Surface Engineering of Turbomachinery Components to Meet Future Industry Trends
By Cummins Inc., Global Power Technology Leader
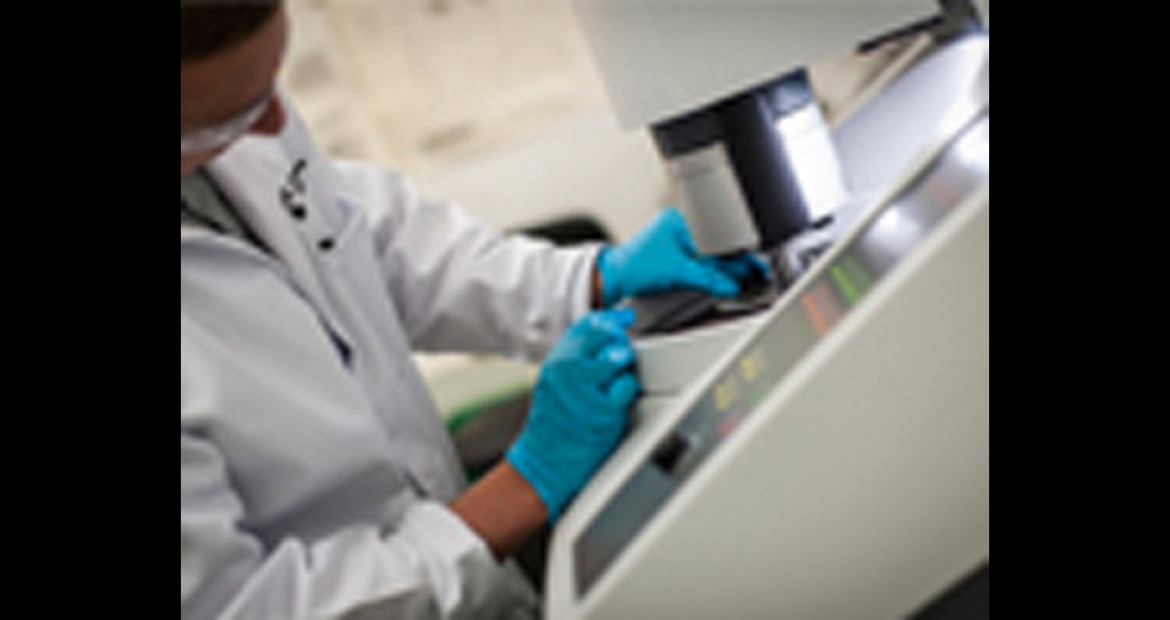
Novel Solutions for Materials Engineering
Increased demands are being placed upon turbochargers as a result of ever more stringent emissions regulations, a necessity for improved product performance and reliability and a requirement for a wider product operating range. Consequently, a greater level of stress is placed upon the materials from which turbochargers are manufactured. In order to achieve all of the necessary legislation and customer requirements, novel solutions to materials engineering challenges are being developed.
Two such challenges faced by the turbocharger industry are high temperature tribology and the corrosion and erosion environment generated by long route exhaust gas recirculation (LR EGR). Cummins Turbo Technologies has developed innovative materials engineering solutions using surface treatments applied to cost effective substrates, rather than utilizing much more expensive, exotic alloys.
High Temperature Tribology
As a consequence of experiencing excessive vane and slot wear whilst in service and experiencing temperatures > 500 °C, a thermochemical diffusion surface engineering solution was developed for variable geometry systems.
Such technology was generated using a systematic approach to tribological testing and analysis, which was pioneered by Cummins Turbo Technologies. After comprehensive evaluation of the problem using the expertise at Cummins Turbo Technologies, it was determined that during particular operating conditions the conventional uncoated nozzle and shroud plate experienced high levels of abrasive wear and elevated friction forces.
In order to solve the problem, a multi-disciplinary cross functional team at Cummins Turbo Technologies used the relevant customer and regulatory requirements to identify and develop the surface treatment concept. Using cutting-edge techniques, the fundamental mechanical and physical properties of the thermochemical diffusion treatment were determined. Subsequently, the surface treatment was characterized in terms of friction and wear performance using a tribometer, which simulated the variable geometry nozzle to shroud plate interface and associated operating conditions.
The surface treatment was tested on a turbocharger, on both gas stand and engine, with the results correlated to tribometer-based testing to ensure consistency of performance. This approach to the problem ensured that a robust engineering solution was identified and implemented into production; the resultant positive impact on nozzle vane wear performance can be observed.
Long Route Exhaust Gas Recirculation
The turbocharger compressor stage, which includes the compressor wheel and cover, is subjected to a corrosive and erosive environment when an engine is operating LR EGR. The chemistry and pH of the condensate present in the compressor stage varies depending on engine operating conditions and the chemistry of the fuel. Furthermore, the architecture of the LR EGR system dictates the density and size of erosive particles to which the compressor stage is subjected.
In order to minimize the wear and corrosion observed on the compressor wheel and cover as a result of interaction with condensate and erosive particles, surface treatments were developed for the two components. Numerous concepts for both components were identified using a multi-disciplinary cross functional team at Cummins Turbo Technologies, using regulatory and customer requirements as a guideline.
Subsequently, the concepts were subjected to numerous in-house tests which were developed using the expertise of Cummins Turbo Technologies:
Mechanical properties
Aerodynamic performance
Corrosion resistance
Erosion performance
Such experiments utilized surface treated test bars and also components in order to correlate the data from fundamental laboratory to turbocharger-based testing. The acquired data was analyzed using the expertise of Cummins Turbo Technologies and various advanced techniques, with the results input into a comprehensive scoring matrix in order to select the most appropriate solution for the two respective components.
The process developed for the compressor wheel was of an anodizing type, whereas a polymeric coating was developed for the compressor cover. As a result of the research and development work conducted, these technologies have been proven to significantly reduce the wear and corrosion observed on compressor wheels and covers subjected to LR EGR environments.
Experts at Cummins Turbo Technologies are continually developing novel solutions to materials engineering challenges in order to meet customer requirements for more robust and durable products.
Author Profiles
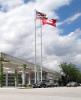
Cummins Inc., Global Power Technology Leader
Cummins Inc., a global power solutions leader, comprises five business segments – Components, Engine, Distribution, Power Systems, and Accelera by Cummins – supported by its global manufacturing and extensive service and support network, skilled workforce and vast technological expertise. Cummins is committed to its Destination Zero strategy – the company’s commitment to sustainability and helping its customers successfully navigate the energy transition with its broad portfolio of products. Cummins has approximately 69,900 employees and earned $3.9 billion on sales of $34.1 billion in 2024. See how Cummins is leading the world toward a future of smarter, cleaner power at www.cummins.com.
Related Tags