7 Ways Cummins Goes High Tech to Power its Customers
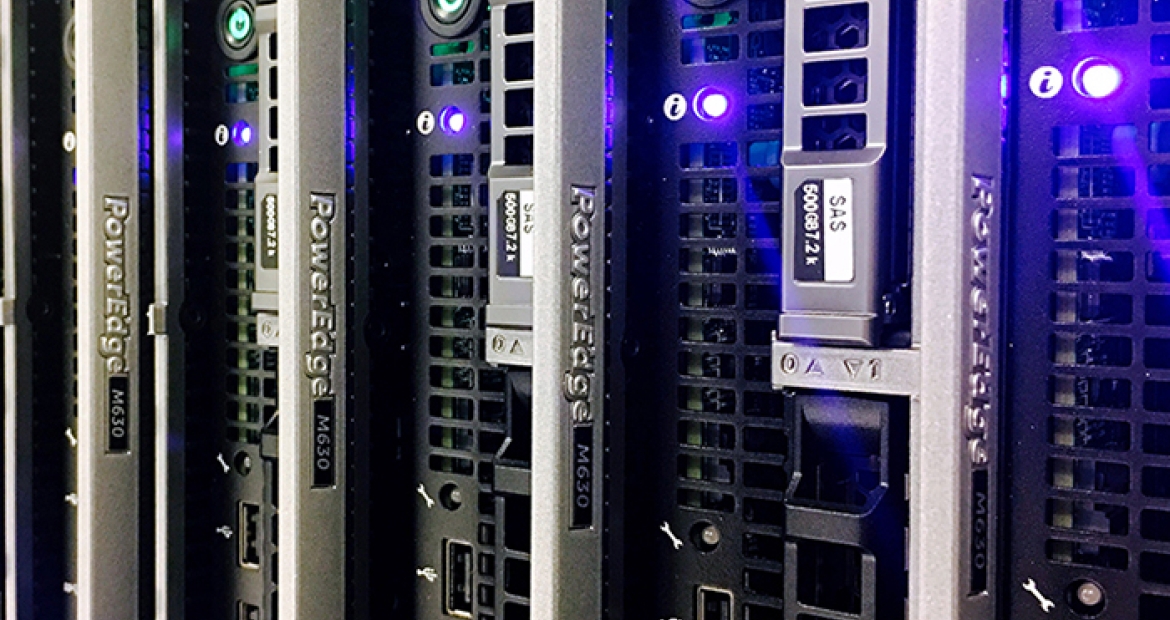
IN MANY WAYS, CUMMINS ENGINES AND RELATED PRODUCTS ARE MORE COMPLEX THAN YOUR SMART PHONE. HERE'S SEVEN WAYS CUMMINS PUTS HIGH-TECHNOLOGY TO WORK FOR YOU:
SUPER COMPUTERS
The Clessie 2.0 supercomputer is a critical asset to the company’s engineering function, accelerating innovation, improving productivity and reducing product development time as well as costs.
With approximately 1.4 petabytes of total storage, 8,584 cores, 355 teraflops of computational muscle, and built to double in capacity, it enables engineers to explore thousands of computer assisted design (CAD) options on demand. Traditionally, an engineer could only explore a small number of design options.
The combination of engineering expertise, robust software, and powerful computing enables Cummins to produce the best engines in the world.
3D PRINTING
3D printers take extremely detailed instructions to make precise objects a layer at a time, with relatively little waste. The technology is primarily used at Cummins to help engineers make detailed prototypes of the engine parts they design, and do it faster and more accurately than ever before.
Prototypes can be made from materials strong enough to put in a working engine for testing, which ultimately means great ideas can get to market faster.
CONNECTIVITY AND BIG DATA
Immediate Assessment, for example, enables service providers to wirelessly connect to an engine through their smart phones or tablets. A feature of Cummins’ new Guidanz™ mobile app, it can pull fault codes indicating the most likely cause for a check engine light and estimate repair time based on data from thousands of similar repairs. In the past, customers could wait hours just to learn what was wrong.
Telematics devices, meanwhile, allow Cummins to gather extremely large sets of data about how Cummins-powered products operate. Company experts can then analyze that data to create digital solutions to customer challenges. With this technology, we can also remotely monitor Cummins-powered products and send software updates to them over-the-air.
In June, Cummins launched a new company, ZED Connect, to help carriers and drivers use data and analytics to increase their bottom lines. The new company’s first product is a simple and low-cost electronic device, ZED ELD, to help fleets and operators log their hours electronically.
VIRTUAL REALITY
Formally known as the CTC’s Advanced Virtual-prototyping Environment, the facility is one of several virtual reality centers across Cummins. Making it easier to see the intricacies of a big engine like those used in heavy-duty trucks or trains can be critical to engine uptime. It allows designers to know early on when a part is difficult to reach if a repair is necessary.
It can be important for engine components, too. The CAVE played a key role in development of Cummins’ ultra-efficient Single Module exhaust aftertreatment, helping engineers with both the design and the chassis installation requirements for the system, which is up to 60 percent smaller and up to 40 percent lighter than its predecessor.
ELECTRIFICATION
Cummins is currently in the midst of multiple electric mobile and stationary power projects. In the spring of 2016, the company announced it was part of a project awarded a $4.5 million grant from the U.S. Department of Energy to develop a Class 6 commercial plug-in range extender electric powertrain that could reduce fuel consumption by at least 50 percent over a conventional Class 6/7 delivery truck.
ELECTRON MICROSCOPES
Roger England, the Cummins Technical Center’s Director of Materials Science & Technology in Columbus, Indiana (U.S.A.), said that tool and others enable his team to work in the realm of atoms as it investigates problems like why a certain kind of oil might wear down an engine part and what metals might be less susceptible to damage.
OUR PEOPLE
About a third of the company’s professional staff has degrees in Science, Technology, Engineering or Math (STEM). Many at the company’s tech centers have PhDs.