Reducing greenhouse gas emissions of engines in the oil and gas sector for improved sustainability
By Aytek Yuksel, Content Marketing Leader - Power Systems
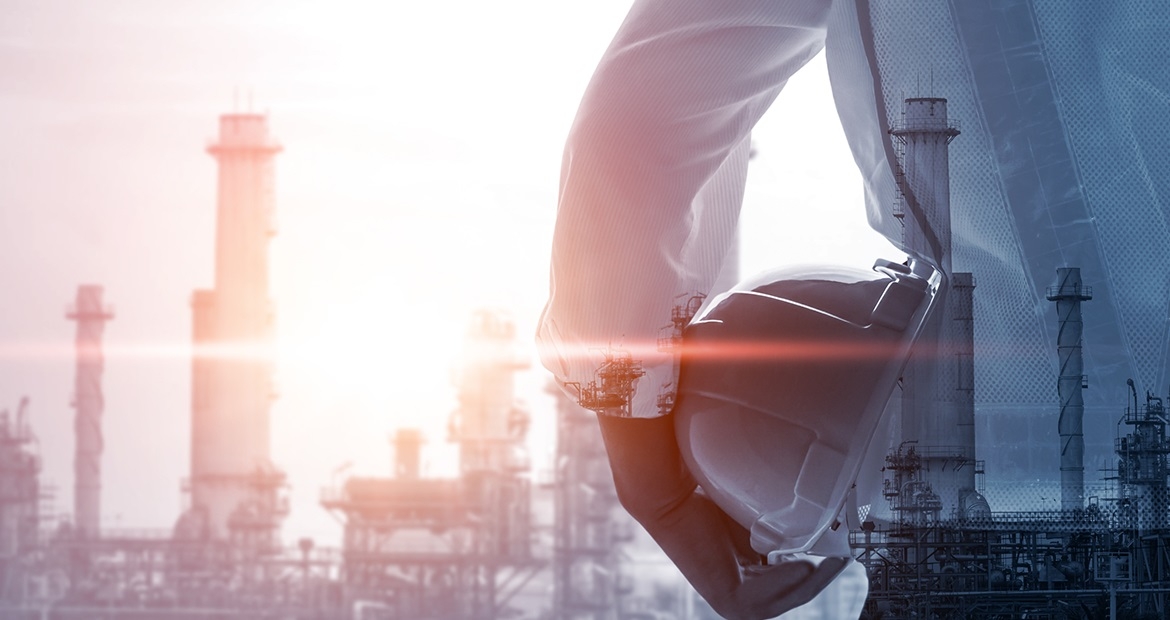
The oil and gas sector’s environmental footprint differs between its upstream, midstream and downstream activities. For midstream, refineries collectively represent the majority of greenhouse gases (GHGs) emitted in this stage of the processing. On the other hand, many different activities contribute to the sector’s GHG emissions produced during upstream processing. These activities range from onshore production and gathering, to natural gas processing. In fact, a collection of these upstream activities makes up over 10% of GHG emissions of the industrial sector in the U.S.1
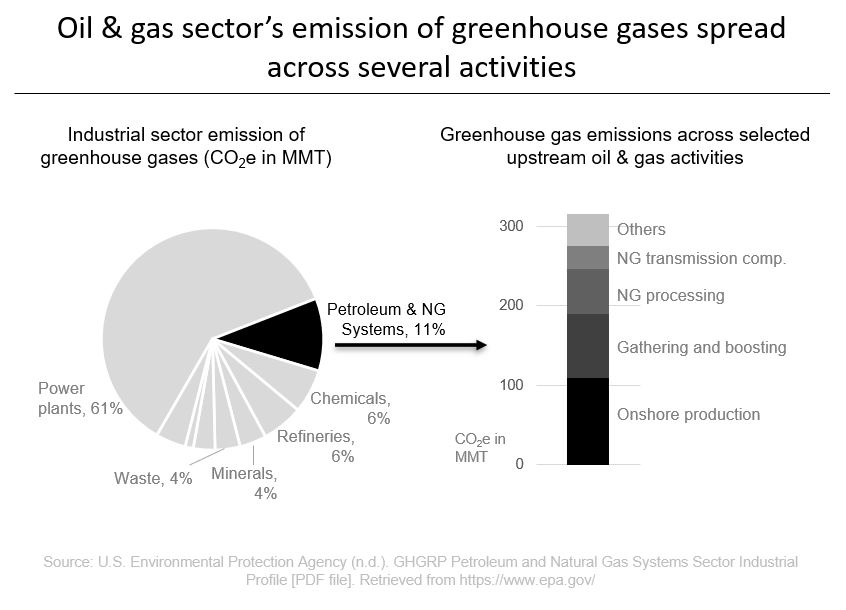
For the rest of this article, we will focus on upstream oil and gas activities, ways to reduce greenhouse gases emitted from engines, and power systems used across upstream activities. From drilling contractors to oilfield services companies, GHG reduction is getting more traction, driven by a combination of regulatory and societal factors.
A good starting point in reducing emission contaminants within upstream oil and gas activities is diesel engines. There are many emission regulations focused on reducing diesel engines’ environmental footprint; you can read more about these regulations in our previous article. Let’s start with diesel engines and reducing emissions.
