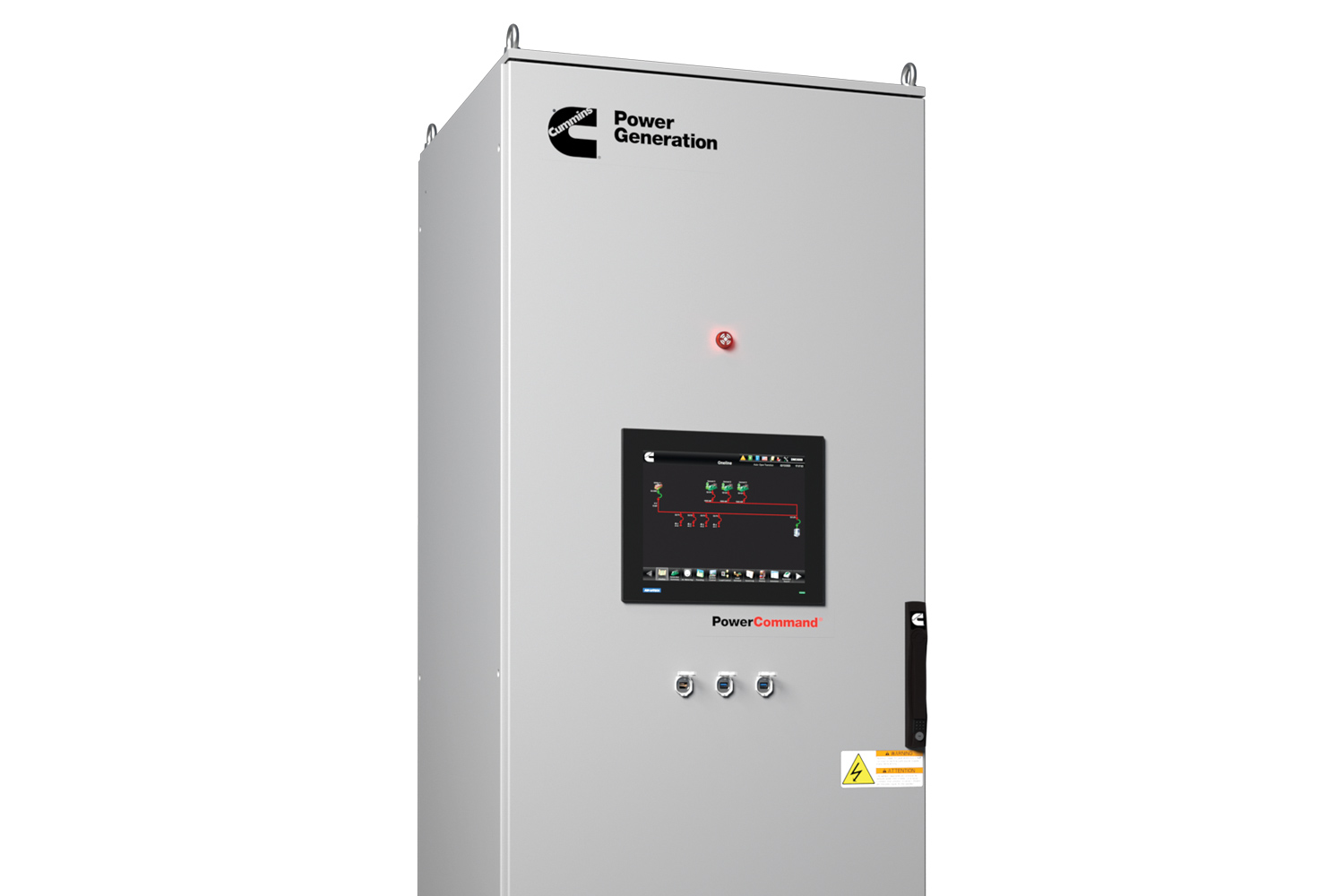
Upgrading Cummins’ legacy Master Controller MC-150 to the Cummins Power Command® DMC6000 for a major network and communication service provider in Saudi Arabia
Project background
The upgrade was essential as the legacy Master Controller MC-150 which was in service for over twenty years, had reached end-of-life due to the obsolescence of both its software and hardware components. Additionally, the customer aimed to optimize their generator control system by transitioning from the legacy PCC3200 controllers to the advanced PCC3300. This comprehensive upgrade also included redesigning the control sequence for generators managed by Cummins’ Master Controller, facilitating more efficient and dependable autonomous operations to meet the customer’s advancing operational requirements.
After two decades of reliable service, Cummins legacy Master Controller MC-150 has reached the end of its operational life, having effectively supported the customer’s needs over the years. However, as technology advanced, the MC-150 began facing challenges due to outdated hardware components and limited software capabilities.
