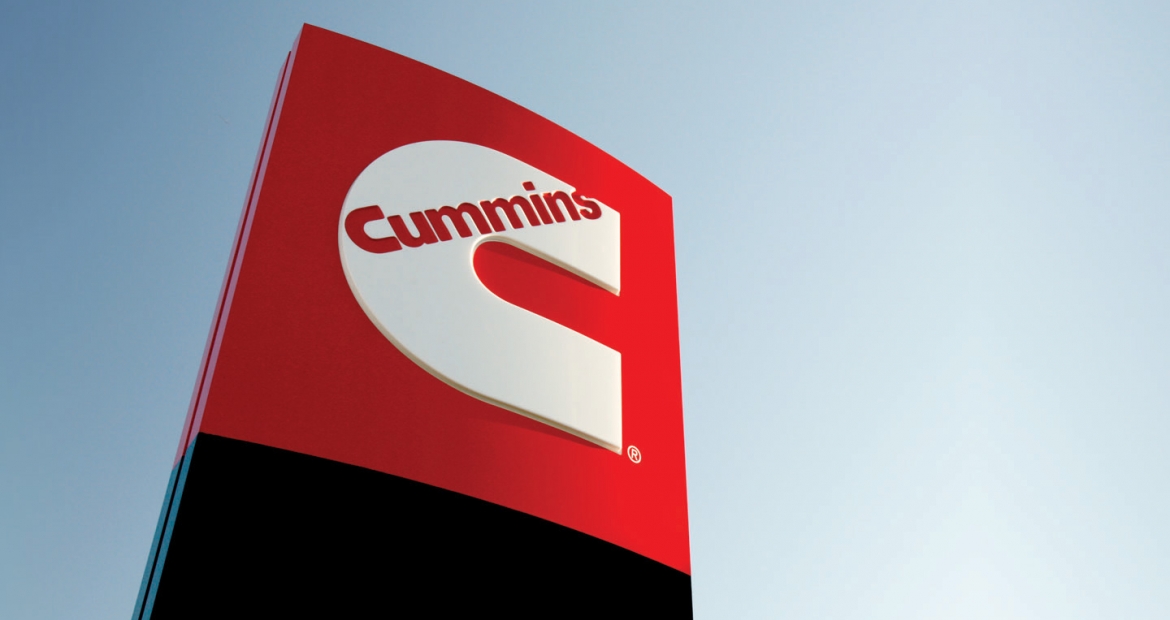
Project background
The upgrade was necessary as the legacy DMC300 reached end-of-life due to obsolete hardware components and software. Additionally, the customer aimed to add more generators and required changes in the control sequence to enable integration with a PV renewable system.
Challenges
The legacy DMC300 was equipped with outdated PLCs, having obsolete software and hardware modules, leading to several challenges:
- Obsolete software and hardware
- The outdated PLCs used obsolete software and hardware modules, causing significant difficulties in obtaining aftermarket support and spare parts. When the product had one faulty module, the unavailability of spare parts led to prolonged downtimes and increased maintenance costs.
- Communication protocol issues
- The communication protocol between the legacy DMC and the local generator controllers was outdated and slow. This resulted in inefficient communication, delayed responses, and overall sluggish performance of the control panel. The slow communication speed impacted the coordination and control of the generators, leading to inefficiencies in power management.
- Impact on production
- The combination of obsolete hardware, outdated software, and slow communication protocols had already impacted production several times in the past. The control system’s inability to quickly and reliably communicate with the generator controllers caused delays and interruptions in power supply, affecting the plant’s operational efficiency and reliability.
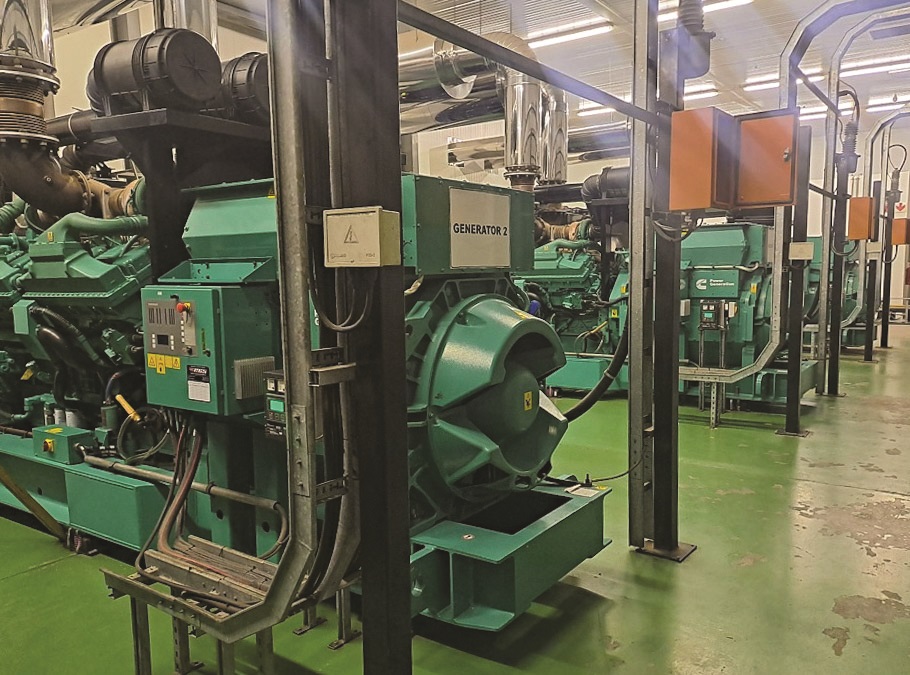
Objective
Cummins’ new Digital Master Controller (DMC8000) represents a leap forward in power plant control technology. Designed using cutting-edge PLC models, automation hardware, and software, the DMC8000 integrates Cummins’ proprietary logic design, which is customized to address the unique operational requirements of the customer. It includes the consideration of over 2000 failure mode sequences, enabling the DMC8000 to autonomously manage the power plant and make informed decisions, even in rare and extreme fault scenarios.
