The Future of Turbocharger Technologies in the Off-Highway Sector
The debate around turbocharger and engine technologies in the off-highway sector has historically been one that focuses on reliability and durability. Operators in these markets need to minimize the downtime of their equipment to ensure there isn’t a commercial impact on their businesses.
For example, mining companies face the challenge that they consistently need to identify and prevent issues in advance and pre-schedule periods of repair to mitigate against equipment failures, which may then impact on the ability of other stations to operate effectively. Although this remains a vital consideration for the sector, there are likely to be other changes in the market that Original Equipment Manufacturers (OEMs) of mining machinery need to prepare for, to ensure that their customers are ready for the future. Other off-highway applications face similar issues with equipment downtime having a direct implication on their operational efficiencies.
Where turbochargers for the off-highway market have focused on creating the most reliable and durable solutions previously, a bigger priority for the on-highway market in contrast has been compliance with environmental legislation. Government legislation has been in place for many years to ensure that vehicles are continually improving their fuel emissions and turbocharger technology is a primary consideration in meeting those targets. Although different regions around the world are at varying stages of this, the legislation does exist at a global level and turbocharger manufacturers have been preparing for this for a number of years.
This has led to an increase in focus for governments who will need to assess the off-highway market and analyze how machinery and equipment can achieve a greater reduction in their emissions to bring them in line with on-highway. With increasing costs of fuel, turbocharger manufacturers also need to address how their technologies can increase the efficiency of fuel in both on and off-highway. Thankfully we have reached the point at which turbocharger technologies can reduce emissions without reducing quality or workability in the off-highway sector.
Fuel Emissions & Off-Highway
As governments continue their efforts towards a low carbon community, it is only natural that other vehicles and fuel-consuming machinery (whether diesel or gas) will need to be addressed more rigorously. Although legislation exists for off-highway sectors, especially where equipment is in use on a 24/7 basis, they will need to look at all aspects of the engine to determine ways of reducing emissions by a more significant percentage. It may seem that all the hard work has been done from years of on-highway ‘practice’, but inevitably there are challenges to applying technologies designed for on-highway into an off-highway environment – the demands and usage of the equipment is so different and it isn’t a simple case of deploying the same solutions.
Fuel efficiency is the new priority
Fuel consumption is determined by the way that the fuel is burned in the cylinder and there are a number of ways that we can adapt the turbocharger to create both a cleaner and more efficient exhaust. Fuel efficiency is the new priority for the on-highway sector and, while previous emissions legislation drove new technologies, future emissions legislation and rising fuel costs will drive fuel economy by changing the constraint to CO2 reduction rather than NOx. This will naturally be a priority for off-highway as well, particularly when sectors such as mining use their equipment for continuous periods of time without a break.
The elements that can determine the amount of fuel consumed within such equipment include the variation in speed and load. In the high horse power market there is usually a variation in one or the other, and in mining this is likely to be in the load.
Supplementary systems installed on engines often work well when either the speed or load of the vehicle is stable. Examples of this are turbocompounding and Waste Heat Recovery, which may offer targeted and significant fuel savings but we are yet to see how cost effective they will be. There is no one size fits all solution though and OEMs need to ensure that they select the right solution for the right type of use.
Research and development experts at Cummins Turbo Technologies have spent many years developing these solutions, and we are already looking ahead to the future requirements of the market so that we are able to meet future demand as soon as it is required.
Rigorous testing in a range of environments
At Cummins Turbo Technologies, we rigorously test and trial technologies in a range of environments throughout the design phase to ensure that they are fit for market and meet stringent emissions standards while retaining their reliability and durability. We also spend time getting under the skin of how the equipment will be used so that technologies suit the operator’s usage. Operating as part of Cummins Components group, we are uniquely positioned to to design, test and supply integrated system solutions to optimize efficiency of turbo machines with aftertreatment and filtering, which helps deliver performance, emissions reduction and robustness in harsh environments.
New generation of turbochargers for 16 litres and above
Cummins Turbo Technologies have been able to utilize the technologies from our on-highway product to optimize for the off-highway market and therefore achieve greater savings on emissions and fuel efficiency. For example, the new generation of turbochargers for 16 litre and above applications, series 800/900/1000 has incorporated the latest turbocharger componentry, which will improve the efficiency of the turbocharger by 10%* and are engineered to meet the diverse duty cycles of this engine range.
