Cummins Manufacturing: Doing More to Use Less
Manufacturing and environmentalism don’t often go together. But at Cummins, the two are increasingly working in harmony to help meet the world's demand for goods and services while using fewer of its resources.
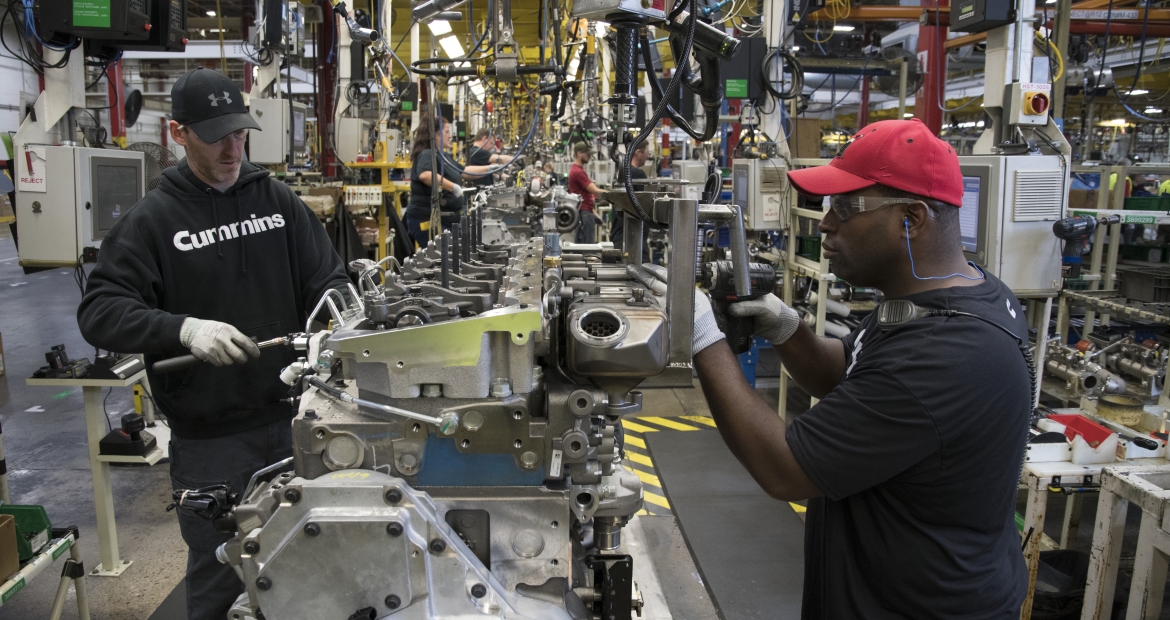
The company, for example, expanded its use of the latest technology to capture energy from engine test cells for use at its plants. Cummins is steadily adding high-efficiency LED lighting at its manufacturing facilities, also enhancing safety. And the company recently installed solar panels at its plant in Juarez, Mexico, joining plants in Jamestown, New York; Beijing, China; and eight other Cummins’ locations drawing some of their power from the sun.
These and other steps by the company’s manufacturing operations, working with Cummins’ environmental team, are helping the company make progress toward its 2020 goals to reduce the water and energy it uses and the waste it produces.
“Our mission to build a more prosperous world can only happen if we take steps now to protect and preserve the environment,” said Tim Millwood, the company’s Vice President of Global Manufacturing. “While I’m proud of the progress we’ve made, there’s definitely a lot more we can do.”
GOAL-DRIVEN RESULTS
The company announced its first public greenhouse gas reduction goal in 2006 and set additional public goals for water, waste, logistics and products-in-use in ensuing years. Currently, Cummins’ targets around water, waste and energy are timed to 2020, but future goals are expected to be announced soon.
Manufacturing leaders have been all-in from the beginning. Relatively easy steps came first, such as investing in LED lighting. Then came controls to use water and energy only when needed, addressing more hidden inefficiencies.
The creation of a group Cummins initially called its Energy Champions and now calls its Environmental Champions has played a key role, said Alan Resnik, Director of Environmental Management for Facilities and Operations at Cummins. About 1,000 employees from across the globe have been trained to look for savings in water, waste and energy at their plants and facilities. They’ve fixed leaks, replaced inefficient equipment and changed practices. Collectively, the improvements have made a big difference.
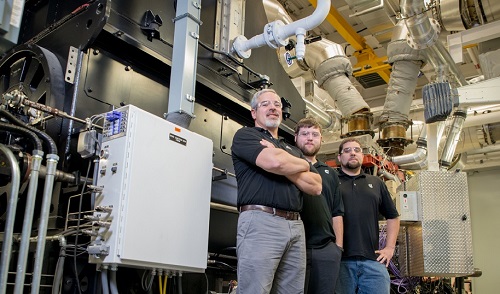
Finally, the company has invested in big ticket items such as regenerative dynamometers, also known as regen dynos. One of the biggest uses of energy at Cummins is engine testing. The engines can run for hours, requiring large amounts of fuel. The newest regen dynos capture the energy generated during testing so it can be used at the plant or sent back to the grid. They also use much less water for cooling than conventional dynos.
The latest dyno technology was recently installed at plants in Brazil, India and the United Kingdom. At Cummins’ Seymour, Indiana, Engine Plant, where the company builds some of its biggest engines, the regen dynos generate about 20 percent of the plant’s electricity needs.
These and other steps have led to:
• A 25 percent reduction in energy intensity (energy use adjusted by hours worked) across Cummins toward a 2020 goal of a 32 percent reduction using 2010 as a baseline.
• A 47 percent direct water use reduction, adjusted by hours worked, compared to 2010. Cummins’ 2020 goal is a 50 percent reduction.
• The company is nearing the half way point for converting lighting to LEDs and has completed dozens of projects to increase Cummins’ use of returnable and recyclable packaging.
“We're using less water and energy. We're producing less waste,” said Brian Mormino, Executive Director of Worldwide Environmental Strategy and Compliance at Cummins. “And we are saving millions of dollars every year while mitigating risks.”
A PROMISING FUTURE
Manufacturing leaders say future innovations hold tremendous promise. The company, for example, is working on a system at its Rocky Mount, North Carolina, Engine Plant that will capture all the water used on site and recycle it for heating, cooling and other non-potable uses.
Additive manufacturing, sometimes referred to as 3D printing, also could make a big difference. It creates three-dimensional objects one ultra-thin layer at a time. Elizabeth Hoegeman, Executive Director of Global Manufacturing Engineering at Cummins, said the process should reduce waste by eliminating the need for molds and dies to create a part.
Perhaps more importantly, 3D printing can make it much faster for new ideas, including those beneficial to the environment, to be designed, tested and adopted, Hoegeman said. While the technology is still developing for high volume industrial use, Cummins’ remanufacturing in Mexico recently sold its first 3D printed part.
Finally, Cummins is looking to see if tools such as computer-based Analysis Led Design and improvements in quality control might enable the company to reduce the time engines run in test cells.
While there are many challenges ahead, Millwood says this is an exciting time to work in manufacturing.
“What we make and how we make it will help shape what our world looks like in 2050 and beyond,” he said. “That’s an awesome responsibility, and a tremendous opportunity.”
Related Tags