- Special consideration
- Coordination with the installation Electromechanically contractors was essential to understand the timing of the next power outage. This allowed planning for a direct swap without needing a temporary solution, which would be costly and time-consuming to install and test.
Solution overview
- Power system overview
- The system is 11 KV HV dual transfer pair controlled by the new Digital Master Controller DMC8000, 4 x11KV x1800KW DGs, 2 x 11KV Utility incomers, and 10+ downstream outgoing feeders.
- Key features
- The new DMC8000 panels provide faster communication and easier connections to the PLC. The larger front screen panel improves visibility and access, making the system more user-friendly for technicians and engineers. The upgraded system uses modern communication protocols, enhancing overall reliability and performance, and supports seamless integration with the PV renewable system.
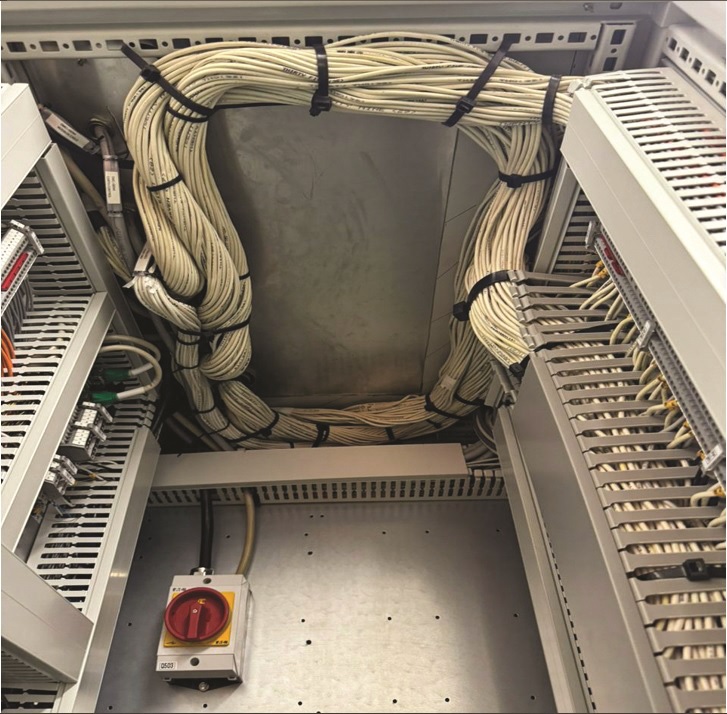
Implementation
- Project partners
- Cummins collaborated with an electro-mechanical contractor specialized in handling the high voltage installations.
- Installation steps
- Decommissioning the legacy DMC300 involved switching off all power from engine batteries, battery chargers, and power sensing fuses.
- Verification and confirmation of all power, control and communication cables against existing interface wiring drawings before disconnection.
- Removal of the old panel and installation of the new DMC8000.
- Labeling all existing cable terminals to ensure easy and accurate termination in the new DMC8000.
- Timeline
- The project was completed within a 2-weeks’ window. This involved decommissioning the existing panel, disconnecting all control cables, removing the DMC200/300, and installing the DMC8000. The new panel was then reconnected with the cables.
Results
Operational benefits:
- Advanced PLC models
- Utilizes state-of-the art PLC models that offer enhanced processing power and efficiency, allowing for more complex control algorithms and faster response times.
- Updated automation hardware
- Incorporates modern automation hardware components, ensuring reliability and longevity while supporting future expansions and upgrades.
- Enhanced software capabilities
- Includes a suite of advanced software features.
- Trends, events, and alarms history
- Stores historical data for up to 365 days, providing detailed insights into operational trends, events, and alarm logs for proactive maintenance and troubleshooting.