Using such advances in technologies has allowed us to achieve the highest levels of turbocharger efficiency to date:
- Vaned and vaneless compressor stages allows tailoring of performance for various applications, pressure ratios, map width requirements
- Inverse impeller design uses state of the art software to develop the optimized blade shape resulting in the most efficient wheel for the chosen application
- High efficiency turbine design improves fuel economy and cost savings to the customer
- Super Map Width Enhancement improves drivability, improves fuel economy and improves map width by up to 15%
Preparing for regulations and rising costs
Although we don’t need to go back to the drawing board on the technologies that we could use to reduce emissions, we do need to undergo a period of bespoke testing for sector specific uses – often the turbocharger is put under far greater strain and is used continuously in the off-highway market - and it is inevitable that adjustments will need to be made.
OEMs for the off-highway sectors can prepare for this by starting to have those discussions now and by working collaboratively with their turbocharger partner to assess the options available before new legislation becomes imminent.
In essence, Cummins Turbo Technologies anticipates many changes ahead for engine manufacturers for the off-highway markets. We need to be prepared for future legislation and consider the challenges these sectors will face when developing these technologies. We need to consider the cost implications for mining operators in ensuring their machinery ticks the emissions box, while fuel costs continue to soar. More importantly, we must not lose sight of the core fundamental concern of the sector – to continue to minimize downtime. Our job, and challenge for the future as turbocharger manufacturers, is to create technologies that address these trends in the sector, but continue to perform robustly and remain reliable and durable.
* Figure is based on improvement against previous turbocharger products available
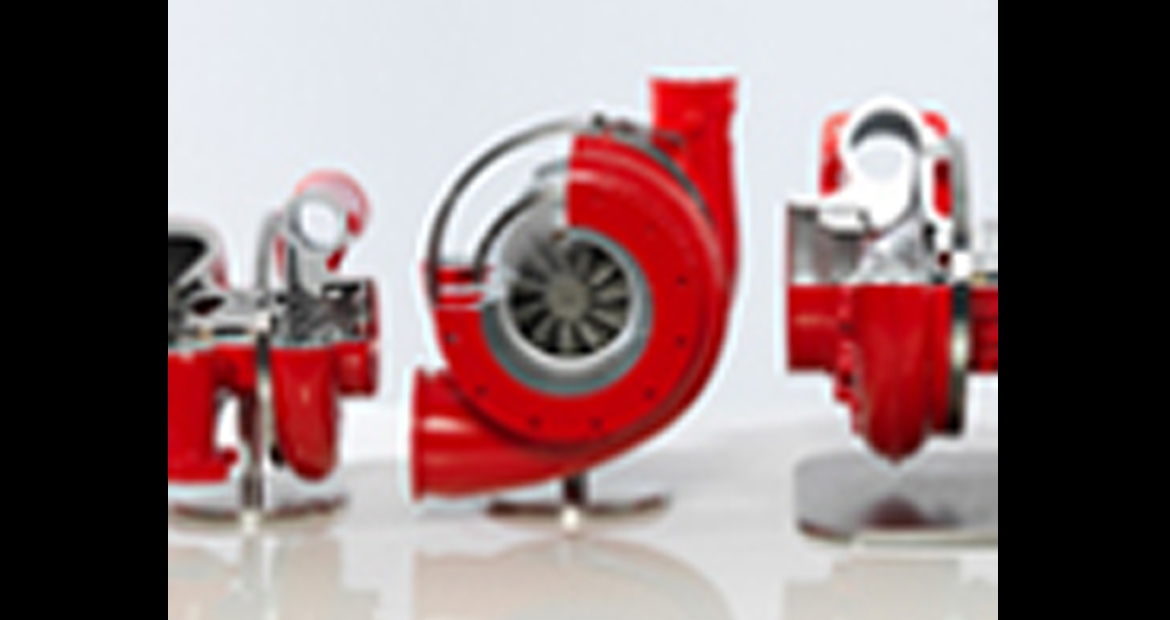