Agility and resilience define the Daventry story
Over the past five decades, more than 140,000 high horsepower engines have been transported out through the gates of the historic Cummins Power System plant at Daventry in the English Midlands, earning no less than 10 Queens Awards in the process, eight of them for export achievement.
By Cummins Europe, Global Power Technology Leader
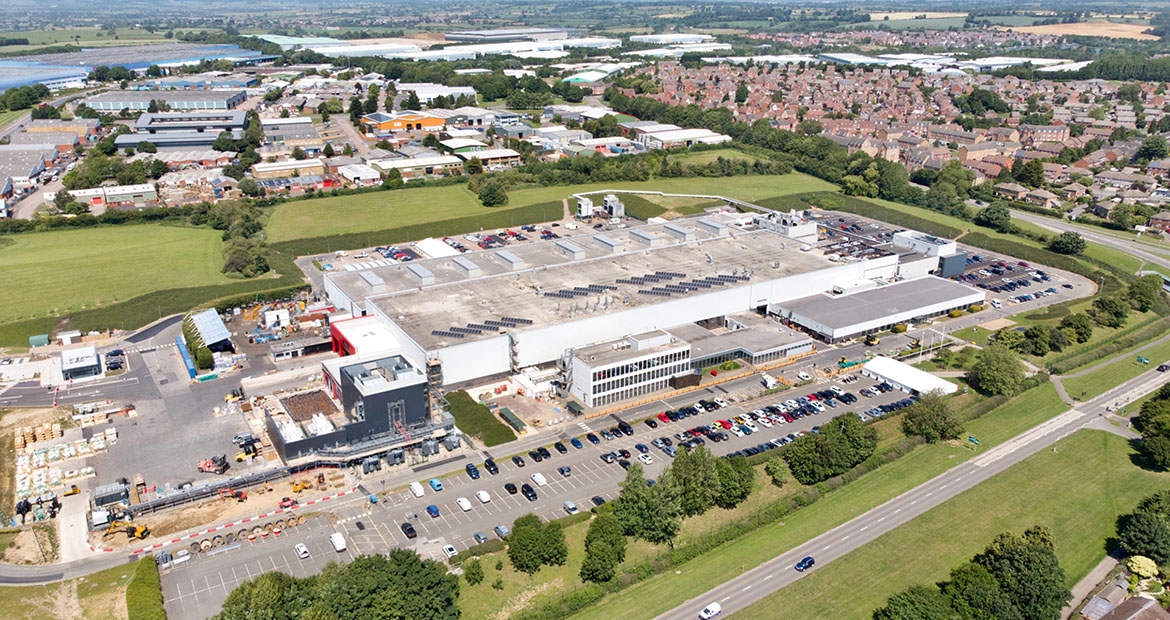
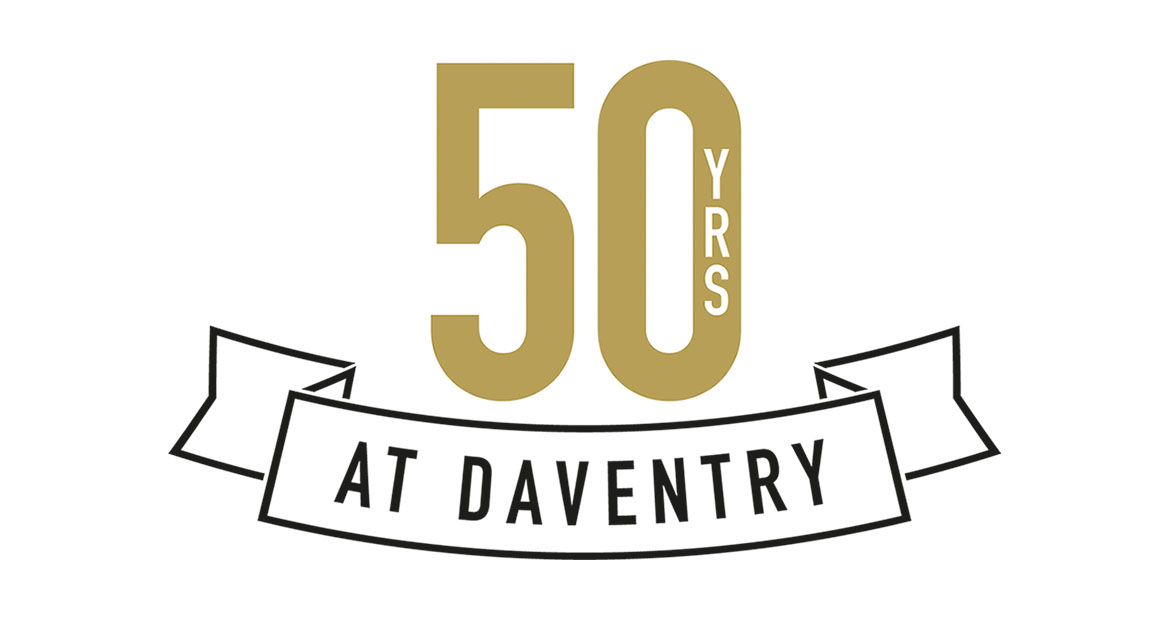
Engines bearing the ‘Made in Daventry’ stamp have come to be regarded as a symbol of efficiency, reliability and growth across a range of strategically important economic sectors in every continent of the world.
