Cummins and Data Centers: At the Heart of It All
By Michael Nagel, Leader - Global Brand
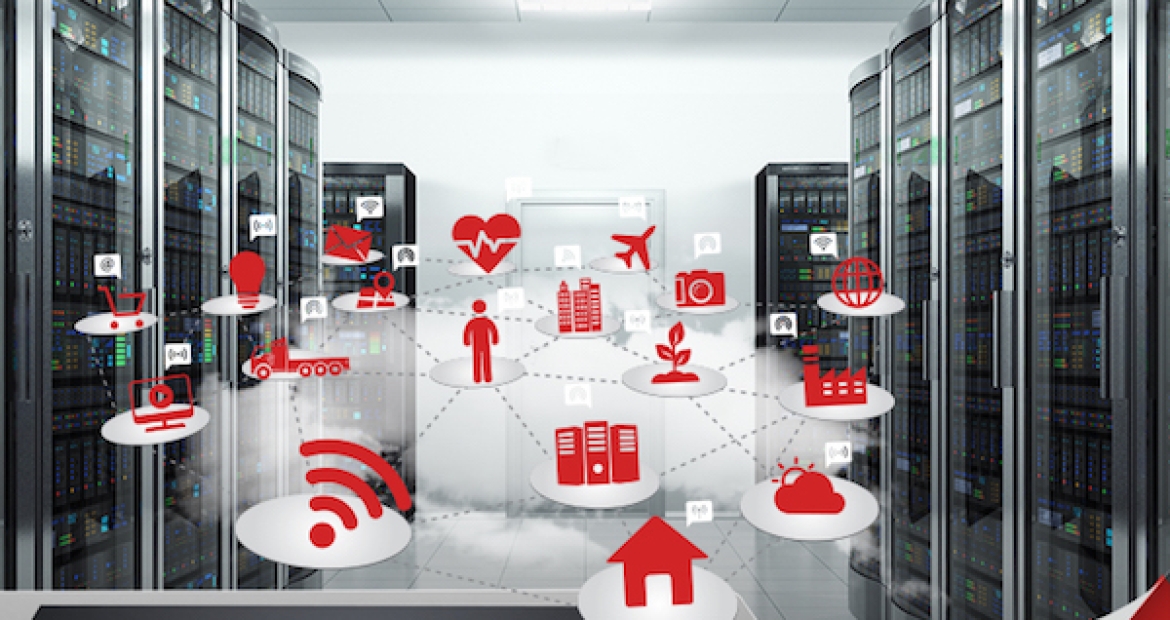
What once took shape as science fiction concept in books and movies, now riddles its way into day-to-day life: the Internet of Things (IoT). In the Internet’s short history, technology has leapt from clunky computers to wearable technologies like the iWatch, creating the web of connected “things.”
These ever-changing technologies not only bemuse the modern world but also give promise of a longer life filled with conveniences. With each connected thing, the IoT technologies collect and communicate data—lots and lots of data.
In order for the technology to function properly for any application, that data must be processed, stored and recalled in mere moments. For some instances that’s a matter of life or death, creating a dependence upon these technologies to run non-stop, rain, sleet snow and shine.
Data Centers: Powering the Internet of Things
When you’re transferring data over a network – be it via email, text or video – there’s a data center involved. Everything a consumer navigates on a smartphone or purchases at the point of sale at your local Target store? Stored at a data center. Individuals getting paid through financial institutions? Data centers. You might not realize it, but all of these data transfers rely upon well-maintained backup power sources to ensure a solid user experience.
Of course, it can be difficult to define was a good user experience actually is. What one person may expect or, conversely, tolerate varies from the next. Whether it’s a video on Facebook or a purchase at the point of sale in a brick-and-mortar store, today’s consumers demand quickness, reliability and dependability.
“If somebody were to ask how to describe a good user experience, it’s a difficult thing to put into words,” Brent Ness, Director of Mission Critical Accounts, Strategic Accounts with Cummins Power Generation says. “You know when you’ve had a one and you definitely know when you haven’t.”
