Digging Deeper: Two aspects of improving productivity of mining operations
By Aytek Yuksel, Content Marketing Leader - Power Systems
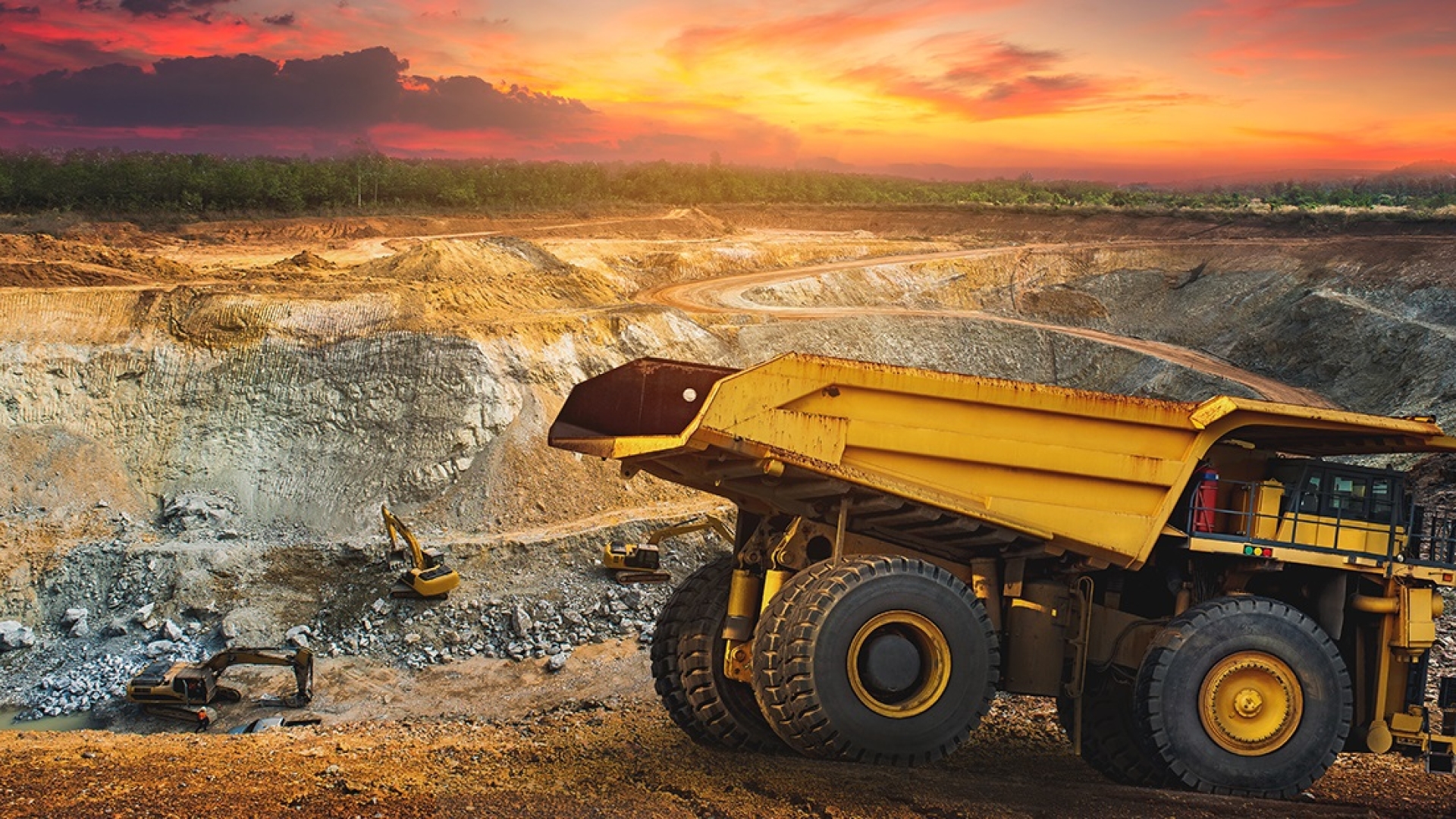
Let’s define productivity as getting the job done faster, and increased productivity helps miners do more with less. In the mining business, productivity is sometimes less space being consumed by an engine, leaving room for more payload or less time to accelerate, thus maximizing the number of trips a day.
Miners have several opportunities to improve their operational productivity; below focuses on two opportunities most relevant to increasing productivity of equipment ranging from haul trucks to excavators.
No. 1: Extended maintenance intervals deliver higher productivity
The longer miners can run their equipment, the higher their productivity is. In most cases, mining equipment operates near continuously through days, weeks and months, and this creates the need for periodic maintenance events for filters, fluids and beyond. In this quest towards higher productivity, even these periodic planned maintenance events are open to questioning.
No.2: Engines capable to do more with less even in most extreme conditions
Miners are familiar with extreme conditions whether it is the elevation, temperature or accessibility, and understand how these conditions impact the performance of their equipment. For instance, reduced oxygen in high altitude locations result in losses in engine power; resulting in overall reduced mine productivity. Loss of engine power could lead into more trucks doing the same work or work being done slower, and neither are good solutions. More trucks would mean increased carbon footprint while doing the work slower means low productivity.
Cummins engines accept the challenge of extreme conditions in a variety of applications at China’s largest copper mine site. Located at an altitude of 5,500 meters, higher than the base camp for Mt. Everest, the Julong Copper Mine features over 65 Cummins engines powering excavators, dump trucks, power generators, drillings and bulldozers. Haul trucks powered by Cummins QSK60 engines have continuous uptime in this severe environment, making it the top engine of choice at Julong.
“The mining industry will continue to find solutions to improve the productivity of its operations. Some of these, such as the extended maintenance intervals and engines capable to do more with less, will help miners both on sustainability and productivity fronts, a double gain for the industry,” said Steve Cummins, Director of Mining Business at Cummins.
To learn more about trends in the mining industry follow us on Facebook and LinkedIn. To learn more about mining power solutions Cummins offers, visit our webpage. To learn more about how Cummins is powering a world that’s “Always On,” visit our webpage.
Author Profiles
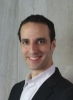
Aytek Yuksel, Content Marketing Leader - Power Systems
Aytek is a marketing leader at Cummins, focusing on technology and thought leadership. Since joining in 2008, he has held various marketing roles and now shares insights on markets, technologies, and energy transition. Aytek lives in Minneapolis with his wife and two kids.
Related Products