Those engines, ranging from 38 litres in displacement, can be found in mammoth mining machines, in oil and gas equipment, on trains, trucks, ferries and other working boats and on generators being used to provide critical back-up power for hospitals and datacentres.
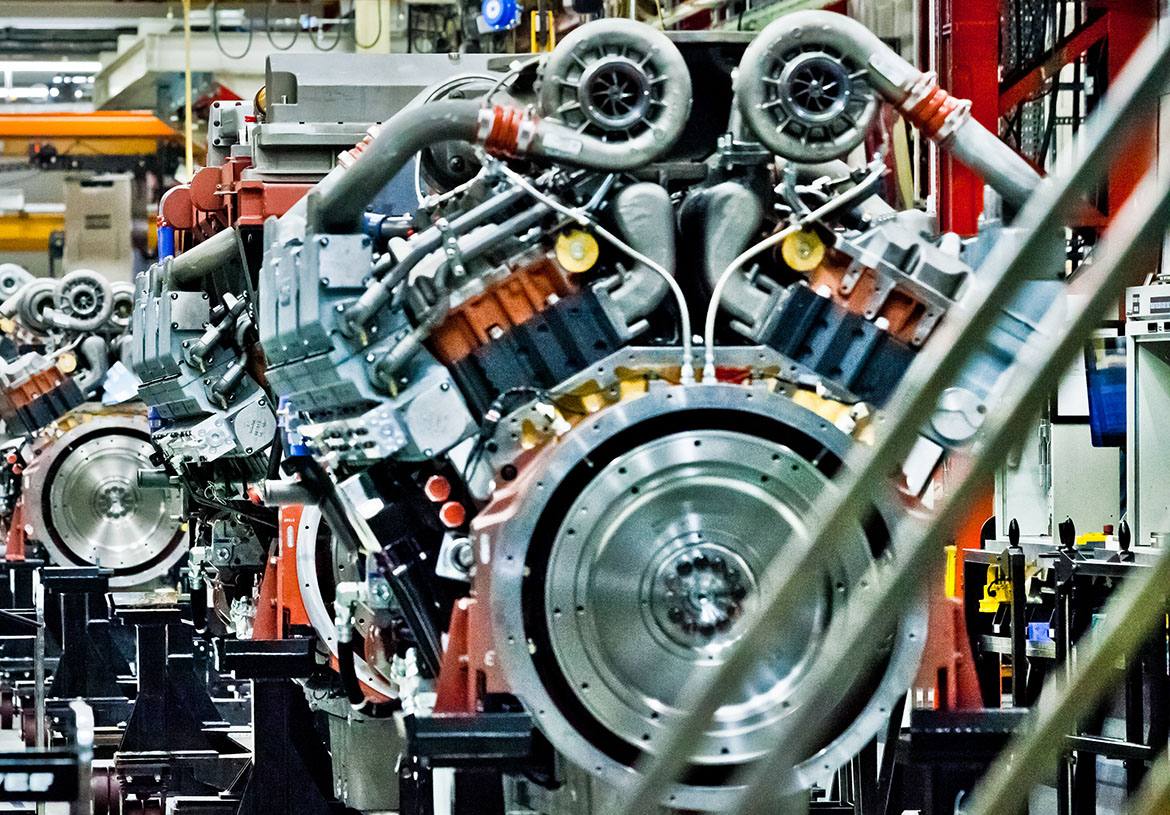
The success story that is Cummins Daventry owes much to creative thinking by the senior management and the spirit of resilience that flows through its massively experienced workforce: always ready to embrace change, seize opportunity and rise to whatever challenge presents itself, most recently global supply chains constraints in the wake of the Covid pandemic and the fallout from the war in Ukraine.