- Help screens
- Intuitive help screens guide operators through system operations and troubleshooting procedures, reducing downtime and enhancing operational efficiency.
- New load demand functions
- Optimizes load distribution based on real-time demand fluctuations, improving grid stability and energy efficiency.
- Enhanced graphical user interface (GUI)
- Features a redesigned GUI with improved graphics and visualization capabilities, offering clearer data presentation and a more user-friendly experience.
- Trends, events, and alarms history
- Includes a suite of advanced software features.
- Future-proof design
- Designed with scalability and future compatibility in mind, allowing seamless integration with renewable energy systems and accommodating technological advancements for years to come.
- Improved communication protocols
- Supports faster and more reliable communication between the DMC8000 and external devices, enhancing overall system responsiveness and coordination.
- Long-term support and spare parts availability
- Ensures continuity of aftermarket support and availability of spare parts for extended periods, mitigating risks associated with obsolescence and reducing maintenance costs.
- Customizable logic design
- Features Cummins’ proprietary logic design tailored to meet specific operational requirements, enabling flexible customization and optimization of power plant operations.
- Energy management optimization
- Optimizes energy management strategies, balancing operational efficiency with sustainability goals, and supporting compliance with environmental regulations.
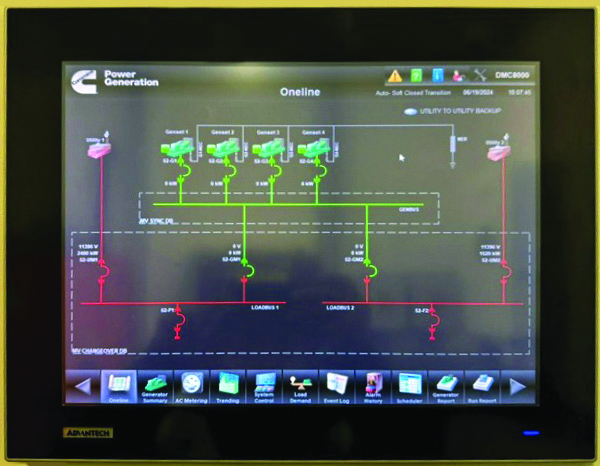
Customer feedback
The customer expressed high satisfaction with the upgrades and improvements provided by the DMC8000. They highlighted several key benefits:
- Improved user interface
- The new screen is more intuitive and provides easier access to vital information. Technicians and engineers find the enhanced GUI with better graphics much more user-friendly, allowing for more efficient monitoring and control. The integrated help screens are very useful in case of any doubts or operational questions.
- Ease of data access
- The setup allows for straightforward USB connection at the service port of the panel, facilitating easy report viewing and data extraction. Even USB printers can be easily configured to directly print the alarms and events log, streamlining the process of accessing operational data and logs.
- Enhanced connectivity
- The system offers simpler and more reliable connections to various components, including the factory SCADA system over the Modbus TCP/IP communication interface. This has significantly improved the ease of troubleshooting and fault-finding, reducing downtime and increasing the speed of maintenance tasks.
- Advanced software features
- The inclusion of trends, events, and alarms history, along with integrated help screens, has made it much easier for the customer’s team to manage and diagnose issues. This feature-rich environment supports proactive maintenance and improves overall operational efficiency.
- Aftermarket support
- With cutting-edge software and hardware features, the customer does not need to worry about parts availability for the next 15+ years, ensuring long-term reliability and reducing maintenance concerns.
- Future-proof design
- The customer is confident that the new DMC8000 will ensure long-term reliability and compatibility with future technological advancements, reducing concerns over obsolescence and enhancing the power plant’s sustainability.
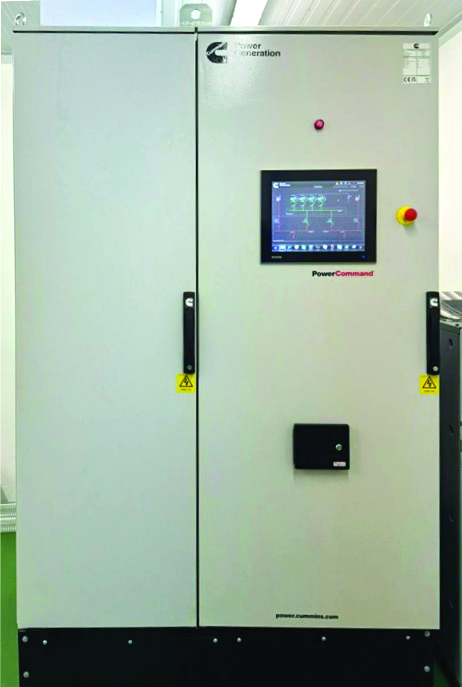
These advancements in the DMC8000 not only improve operational efficiency and reliability but also empower operators with enhanced control and monitoring capabilities, facilitating smoother and more efficient management of power plant operations.