Henok's focus on quality makes him the perfect fit
By Lauren Cole, Senior Digital Communications Specialist
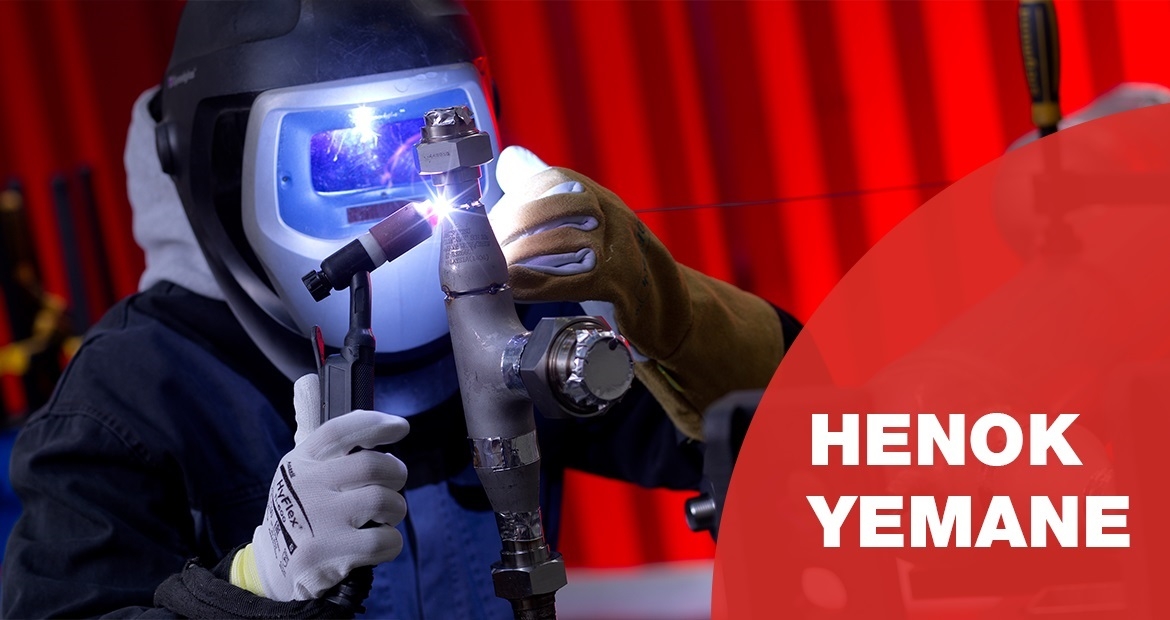
Henok Yemane has been laser-focused on quality for the past 11 years. As one of Cummins' certified welders (both ASME IX and EN ISO 9606-1 - American and European welders accreditation standards), Henok is responsible for ensuring the piping on Cummins electrolyzer meets international welding standards.
Despire working on time-critical prototypes and high customized jobs, Henok never lets weld quality or standards slip.
A (Welding) World of Opportunities
Working as a welder in the Cummins Oevel, Belgium facility since 2009, Henok's eye for detail has led him to be responsible for many special welds, including TIG/GTAW welding on stainless steel pressure piping and stainless steel pressure vessels used in Cummins electrolyzers.
Every weld requires a high level of detail and precision to ensure that critical components in Cummins electrolyzers (cell stacks, safety valves and sensors) are safe from damage cause by debris, metal dust, cutting oils or corrosion.
Recently, a high-end gas metal arc welding (MIG/GMAW) capability was added to the welding facility in Belgium, and Henok is now certified to weld piping in several thicknesses and diameters. The piping is used to transport several substances, including highly corrosive potassium hydroxide, hydrogen and oxygen gasses. The working pressure of the piping is typically 10 to 30 bar/145 to 435 PSI at a working temperature of 70° C (160° F). Other applications require higher pressure, such as for fueling where the pressure can rise to 1,000 bar/14,500 PSI.
Delivering our Brand Promise of Innovation and Dependability
Each weld is closely monitored to ensure the highest quality. Before welding begins, a cleaning procedure is implemented. During the weld, the oxygen content of the pipe is monitored to prevent discoloration. After welding, a visual check of both the inside and outside of the pipe takes place. A liquid penetrant test and pressure test then endure the weld quality and cleanliness. Once Henok and his colleagues are satisfied, an independent inspection agency inspects 10% of the welds with X-rays as final confirmation that the weld is sound. The slightest defect, such as an incomplete fusion of only 0.1mm (0.004 inches), will be detected.
X-raying out welds gives us complete confidence that our quality is high and there will be no issues out in the field.
Over a three-year period, only three welding errors have been detected across the complete output of the welding team. With several thousand welds each year, this is something Henok and his team is incredibly proud of.
Working Across the Globe
Not only is Henok responsible for each of the welds in the Oevel facility, he also visits customers across the globe to perform special welds on site. For Henok, completing a difficult job on site located in Russia is one of his proudest achievements. "Several units needed complete refurbishment with limited downtime for the customer. With temperatures between -10°C and +40°C (14°F and 104°F) ambient in the improvised workshop, creating custom piping on site was challenging," says Henok. Despite these challenges, Henok completed the job to perfection.
Since beginning his career in 2009, Henok has also had the opportunity to visit Germany, Turkey, Argentina, Abu Dhabi and Uganda to carry out specialized welds at customer locations.
What does the future hold? Henok would like to use his skills to train new welders in this extremely precise field. He describes himself as a team player and says that his aim is to always help and assist colleagues as much as possible. When asked what motivates him each day, Henok says,
The best feeling is knowing that my work is of the highest quality and going home and feeling that my contribution to the company was successful.
Henok looks forward to his next challenge and continuing to ensure the highest level of quality on every product that passes through the welding facility.
Interested in learning more about New Power at Cummins? Explore our careers.
Want to hear more from members of Cummins' New Power team?
Author Profiles
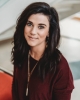
Lauren Cole, Senior Digital Communications Specialist
Lauren is the Senior Digital Communications Specialist for Cummins Inc, where she focuses on social media, employee storytelling, and employer branding. Lauren joined the company in early 2017 and has a Bachelor of Science in Marketing from Indiana University.
Related Tags