Key limitations included:
- Obsolete software and hardware: The MC-150 had outdated hardware components including a PLC running on DOS operating system, along with obsolete hardware I/O modules, making it increasingly difficult for Cummins to provide the expected, high-level aftermarket support. With the system relying on discontinued components, even a single module failure led to extended downtimes due to the unavailability of spare parts. This situation not only increased maintenance costs but also disrupted operations, with prolonged repairs impacting production timelines.
- Text-based monochromatic HMI: The MC-150 was equipped with a basic monochromatic Text HMI, limiting visibility and real-time monitoring options for operators. The HMI’s limited display and control functionality restricted the user experience and complicated system troubleshooting, as critical data visualization and process tracking were constrained by the outdated interface.
- Slow processor and communication issues: The legacy MC-150’s PLC featured a slower processor with limited communication capabilities, affecting the coordination and response times of the system. Communication protocols between the MC-150 and the local generator controllers PCC3200 was slow and outdated, resulting in delayed responses and overall sluggish performance. This slow communication speed disrupted the real-time control and management of generators, creating inefficiencies in power regulation and system responsiveness.
After more than two decades in service, it was the right time for the MC-150 to pass the torch to Cummins’ latest innovation, The cutting edge Digital Master Controller DMC6000. This DMC6000 offers robust features designed to meet today’s complex operational requirements, ensuring the customer’s system continues to perform at peak efficiency well into the future.
Objective
Cummins’ new Digital Master Controller DMC6000 represents a leap forward in power plant control technology. Designed using cutting-edge PLC models, automation hardware, and software, the DMC6000 integrates Cummins’ proprietary logic design, which is customized to address the unique operational requirements of the customer. It includes the consideration of over 1200 failure mode sequences, enabling the DMC6000 to autonomously manage the power plant and make informed decisions, even in rare and extreme fault scenarios.
Cummins Arabia DBU Service team expertly supervised and managed the replacement of a legacy MC-150 controller with the new Cummins DMC6000 by working closely with the customer’s electromechanical contractors, the team provided comprehensive technical support to ensure that the DMC6000 installation adhered seamlessly to Cummins’ installation guidelines.
A key achievement of this project was the strategic reuse of existing control cables, enabling a seamless, direct swap without the need for a costly and time-intensive temporary solution. This approach significantly enhanced project efficiency. Effective coordination with the installation contractors was essential, allowing the team to schedule the upgrade precisely during a planned power outage.
Additionally, the project involved a retrofit of three PCC3200 units to PCC3300 control panels for three QSK23-G3 generator sets. This direct swap solution not only minimized downtime but also optimized the upgrade process, ensuring long-term reliability and advanced operational control for the customer.
Solution overview
Power system overview: The system operates as a 220V/127V LV Isolated Bus transfer pair, without a Generator Main, controlled by the new Digital Master Controller (DMC6000). The power system consists of three 220V x 800KW diesel generators (DGs), three 220V utility incomers with ATS arrangements, and three downstream outgoing feeders.
Key features: The new DMC6000 delivers faster processing speeds and cutting edge communication with the new generators’ PCC3300 local controllers. It has a 15” multi-touch HMI screen with intuitive graphics and advanced diagnostic tools, enhancing visibility, accessibility, and ease of use for operators, technicians and engineers. The system leverages the cutting-edge Modbus TCP/IP communication protocol, ensuring enhanced reliability and performance while providing robust, high-speed communication with the customer’s BMS/DCS systems. Designed for scalability, the system supports seamless integration with up to 16 generators, enabling effortless future expansion as operational needs evolve.
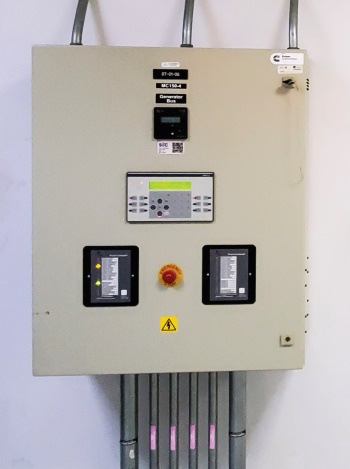
Implementation
Project Partners: Cummins Arabia collaborated with a range of specialized contractors, each assigned to manage a specific aspect of the upgrade. The teams handled key tasks including the power cable management, decommissioning of the legacy MC-150 mechanical panel, electromechanical installation of the new DMC6000 panel, and the termination of control cables into the new system. Throughout the process, the Cummins Arabia service team expertly oversaw all activities, ensuring seamless coordination between the customer’s project and operations teams.