A culture of innovation and continuous improvement has been developed over the years and is firmly embedded in the professional DNA of everyone who works at Daventry.
“Yes, life here can be a bit of a roller-coaster ride as we anticipate and adjust to the economic cycles of the world,” says Dave Barker with a wry smile. Dave has been manager of the Daventry plant since 2017. His time at the helm comes to an end when he retires in mid-June 2023, returning to join the official celebrations marking 50 years of engine production at Royal Oak Way.
Launchpad for global expansion
Cummins bought the former Ingersoll-Rand automotive machine tools factory in 1972 to support its global ambitions and launch into the international mining sector. Opportunities within the Common Market, which the UK was about to join, were also a factor.
Newspaper cuttings from the time quoted Cummins officials saying Daventry – the first ‘American style’ factory outside the United States, distinguished by its enormous flat roof and absence of windows – would support around 450 jobs.
As it turned out, Daventry has maintained a workforce of 1,000 and more almost from the start of production in 1973.
Daventry had been earmarked as an ‘overspill’ town from the nearby cities of Birmingham and Coventry with their rich manufacturing heritage, so Cummins had little problem finding the right engineering skills. Some Ingersoll-Rand workers also stayed on.
In the past decade or so, Daventry has become a magnet for huge distribution centres. Close to the M1 and M40 motorways, and since 1997 home to an international rail freight terminal, it has welcomed the likes of Amazon, DHL and Eddie Stobart. Ford has its Parts Distribution Centre across the road from Cummins.
The first engine off the line at Daventry was a 12-cylinder K38 for the mining and construction equipment giant Komatsu, which remains a premium partner and customer of Cummins. And talking of longevity, a version of that K38 is still built at Daventry today.
The next product Iine was the K50, developed in test cell number one under the watchful eye of an experienced technician. “That K50 has proved itself one of the most capable industrial diesel engines in the world,” said Dave Barker. “It is absolutely the benchmark.”
On taking over as plant manager in 2017, Dave had a set of priority tasks that included extensive remodelling of the road entrance and the installation of new electrical infrastructure, including five new sub-stations, to future-proof the building.
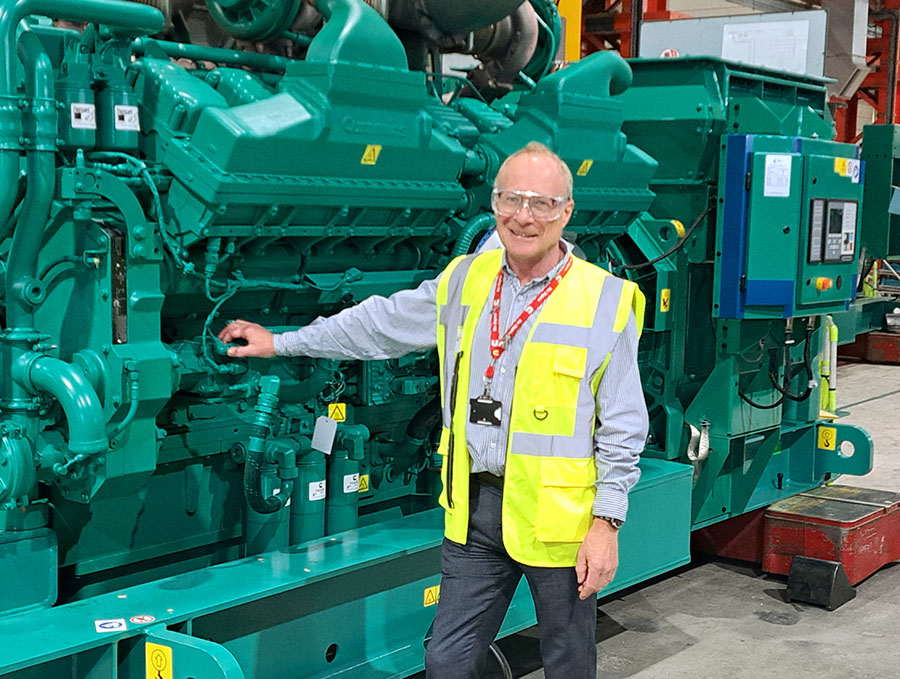
“Safety has to be a priority in our business, and the old single-lane access to the plant was always a concern. Every morning it would be carnage, with lorries backed up into the road and cars trying to get out. Improving the site access didn’t increase our production but Cummins’ support for safety enabled funding to be released to improve this area.”
