Austin Hospital is prepared for any emergency with three Cummins generator sets
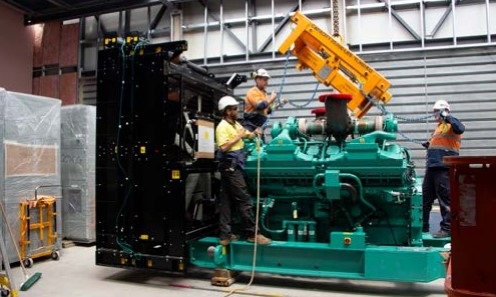
Cummins has played a key role in the installation of a new emergency power system at one of Australia’s time-honoured medical institutions, Austin Hospital in Melbourne.
A hospital steeped in history, reopens after major redevelopment
Steeped in history, Austin Hospital was opened in 1882 as ‘The Hospital for Incurables’. The original ‘incurables’ were mostly tuberculosis sufferers but by the 1920s the second wave of ‘incurables’ were cancer sufferers. In fact, by 1935 the hospital was the largest cancer hospital in Australia and to this day still supports more cancer research than any other medical centre.
Located in the Melbourne suburb of Heidelberg, Austin Hospital today is a major teaching public hospital and along with its reputation for cancer treatment provides the only Victoria-wide service for acute spinal injuries and liver transplants. It has over 560 acute beds for its wide range of services.
In 2005, the hospital was reopened after a major redevelopment and is housed in one of two towers, the other tower occupied by Mercy Hospital for Women. The new emergency power plant, which serves both the Austin Hospital and Mercy Hospital towers, replaced generators that were installed in an adjacent building – the boiler house in an early era – and were unreliable.
Three Cummins generator sets provide emergency power for Austin Hospital
Three Cummins generator sets, designed around Cummins’ 60-litre QSK60 diesel engine, are at the heart of the emergency power plant that has been installed on a new mezzanine floor on the hospital roof, effectively adding a 10th storey to the building.
The 2250 kVA generator sets were broken down into three major components – radiator, engine and alternator – so that each were under 10 tonnes to allow the crane to hoist them safely to the plant room on the hospital roof; the 16-cylinder engine was the heaviest at 9.5 tonnes.
Nilsen headed up the project to improve electrical infrastructure capacity at Austin Hospital and contracted Cummins to supply and install the generators, fuel system and plant room acoustics.
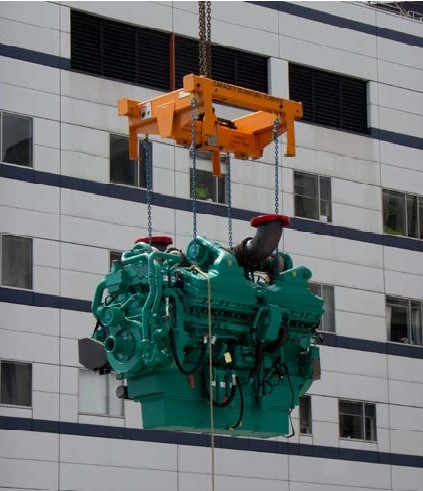
Jumping a few hurdles to cross the finish line ahead of schedule
“We were given a tight time frame so had to hit the ground running…we actually completed the project three months ahead of schedule,” says Adam Ferrara, power generation project manager for Cummins Laverton in Melbourne.
“Most importantly, our customer (Austin Health) is very happy with the new installation,” says Nilsen project manager Cameron Harper. “The work Cummins has done is of a high standard, and to have completed it three months ahead of schedule is a great achievement.”
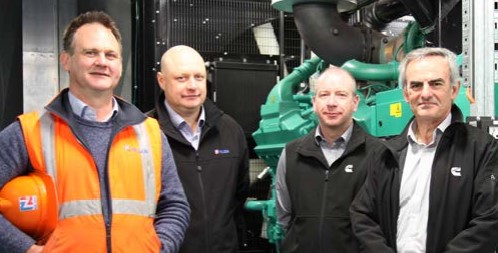
One of the challenges for the project team was working within a fully operational or ‘live’ hospital. As Nilsen project foreman David Frazer points out: “A lot went on behind the scenes such as load bank testing and commissioning and we had to ensure there was no interruption to the hospital’s power supply… the hospital didn’t lose power for one second during the entire project,” he says with a definite tone of pride.
Cummins’ proven expertise in emergency generator installations at other major hospital projects around the country along with well-established product reliability were key reasons it got the nod for the Austin Hospital job.
“We had an on-site team of up to eight mechanics and electricians from Cummins Laverton during the construction and commissioning phases,” says Adam Ferrara, who worked closely with Cummins application engineer Kevin Baxter. “We allowed a week for the crane lifts but these were actually completed in two days. The fully built-up generator sets were disassembled at our Laverton branch and the components trucked to the site.”
QSK60 generator sets are built for vibration and noise control
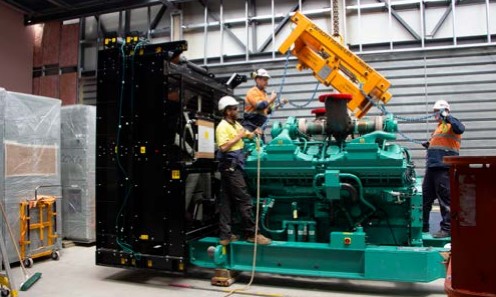
Stringent vibration and noise control is achieved with the generator sets mounted on spring isolators and an acoustic membrane separating the two concrete floor slabs. Other acoustic measures in the plant room result in a barely discernible hum when the three generators are running at full load.
The three Cummins C2250 D5 generator sets, incorporating Cummins PowerCommand digital paralleling equipment, source their fuel from two 11,000-litre tanks in the basement carpark along with three 1000 litre day tanks in the plant room. Two other Cummins generator sets – 1400 kVA and 550 kVA units – were also recently installed on the Austin campus by Cummins Laverton as part of the emergency power upgrade carried out by Nilsen. The 1400 kVA set, powered by Cummins’ KTA50 engine, and the 550 kVA unit, powered by Cummins’ QSX15, are back up for the Lance Townsend and Harold Stokes buildings.
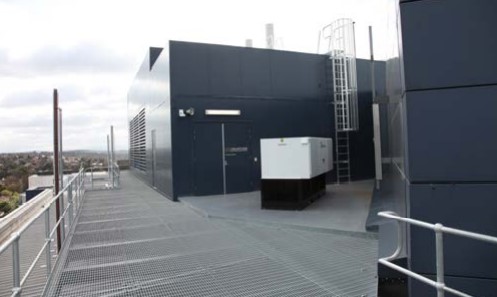