Installation steps
- Decommissioning the legacy MC-150 panel: The first step involved safely shutting down all power sources, including engine batteries, battery chargers, and power sensing fuses, to ensure a safe working environment.
- Decommissioning of the PCC3200 generator control panel: Similar to the MC-150, power to the 3 x PCC3200 generator controllers was turned off, including engine batteries, battery chargers, and power sensing fuses.
- Cable verification: All power, control, and communication cables were verified and cross-referenced with the existing wiring drawings to ensure accurate disconnection and reconnection.
- Panel removal and installation: The old MC-150 panel and the 3 x PCC3200 generator control panels were removed and replaced with the new DMC6000 and 3 x PCC3300 panels, respectively.
- Cable termination: Existing cable terminals were clearly labeled to facilitate accurate and efficient termination during the installation of the new panels.
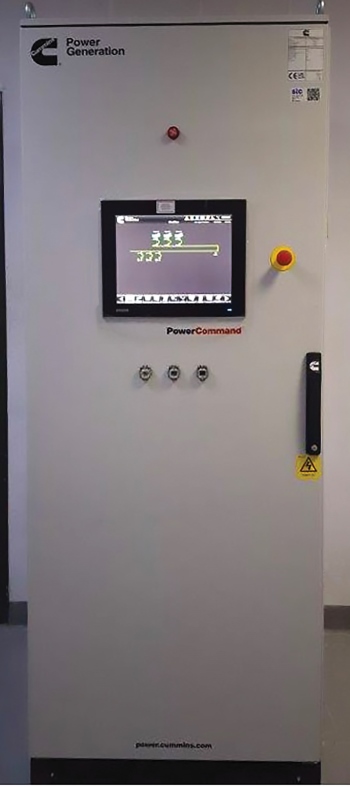
Timeline
The project was successfully completed within the agreed 6-week shutdown period. All activities were carried out as planned, starting with the decommissioning of the legacy MC-150 panel. This was followed by the installation, testing, and commissioning of the new DMC6000, along with the integration of the three new PCC3300 controllers. Each phase was meticulously managed to ensure smooth transitions and timely execution, ultimately leading to the successful activation of the upgraded system.
DMC6000 product overview
The DMC6000 is a pre-engineered, scalable power system paralleling control solution designed for a wide range of complex power systems. Featuring advanced modular control and a user-friendly 15" touchscreen interface, it offers exceptional flexibility in system design and functionality that can monitor and control both LV & HV power systems. With over 1,200 failure mode scenarios integrated, the DMC6000 provides robust, comprehensive power control for up to 16 generators, 16 loads, and 2 utility connections, ensuring seamless and reliable operation across diverse applications. For more details, visit Cummins DMC6000.
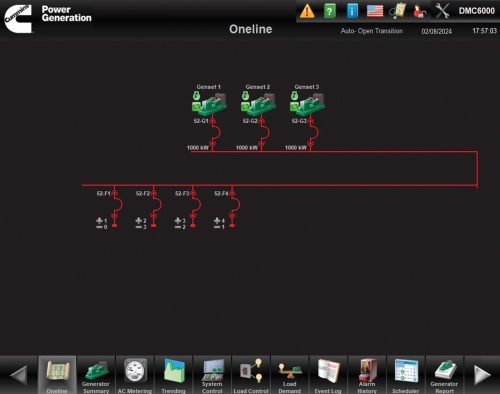
Operational benefits
- User interface: The built-in 15" color touchscreen with high-resolution graphics (1024x786) and intuitive controls, which enhances operator interaction. The system provides real-time and historical data trending, enabling operators and engineers to make informed decisions.
- System expansion: The DMC6000 supports up to 16 generators, 16 loads, and 2 utilities, allowing for complex configurations such as isolated bus, common bus, and main-tie-main topologies. This flexibility ensures it can meet evolving operational demands.
- Communication and connectivity: It uses the advanced Modbus TCP/IP protocol for reliable and fast communication with external systems like BMS/DCS. Additionally, distributed logic based on ring ethernet guarantees optimal data transfer speed at 100 Mbps.
- Remote access: The system allows remote access via a web browser, enhancing maintenance flexibility. Operators can also use an optional remote touchscreen for added convenience.
- Failure scenarios and diagnostics: The system is equipped with over 1,200 failure scenarios, and advanced diagnostic tools, enabling proactive maintenance and minimizing downtime.
