Jamestown Engine Plant’s Community Recycling Day fights against waste
By Cummins Inc., Global Power Technology Leader
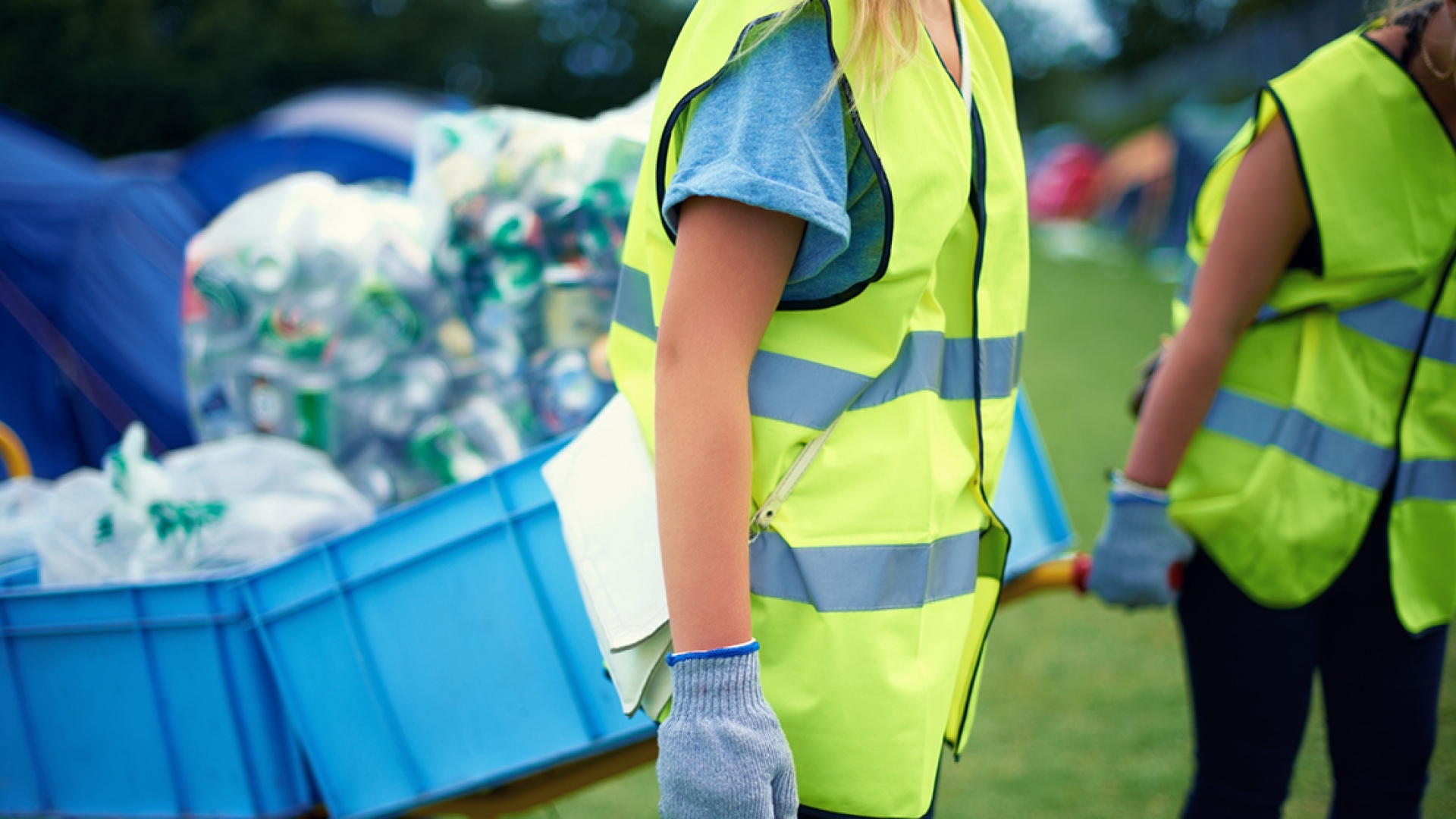
The Cummins Inc. Jamestown Engine Plant (JEP) isn’t only known for their engines that have powered fleets, businesses, and customers globally. It’s their dedication to environmental responsibility, particularly in their local community, that’s powering people’s motivation to recycle.
