shots of the finished engine room. On September 13 I took the attached photos, as I will not be in Vancouver on September 15 when sea trials take place.
When I visited the boat earlier one of the engine room crew promised me that there would be “lots of ‘bling’” on the finished job. That is clearly demonstrated in the attached photos where there has been extensive use of stainless steel throughout. Wherever practical stainless piping has been used. An interesting flourish is the manner in which stainless plate has been used for identity tags on valves. See the attached fuel tank manifold photo.
As explained in the attached article, such refinement is not limited to the engine room. On deck a stainless steel fairlead has been mounted on the bow. While reminiscent of those on the big docking tugs, Paul Kruse, explained that this one is designed to reduce the friction and hence wear on modern synthetic mooring lines. Another innovation, this one reminiscent of the line stops on larger anchor handling tugs, is a combination fair lead and mooring cleat on the bulwarks. Kruse explained that when British Columbia tugs are working barges up close with bridles the bridle wire can hang up on the conventional bollards mounted on the bulwarks, This design prevents that while providing a convenient fair lead and a cleat mounted low and out of the way.
These are just a couple of examples of the kind of improvements on this stalwart tug that have resulted from a company that listens to its crews. Already ISO certified for management they are currently beginning the process of ISO 14000 certification for environmental considerations.
British Columbia, on Canada’s west coast, has some attractive and well-proven tugs, but the fleet is aging with many vessels over thirty years old. Four years ago Vancouver’s Island Tug and Barge (www.islandtug.com) launched the new build Island Scout with a pair of Cummins KTA38 main engines.
This August, they will return their 1977-built 21 by 7.28-meter tug Island Defender to service. The midlife rebuild has taken a year to complete but as Island Tug’s president Bob Shields explained this was much more than a repower, “As with our other Cummins repowers, we conducted a life cycle cost analysis using Robert Allan Ltd. for assistance and determined that a package that included a pair of Cummins KT19s would yield us the best value. The engines are soft mounted and connected to the drive train via a Centa Link coupling which we expect to have a tremendous impact on overall vessel noise as it did on the Island Scout. We added a Krill fuel management and monitoring system, new shafts and Kobelt shaft brakes, Rice nozzles and propellers and a pair of John Deere gensets. Most of the rest of the vessel has been re-built as well which has taken a little over a year to complete.”
Project manager Paul Kruse filled in some of the details of the extensive job as well as the pros and cons of such a rebuild versus a new construction. “We had a good hull to start with,” he said. The Island Defender was built in Vancouver as the log-towing tug Hamilton Bailey with a pair of 480 HP Cat D346 mains. Later the boat was taken around to the Great Lakes aboard a heavy lift ship. There she was renamed the Josee M and re-powered with a pair of Detroit DDEC V16-92 engines rated for 1100 HP each at 2100 RPM. Subsequently North Arm Transport brought her back to the Pacific coast before selling her to Island Tug. “A steel boats rusts from the inside out,” explains Kruse, “It is easy to sand blast them and paint them all up nice on the outside but the inside is often neglected. But this boat had good steel through most of the boat. We gutted the hull taking out all the piping and repainting it with modern epoxy paints.”
That was just the start of the job. The fact that the hull had sponsons that act as mounts for the fendering and guards for the hull was an asset. Although use over the years had opened cracks in the steel that allowed salt water in, the main hull was well protected. The sponsons were opened up, blasted and painted inside then divided into four compartments before being resealed. The entire bulwark steel around the aft deck and stern was replaced and the Western Machine Works towing pins refurbished with new parts. The tug’s original Burrard single drum towing winch was taken back to the Burrard shop for a complete rebuild and minor updates. ”I’ve got nothing but good to say about Burrard and their winches,” said Kruse.
The accommodation areas were not neglected in the rebuilt with some bunk rooms gutted and refurbished. The galley got a total rebuild with fine new woodwork done in house at Island Tug’s own maintenance facility. The original concrete layer on the deck was taken up and replaced with a sound-damping system that includes layers of a cork-concrete mix and perforated aluminum all topped with an acrylic flake finish.
The bridge as well as two outside control positions received updating including a new set of Cummins engine monitoring and control panels in the main wheelhouse. Additional winch controls including air-assisted power brakes were added on the flying bridge as well as the control station on the aft cabin top. Even the stack got the company’s new colour scheme.
The engine room is the heart of a tug and it was here that the most significant changes took place for the Island Defender. With old main and auxiliary engines removed as well as the piping, it was possible to clean the interior and apply the new acrylic paints. The existing ZF 5.037:1 gears were sent out to the Seattle shop to be refurbished and adapted from the direct link that they had to the old engines to the new flexible link that they would have to the new Cummins mains. While the old engines were 1100 HP each the new will be only 500 HP each it was decided to keep the original gears which were hard mounted to the hull while the engines are soft mounted to reduce noise levels in the boat.
When in dry-dock at Allied Shipyards, the old Kort 19A nozzles and their five-blade Kaplan props were removed. New Rice nozzles and three blade props were installed with the trailing edge of the nozzles cut away to allow the placement of the rudders within six or seven inches of the wheels for improved handling. In spite of the reduction from 2200 HP to just under 1000 HP total, The ownsers are expecting improved performance. Bob Shields explained, “According to the RAL predictive graphs, the Rice nozzles will produce a static bollard pull of 34,000 pounds and, with a 5500 tonne barge, we will see seven knots loaded and nine knots empty which is an increase in efficiency of 8% over the previous setup.”
Canadian crewing regulations require a full time engineer in tugs with over 1000 HP. The reduced crewing and significantly reduced fuel consumption will contribute to increased profitability for the re-built tug. Todd Barber of Robert Allan Ltd. developed re-power scenarios for three different engine manufactures taking into account capital and operating costs to come up with this re-power. As the new engines are significantly lighter, the existing ballast that had been mounted inside the hull on either side of the centerline was removed and replaced with a 5.5-ton steel bar on the bottom of the keel.
The boat’s primary work will be coastal towing of 25,000 barrel fuel barges and 5500 tonne deck barges
As the installation and fittings of the engine room were being finished up the high quality of workmanship became apparent as did the pride that the fitters took in the project. One of the shipyard crew protested that a photographer should wait until the job was finished “And we have all the ‘bling’ in place”. He went on to explain that there would be a good bit of bright finished metal in the immaculate engine room. The owners are well aware that their commitment to careful study prior to such a job will ultimately bring savings in capital costs (this rebuild costs are about 60% of a new build) and savings in operation with lower fuel costs and less down time. But they also recognize the value of the pride generated in the installation crew and the boat’s future crews in having superior equipment to operate.
For further information:
R. L. (Bob) Shields
President
Island Tug and Barge Ltd.
55 Rogers St.
Vancouver, BC V6A 3X8
Phone: 604 873 4312
Direct Phone: 604 877 5355
E-mail: BobS@islandtug.com
Web: www.islandtug.com
Cary Griffith
Cummins British Columbia
18452-98th Ave.
Surrey, BC V4N 3P8
Canada
Phone: 604 882 5726
E-mail: cary.j.griffiths@Cummins.com
Trophy fish are measured by weight and length at the dock. They almost always exceed the size of the angler reeling them in. The exception would be M/V Chelsea ...
Greek passenger vessel repowers with Cummins. Cruising to Symi on a water taxi is more than a boat ride across the Aegean Sea. Departing the eastern sh...
Crews with no choice but to head out to sea in rough weather conditions rely on trawlers' inherently robust, stout design based on the DNA of highly capable fis...