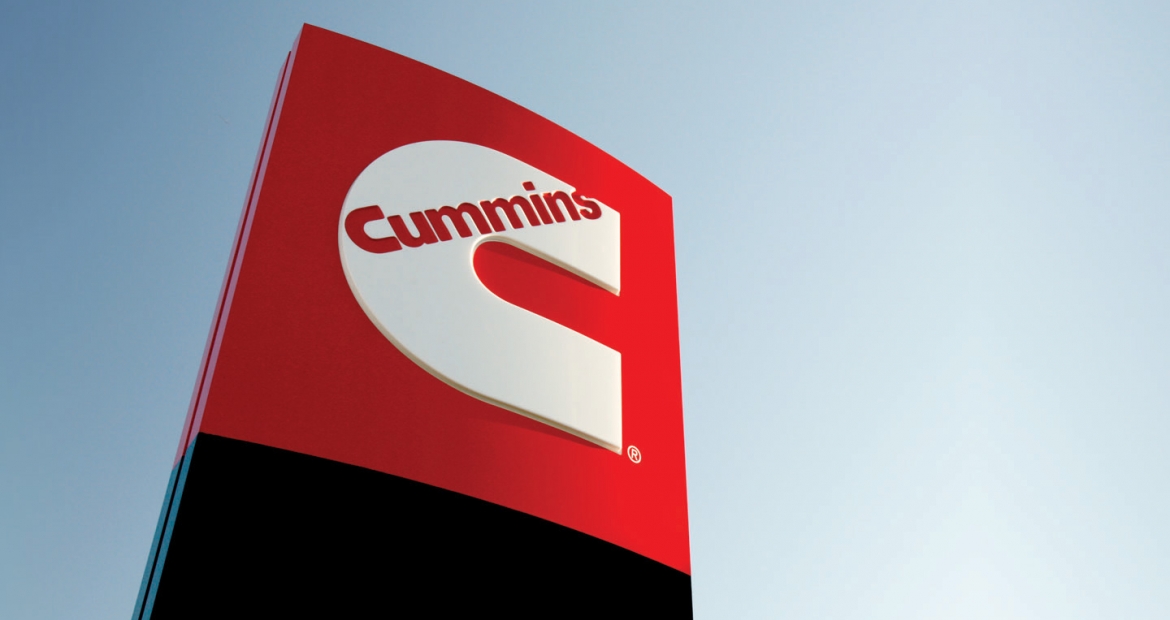
Cummins Vessel Reference #607
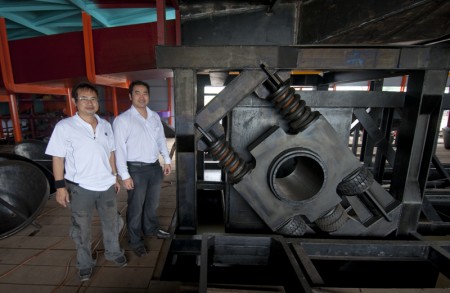
“We hire a new crew to build each dredge,” explained Khun Songpon, “My father, Yongyut Junsiri, trains them as they build the dredge then the same crew operates it in Indonesia. They built it so they know how to care for it and how to fix it when necessary.”
It is a brilliant innovation, but not surprising from a firm that can draw on the 35-year experience of its president Yongyut Junsiri in both the design and operation of dredges. In recent years the opportunities for tin dredges have centered on Indonesia. However it is experience gained in dredging Thai waters that has put Thai builders and operators in a favourable position to develop Indonesian partnerships that can secure the necessary leases.
The vessels themselves are remarkable innovations. They are built with basic technology that will stand up in work areas with few suppliers. Based on four 2.3-meter diameter pontoons the vessels are 83-meters long over all with the two outside pontoons shorter than the inboard pair. With a 55-meter dredge arm and a 2.55-meter cutter head the dredge has a 60-meter working depth.
The dredges are self-propelled with a pair of retractable propulsion propellers and retractable rudders. For maneuvering when dredging a pair of in-house designed and fabricated Z-drives are mounted on the two stern quarters. Each of the propulsion drives and the Z-drives is powered by a dedicated 360-HP refurbished Hino diesel engine. The propellers on the Z-drives have a 156-cm. diameter with the propulsion props being slightly smaller. A keel cooler system has been installed to service all four engines.
Forward, of on either side of the dredge-arm, another Hino engine turns the hydraulic pumps that supply power to turn the cutter head as well as to winches on the deck above that raise and lower the dredge-arm and the vessel’s fore and aft anchors.
The heart of the dredge is the pump engine. This is a big 12-cyliner 1000-HP Cummins KTA38 mounted so that it can turn into the gear and pump mounted on the top end of the dredge arm. The dredged material is brought from the sea floor and pumped to an upper deck where it begins a series of filtering processes. It first enters a large tumbler fabricated with evenly spaced rods that separate out the larger rocks that then pass down a tunnel to return to the sea over the stern. The finer material drops down through rubber filters that remove more of the larger material and then into a set of cone-shaped filters the first of which are about 1.3-meters in top diameter. From there the remaining material drops into similar but smaller cone filters before being deposited in steel boxes at the main-deck level. Finally the remaining material is hand washed to yield an ore that ranges around 75-percent pure tin. This is then transported to shore for final processing and sale.
The construction takes about eight months. As delivered, the dredge costs about 70 million Thai baht. (US$2.361 million) This price can vary with the price of steel and equipment options. Earnings for the dredges in Indonesia are such that repeat orders are steady.
Once completed, the dredge is navigated at 8.5-knots from Thailand to Bangka Island off the southeast coast of Sumatra in Indonesia. The delivery voyage takes about ten days. The crew of 15, all trained while building the dredge, can keep the dredge operating around the clock. The builders have been contracted to crew and operate the vessel by the Indonesian partners. Crewmembers are rotated home for 15 days every three months.
For more information:
Songpon Junsiri
Vice President
Songchai Business Unlimited Partnership
89/28 Moo 5 Rassada
Muang Phuket 83000
Thailand
Phone: 085 8136399
E-mail: tony.junsiri@gmail.com
Sathit Suwanprasert
Senior Sales Engineer,
Diethelm & Co. Ltd.
1696 New Petchburi Rd.
Bangkapi, Huaykhwang
Bangkok, 10310
Thailand
Phone: 02254 4900 x 218
Mobile: 081 913 6599
E-mail: sathit.s@dksh.com
Trophy fish are measured by weight and length at the dock. They almost always exceed the size of the angler reeling them in. The exception would be M/V Chelsea ...
Greek passenger vessel repowers with Cummins. Cruising to Symi on a water taxi is more than a boat ride across the Aegean Sea. Departing the eastern sh...
Crews with no choice but to head out to sea in rough weather conditions rely on trawlers' inherently robust, stout design based on the DNA of highly capable fis...