Data centers around the globe rely on power and backup power to optimize those user experiences. But have you ever stopped to think, “Wait a minute. Who…or what…is powering the server that hosts my home security system, email client and favorite social networking site, and what happens when the power to that server is interrupted?”
In today’s information-driven economy, where machine-to-machine communication continues to grow, data centers are the backbone of modern business – and power is the lifeblood.
When an electrical storm swept through the United States’ eastern region in 2012, customers and end users of one of the largest cloud computing companies in the world quickly discovered what a bad user experience was. The storm took out utility power in the area where several datacenters were located. Inside the company’s regional facility, power failed to switch to generator power—likely ill maintained. As a result, popular services such as Netflix, Instagram, Pinterest and Dropbox faltered that night, which resulted in poor user experiences and extremely unhappy customers.
“If Amazon or Facebook loses power, it makes the news,” Ness says. “And businesses don’t want to be any part of that.”
"Reliability is a must for backup power in data centers. Unplanned downtime...costs an average of $7,900 per minute in the United States"
Companies spend immense amounts of resources—financial and otherwise—to negate data center outages to get latency down and to provide a good consumer experience.
“When all goes well, you never know,” Ness says. “During Hurricane Sandy, one customer’s generator power ran for two weeks. The only problem they had was keeping the generators fueled.”
Reliability is a must for backup power in data centers. Unplanned downtime not only muddies a good user experience it costs an average of $7,900 per minute in the United States.
Life-Saving IoT Technologies
Your favorite social networking site going down for several hours isn’t a life or death situation – although sometimes it might feel that way. But emerging and evolving data technologies present major implications for health care. From fitness trackers like the FitBit and iWatch to a sensor-equipped pacemaker, the possibilities are tremendous.
There will be 80 million wearable health devices within the next two years, according to Hospitals & Health Networks Daily. The more data that these devices collect, the more possibilities flourish into actual application. Today, if a patient’s pacemaker fails or trips at any level, it immediately alerts emergency personnel. Without the patient needing to pick up a phone and often times without even knowing he or she was in danger, an ambulance can arrive at the patient’s precise location.
A fetal monitor can alert an OB/Gyn of a patient and baby in crisis, commencing an orchestration of life-saving activities. For a diabetic who must rely on daily finger pricks to measure blood glucose levels, an implanted insulin regulator could trigger medical action and also greatly improve his or her quality of life. Thus is the beauty of the IoT.
But data centers that power hospitals and healthcare-related technologies require constant uptime. While data center designs, requirements and specifications are as varied as the industries they support, one thing remains constant: In an ever-connected world, uptime reliability is the ultimate objective.
Backup Power: The Data Center's Life Support System
That’s the dance of these technologies: some innovators seek to improve comfort and convenience over the clinical and life-saving possibilities. In either case, users have become dependent on the data-collecting technologies, and those technologies depend upon the power of Cummins.
A mobile app can control the air temperature in a user’s home from miles away—a virtual thermostat. Colleagues from across the globe can collaborate online and video-chat from nearly any wired or wireless device. If you can imagine it, likely you can connect it to the IoT.
The world has evolved with these technologies, and people now have access to global information in real time. In order to keep up that hyper-dependent level of information processing, data centers must run around the clock, without a moment’s loss of uptime. And Cummins Power Generation provides no-break, backup power to these data centers, maintaining uptime that their consumers demand. For mission-critical data centers that act as the heart of the IoT movement, aspiring to 99.999 availability is the ultimate goal.
Author Profiles
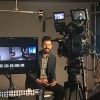
Michael Nagel, Leader - Global Brand
Michael Nagel is the Leader - Global Brand at Cummins Inc. As a member of the external communications team at Cummins, he has more than 15 years of digital communications and traditional public relations experience, with a focus on digital communications, corporate brand and content marketing. Michael earned his B.A. from the Indiana University School of Journalism - Indianapolis and currently resides in Indianapolis.
Related Tags