Diesel engines’ emissions are significantly reduced with Tier 4, and equivalent emission regulations
In recent decades, the diesel engines’ emission contaminants have been significantly reduced through various regulations. For instance, Tier 4 high-horsepower diesel engines used within oil and gas applications emit 80% less particulate matter, and 45% less NOx compared to their Tier 2 counterparts. These reductions also translate into financial gains; check how operators saved over $30 million in fuel, and avoided enough pollutants to fill a 15-mile long train through these Tier 4 solutions.
Most recently, two technologies have been adopted by the industry to achieve these ultra-low emissions with diesel engines: selective catalytic reduction (SCR) and exhaust gas recirculation (EGR). While there are many technical differences between the two technologies, there is one key distinction between them: SCR is considered a post-combustion solution, while EGR is considered an in-cylinder solution to reduce the amount of contaminants released into the atmosphere.
Engines with SCR technology often consume less fuel than engines with EGR technology, delivering fuel savings for their owners
Engine manufacturers could reduce combustion temperature to lower the emission of certain contaminants, but reduction of engine temperature often increases fuel consumption. SCR technology reduces NOx emissions external to the engine, without the need for reducing combustion temperature. With the higher combustion temperature allowed by SCR technology comes lower fuel consumption for operators.
Implementation of SCR technology introduced minimal changes in engine design, helping you leverage the proven technologies you already rely on
Engineers had to introduce minimal architectural changes in existing engines to accommodate the SCR technology, since it is external to the engine. This means the reliability of existing engines proven through millions of hours of operation remain available to you. Plus, since this is a technology external to the combustion chamber, you can upgrade your older engines to meet the newer emission standards often required by exploration and oilfield service companies to contract on different sites.
Newer engines with SCR technology and their older versions have many common parts, making it more efficient and cost effective to maintain
Limited architectural changes from previous engines to the most recent engine platforms mean a higher degree of commonality when it comes to parts. Moreover, technicians who work with these ultra-low emission engines in oil fields can carry forward their familiarization with previous generations of engines.
Beyond diesel, emission reduction is also achieved through gaseous and renewable fuels
Emission regulations and associated technologies covered above have greatly reduced the emission of contaminants from diesel engines. Meanwhile, there is another path ahead in reducing emissions in a drilling or well site: use of fuels beyond diesel.
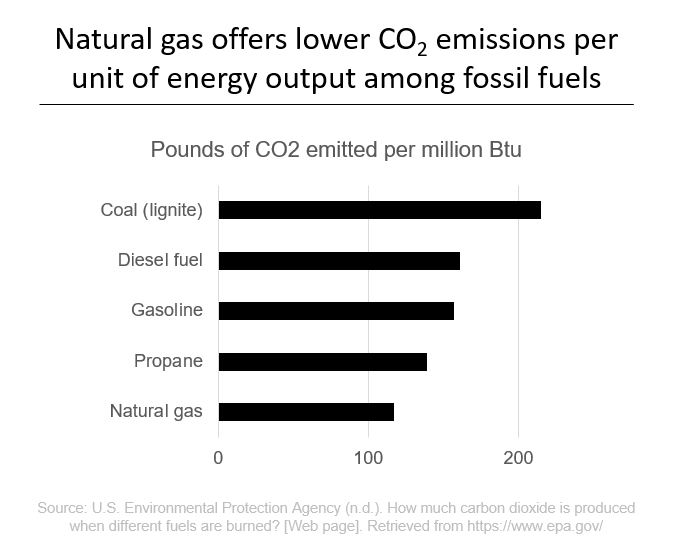
Gaseous fuels, including natural gas, often reduce the emission of GHGs compared to diesel. For example, natural gas has one of the lowest CO2-to-energy content across all fossil fuels2. Moreover, natural gas engines often have much less Sulfur and NOx emissions than comparable diesel engines. On sites where there is an unlimited supply of natural gas, this also could translate into financial savings in the form of operational expenses (OPEX).
Renewable fuels, including solar and wind, are the final destination and getting increasing attention within the oil and gas sector. For instance, ExxonMobil and Ørsted have entered into an agreement in 2018 for Exxon to source over 300MW of renewable power from over 100 wind turbines for its operations within the Permian Basin3. These renewable fuels offer carbon zero power for drilling and well sites.
Diversification will be the key word in the next couple of decades when it comes to energy and power solutions within upstream oil and gas operations. It is forecasted that a diverse set of fuels and technologies ranging from diesel and hydrogen, to renewables will co-exist to deliver the reduced environmental footprint in a manner that is financially manageable by oil and gas sector players.
Sign up below to receive periodic insights, updates and news relevant to the oil and gas industry. Learn more about oil and gas power solutions Cummins offers.
References:
1 U.S. Environmental Protection Agency (n.d.). GHGRP Petroleum and Natural Gas Systems Sector Industrial Profile [PDF file]. Retrieved from https://www.epa.gov/
2 U.S. Environmental Protection Agency (n.d.). How much carbon dioxide is produced when different fuels are burned? [Web page]. Retrieved from https://www.epa.gov/
3 Orsted (n.d.). Our onshore wind farms in the U.S. [Web page]. Retrieved from https://us.orsted.com/
Author Profiles
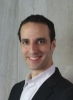
Aytek Yuksel, Content Marketing Leader - Power Systems
Aytek is a marketing leader at Cummins, focusing on technology and thought leadership. Since joining in 2008, he has held various marketing roles and now shares insights on markets, technologies, and energy transition. Aytek lives in Minneapolis with his wife and two kids.
Related Tags