- Compliance and safety: The DMC6000 complies with UL891, IEC/EN61439-2:2011, EMC Directive 2014/30/EU, CSA 22.2, Eurocode 8 (seismic certification), LV Directive 2014/35/EU, RoHS 2011/65/EU, CE & UKCA standards, ensuring reliability and safety across various industries, including oil and gas, healthcare, and manufacturing.
- Enhanced software capabilities, includes a suite of advanced software features:
- Trends, Events, and Alarms History: Stores historical data for up to 365 days, providing detailed insights into operational trends, events, and alarm logs for proactive maintenance and troubleshooting.
- Help Screens: Intuitive help screens guide operators through system operations and troubleshooting procedures, reducing downtime and enhancing operational efficiency.
- New Load Demand Functions: Optimizes load distribution based on real-time demand fluctuations, improving grid stability and energy efficiency.
- Enhanced Graphical User Interface (GUI): Features a redesigned GUI with improved graphics and visualization capabilities, offering clearer data presentation and a more user-friendly experience.
- Long-term support and spare parts availability: Ensures continuity of aftermarket support and availability of spare parts for extended periods, mitigating risks associated with obsolescence and reducing maintenance costs.
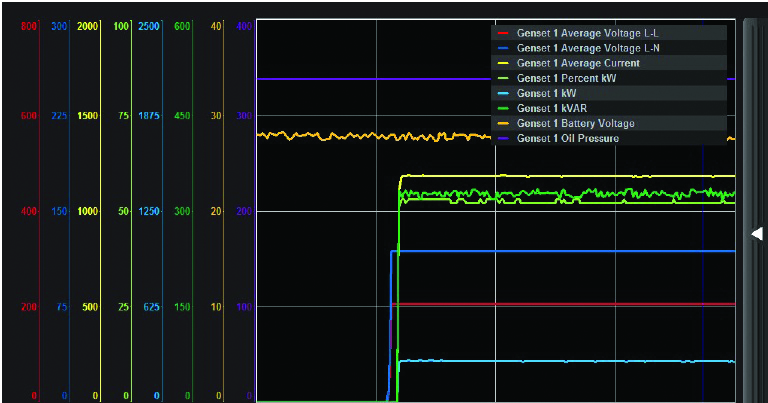
Customer feedback
The customer expressed a high level of satisfaction with the DMC6000 upgrade, noting several key benefits that exceeded their expectations:
- User-friendly interface: The 15" color touchscreen in the new DMC6000 offers a vast improvement over the monochrome text display in legacy MC-150. The new HMI has intuitive graphics and provides user friendly access to power system’s essential information, moreover, The integrated help screens available in the DMC6000 HMI are very useful in case of any doubts or operational questions.
- Data access and reporting: The setup allows for straightforward USB connection at the service port of the panel, facilitating easy report viewing and data extraction. Even USB printers can be easily configured to directly print the alarms/ events log, streamlining the process of accessing operational data and logs.
- Enhanced connectivity: The DMC6000 offers easier and more reliable connections to extra supervisory systems such as BMS/DCS/SCADA system over the Modbus TCP/IP communication interface. This has significantly improved the ease of troubleshooting and fault-finding, reducing downtime and increasing the speed of maintenance tasks.
- Advanced software features: The inclusion of trends, events, and alarms history, along with integrated help screens, has made it much easier for the customer’s team to manage and diagnose issues. This feature-rich environment supports proactive maintenance and improves overall operational efficiency.
- Aftermarket support: With cutting-edge software and hardware features, the customer does not need to worry about parts availability for the next 15+ years, ensuring long-term reliability and reducing maintenance concerns.
- Future-proof design: The new DMC6000 will ensure long-term reliability of the power system and compatibility with future technological advancements, reducing concerns over obsolescence and enhancing the power plant’s sustainability.
- Scalability and flexibility: The DMC6000 supports up to 16 gensets, 16 loads, and two utilities, accommodating future expansion and various configurations like isolated bus and main-tie-main.
- Energy management optimization: Integrated load demand functions improve energy efficiency and operational stability.
- Remote access capabilities: Web-based remote access enhances flexibility for offsite monitoring and maintenance, with optional remote touchscreen support.
- Preconfigured algorithms and advanced diagnostics: The DMC6000 is equipped with pre-configured control algorithms that incorporate over 1,200 failure scenarios, enhancing fault diagnostics and preventive maintenance capabilities. This extensive setup allows the DMC6000 to rapidly detect and address issues, which minimizes downtime and ensures more reliable power system performance. These algorithms make real-time adjustments and offer intuitive diagnostics, enabling operators to maintain seamless operations and reduce the risks of unexpected failures.
Authors: Medhat Mohamed, Paul Pandi
Challenge: Digea required standby power for more than 45 digital television broadcast sites around the country, which was essential t...