On June 18, 2022, locals gathered at Jamestown Engine Plant for its annual Community Recycling Day. Some started arriving as early as 5:30 a.m., eager to safely dispose of the unwanted items they’d been storing.
Over 950 cars showed up at the event toting automotive batteries, light bulbs, scrap metals, electronics, used tires and more. JEP’s Community Recycling Day is a sister event to the Cummins Columbus Engine Plant (CEP) Recycling Day that took place on September 15th. Between the two events, an estimated 140 tons of unwanted items were collected and diverted from landfills.
A look back at JEP Recycling Day 2022 Numbers
The JEP event alone brought in:
- 2,526 gallons of paint
- 4,275 pounds of automotive batteries
- 1,297 pounds of other types of batteries
- 734 pounds of light bulbs
- 3,160 pounds of scrap metal
- 66,844 pounds of electronics
- 950 gallons of used oil
- 65,820 pounds of used tires
The steady rise of electronic waste
The growing popularity of handheld devices like cellphones, tablets and smartwatches has contributed to a vast amount of electronic waste, also known as e-waste globally. E-waste can be broken into six categories: lamps, small IT and telecom equipment, monitors/screens, temperature exchange equipment, large equipment and small equipment.
E-waste is one of the fastest-growing waste streams in the world, with over 50 million tons generated per year. Of those 50 million tons, only 17% is reported as properly recycled.
Cummins plants have implemented systems to reduce this waste. Community recycling days, however, help limit the number of discarded items, including e-waste, that end up at landfills and incinerators, while energizing communities around a common environmental cause. The event shows people how their individual actions can make a greater impact.
Waste reduction a JEP and Cummins
At JEP, recycling days are just one aspect of an overall waste reduction culture. JEP is one of Cummins’ zero-landfill sites – sites that reuse or recycle all materials in a useful way.
The plant has a “waste streams” system which is a color-coordinated method for the recovery, recycling and disposal of waste. Different-colored containers that indicate where to discard items such as aluminum, gloves, wood pallets, bubble wrap and more are located all around the facility. Employees at JEP are known to pick up pieces of waste when they’re accidentally placed in the wrong location, demonstrating the commitment to the zero-waste cause.
As part of the Planet 2050 Strategy, Cummins aims to achieve a 25% reduction in waste by the year 2030, with longer-term aspirations for 2050. This includes a reduction in packaging waste, process waste and general trash. Partnerships with organizations like Indiana Department of Environmental Management (IDEM) have also contributed to education on pollution prevention within plants, when creating new products and resources on waste reduction.
Cummins plans to do this by recycling used oils, batteries, e-waste, cardboard, steel and other materials. They also plan to transition away from single-use packaging and toward reusable plastic packaging.
Jamestown Engine Plant’s Community Recycling Day 2023
This year, Jamestown Engine Plant will host their Community Recycling Day on Saturday, June 10.
Check out how other Cummins plants and communities are implementing sustainability practices every day. Learn more about PLANET 2050 and explore the specific and actionable environmental goals here.
Author Profiles
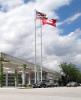
Cummins Inc., Global Power Technology Leader
Cummins Inc., a global power solutions leader, comprises five business segments – Components, Engine, Distribution, Power Systems, and Accelera by Cummins – supported by its global manufacturing and extensive service and support network, skilled workforce and vast technological expertise. Cummins is committed to its Destination Zero strategy – the company’s commitment to sustainability and helping its customers successfully navigate the energy transition with its broad portfolio of products. Cummins has approximately 69,900 employees and earned $3.9 billion on sales of $34.1 billion in 2024. See how Cummins is leading the world toward a future of smarter, cleaner power at www.cummins.com.