No paint? No problem. 6.7 turbo diesel engine ditches clear coating for improved sustainability
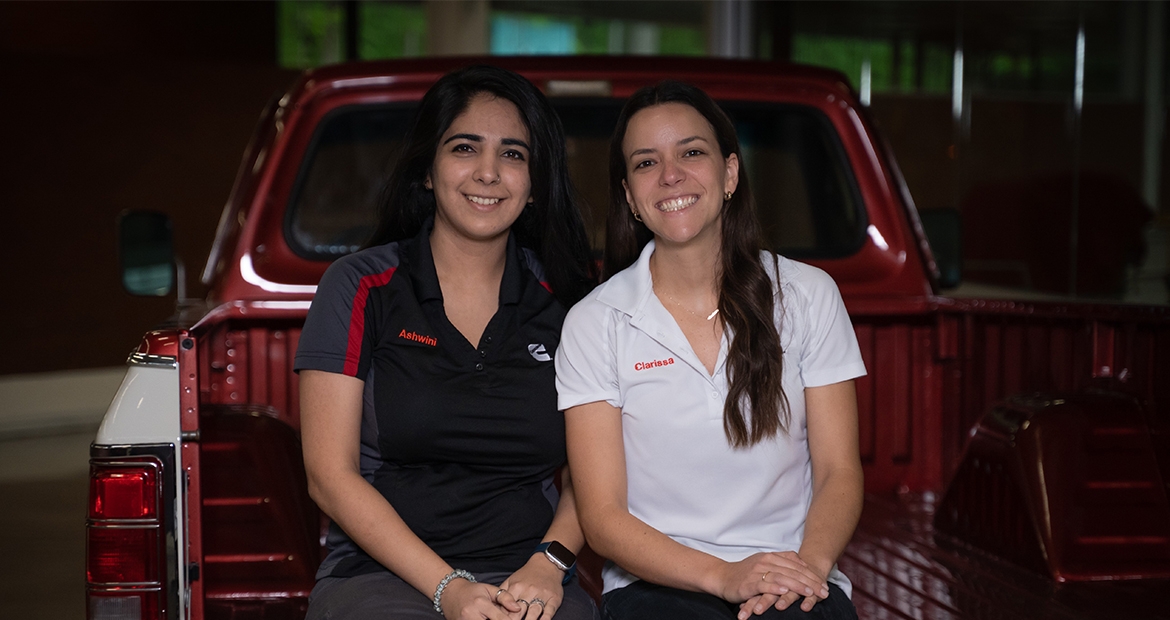
For over 30 years, the Columbus Mid-Range Engine Plant (CMEP) has built the heavy-duty diesel engine for pickup trucks and coated it in a rust-preventative. In 2021, this coating was eliminated, making manufacturing cleaner for the popular engine.
Despite how sophisticated a painted Cummins Inc. diesel engine may look, painting engines hasn’t always been for the dashing looks, cool style, and flash. As the most common source of material used to build an engine in the past was grey iron, it was necessary to use a rust-preventative coating on all of our engine models to avoid corrosion. Coating contributed to the extended lifespan of an engine, its components and overall durability.
While paint offers protection and, to some, great style, it comes with a heavy environmental cost – from massive water and chemical waste and increased energy use and natural gas output to emissions of volatile organic compounds (VOCs). Sustainability leaders and manufacturing and service engineers at the plant recognized the advancements in material diversity on the 6.7-liter engine and conducted an assessment on their coating process.
Through their assessment in 2020, engineers validated that the coating elimination would not expose the engines to excess corrosion, ensuring the same quality, capabilities, and durability without the environmental impacts.
In fact, less than 10 components were at risk of oxidation. With the advancements in technology, most engines today are built using a variety of materials from aluminum to cast iron, with composite components here and there. Over time, the 6.7-liter engine had evolved and with it, its components. As the majority of parts and surfaces on the engine would not be impacted due to the evolution of the engine over time, eliminating the coating process was clear. For the components that were prone to oxidation, engineers found more sustainable ways, like powder coating prior to final assembly, to seal these parts from potential exposure. Only a few components now still receive a rust preventative coating.
Engineers developed a strategy that would eliminate VOCs from coating operations, reduce greenhouse gas emissions (GHGs), water use and waste production, and recycle all packaging plastics.
Here are the top ways removing the coating process has increased the sustainability in manufacturing of the 6.7-liter diesel engine.
Reduced water usage and hazardous waste
In one day, CMEP would use between 10,000 gallons and 14,000 gallons of water solely on the coating processing line. Water from the coating wash tank was mixed with three different chemicals that cleaned the engine thoroughly, protecting coating from peeling over time. Yearly, the plant used an average of 23,500 gallons of chemicals to ensure engines were sealed.
For OEMs, fleets, and customers looking to reduce their scope three emissions, achieve environmental goals, and adhere to strict sustainability regulations, it’s important to know products are manufactured to the same environmental standards. Paint elimination reduces CMEP’s VOCs, particulate matter, and absolute water consumption - allowing the plant to save roughly 5 million gallons of water per year.
Reduced NOx emissions
You can image that running an industrial wash tank, two ovens, and automated spray robots requires a significant amount of natural gas and energy usage. With daily use of these tools natural gas use was significant. While natural gas is one of the more environmentally friendly fossil fuels, as it burns cleaner, emitting 50 percent to 60 percent less CO2 than regular oil, it still emits small amounts of NOx.
As a result of eliminating the coating process, natural gas usage was reduced by 88 percent, saving nine million gallons of natural gas used monthly – that’s equivalent to powering an average home in the United States for 20 years. Reducing the use of natural gas on the paint line eliminates NOx emissions, contributing to both a cleaner plant and cleaner product, with key cost savings to both the customer and manufacturer.
Decrease in plastic usage; increase in material and equipment recycling
Not every component on the 6.7-liter engine received the clear coating. To protect these pieces from overspray, plant workers would use single-use plastic cups, rolls of tape, stickers, and other small plastic covers. With fewer components and sections of the engine to cover, the plant can eliminate most of their plastic, which can often take years to decompose. It’s estimated the plant has eliminated nearly 16,500 pounds of waste.
The coating line alone occupied nearly 20,000 square feet of space in the plant, which has allowed for endless possibilities for how to use the machinery and material. With room for new innovations, The Columbus Mid-Range Engine Plant can continue to improve the 6.7-liter engine for pickup customers.
Coating elimination at CMEP has been widely successful. During Indiana’s 25th Annual Pollution Prevention Conference, the plant received the 2022 Indiana Governor’s Award for Environmental Excellence.
Eliminating a coating or paint process is not always feasible for other manufacturing plants, but Columbus Mid-Range Engine Plant leaders hope other facilities will conduct assessments of their own to determine if elimination and increased sustainability is possible. Cummins’ Jamestown Engine Plant implemented water-based paint in 2013 to eliminate VOCs, while other Cummins plants, like the Rocky Mount Engine Plant are currently evaluating the conversion to water-based paint.
CMEP is manufacturing cleaner, meeting strict EPA and regulatory standards, and continuing to produce the same, durable, and legendary 6.7-liter engine for the pickup customers.
Just as the 6.7-liter turbo diesel engine has evolved over time, with new innovations and technological advancements, so too will manufacturing facilities continue to evolve for the needs of society and the planet’s wellbeing.
Related Tags