Overcoming pandemic challenges to power large-scale data center project in Middle East
By Anisha George , Marketing Communications Specialist
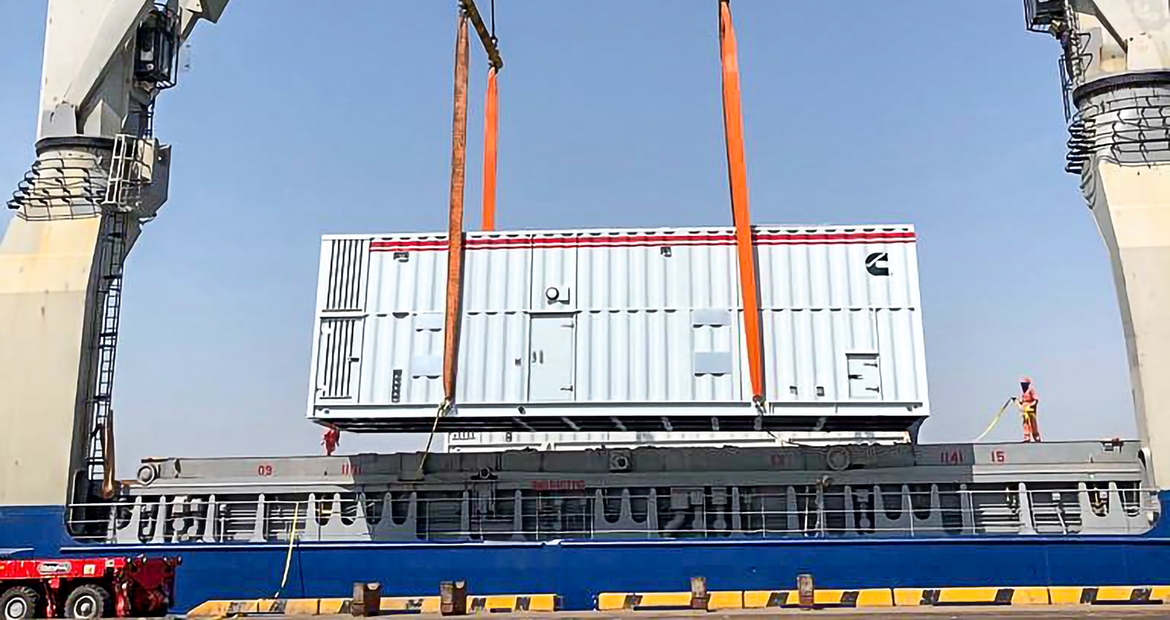
No doubt the COVID-19 pandemic has brought countless unexpected variables with an extended effect on projects’ life cycles including supply chain, manufacturing and testing.
At the end of 2019, Cummins Africa Middle East was contracted by a leading provider of cloud and computing web services to supply nine (9) C3000D5E units enclosed in customized acoustic enclosures, extending the system that was delivered in 2018 and shown in this video.
Leveraging strong relationships, global resources and innovative solutions, the team achieved on-time delivery. Key to the success of this high-profile project was pre-order engineering expertise, leading emission technologies, competitive pricing, regional and global support.
With the first phase completed, many challenges had to be addressed in Phase 2 even before the pandemic. The delivery schedule was very tight, which necessitated that the design improvements happened concurrently while enclosures were being built. The generator sets packaging process inside the acoustic enclosures had an early start based on the customer’s strategic global requirement, and the team reviewed the project’s delivery schedule to find areas to expedite the build to meet the customer’s delivery milestones.
The fabrication and delivery schedule was complicated after the start of COVID-19 restrictions impacted availability of staff and materials, along with restricted access to the build oversight. Adding difficulty was the travel restrictions imposed due to COVID-19 pandemic. In place of a more effective and easy face-to-face meeting, the Cummins team had to rely solely on virtual meetings with the design and factory teams at manufacturing plant for the process of issue identification, redesign and improvement implementation.
During the pandemic, members of the Commissioning team worked at the vendor’s premises to test the full integration of the generator package inside the acoustic enclosure. After completing all the internal tests, the team conducted a three-day virtual witness test with the customer remotely. The team used three cameras to stream the test from all angles to enable the customer to witness the test. Moreover, the whole virtual test was video recorded, and the video was shared with the customer. The customer witness test included 12 hours’ full load test in addition to the functional tests for all the other subsystems.
“The Project Delivery and Implementation Commissioning team is always in the frontline supporting customers to test, commission and deliver power on time,” said Dany Adam, Director - Power Generation Business AME “The team is hard at work behind the scene with the target to support the customers to be Always On.”
The customer was satisfied with the generator performance and factory acceptance test setup and process, which is a remarkable success. Cummins executed, tested and delivered the project on time to a strategic customer despite the operational, logistical and mobilization challenges brought on by the COVID-19 pandemic.
Author Profiles
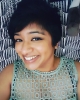
Anisha George , Marketing Communications Specialist
As a Marketing Communications Specialist, Anisha supports marketing, communications and event management for Africa and Middle East regions. Prior to joining Cummins in 2011, she gained industry experience working in the event management field. anisha.george@cummins.com
Related Tags