As you arrive at the plant today, you notice to your left a field full of metal frames ready to support a vast number of photovoltaic solar panels – enough to deliver the two megawatts required to power the entire plant.
Dave Barker said the motivation in installing the solar panels was threefold: “First, we want to be consistent with our Planet 2050 strategy of reducing our environmental impact; second, this is an extremely power-hungry plant, and with the cost of energy so high, we can anticipate significant cost savings; third, we want to aim for energy security and independence from the grid.”
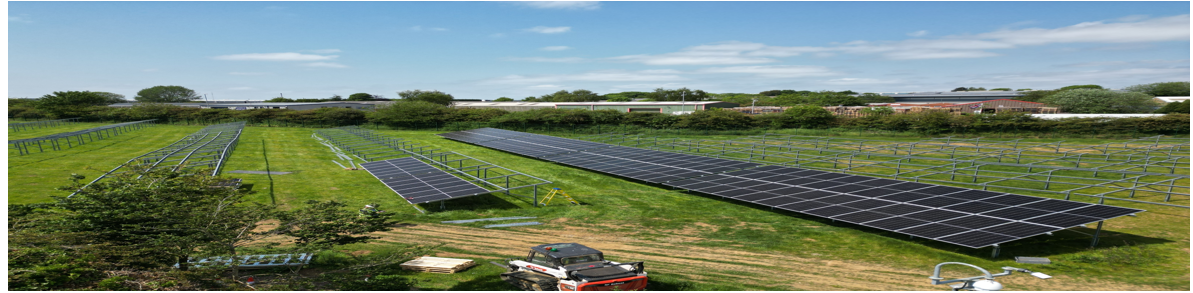
The next project in the pipeline is the installation of a gas-powered Combined Heat and Power (CHP) generator of the kind that Cummins supplies to commercial customers. “The CHP generator will fill in the gaps when we don’t have sufficient solar power, and it will be a great demonstrator for the business. It will make use of all that energy from our test cells that is just wasted.”
“We are not averse to changing the layout of the plant to accommodate new work or improve the flow of existing work – that’s how we accommodated the generator sets business in 2017 – and we’re always looking to create some empty space in readiness for something new. I know exactly where we could fit a battery or electrolyser assembly line if we needed it.”
Management at Daventry has always had to think lean. When the downturn came following the financial crisis in 2008, the team renegotiated key contracts and invested in second-hand machine tools which they could refurbish relatively quickly in-house, saving many millions of dollars and putting the plant in the best position to capitalise on the rebound.
“After that exercise, we found we could get back to our previous capacity of 24 engines a day but working only one shift instead of the five we were working beforehand. We were getting visitors coming to see us from all over the world wanting to know how we’d seemingly achieved the impossible.
“The lesson of that was to be bold and invest in a downturn so you can reap the benefits of the upturn.”
‘Change is what we do’
Cummins Daventry is supplying around 400 customers and processing something like 250 changes on its products each and every month.
“Basically, we are forever tweaking: engineering changes, power ratings, emission regulations, you name it,” said Dave. “The engine we build today will look very different when we come to build it in three years’ time.
“Change and adapting to change is ingrained in our culture, and the more complexity we face, the better it is for us as a business because nowhere else can do what we do here. We are a change machine.”
A tour of the Daventry factory floor confirms the astonishing flexibility of the production process, with engines moving down the line to be worked on in multiple timed stages.
“We are producing a whole number of different engine models, with different performance curves so that every single engine is different,” said Dave. “And we can build in any order, with zero changeover and set-up time because our processes are interchangeable.”
The agile production process extends to the paintshop where it’s not uncommon to see a run of engines emerge in Komatsu yellow, followed by Onan green and then Cummins red, all without any manual intervention as the paint guns are flushed and cleaned automatically.
The generator sets, which could take days to build previously, now take just six hours. “We assemble generator sets powered by Cummins engines produced here at Daventry, or from one of our other global factories. These are mated to Cummins alternators and controlled by bespoke Control panels.”
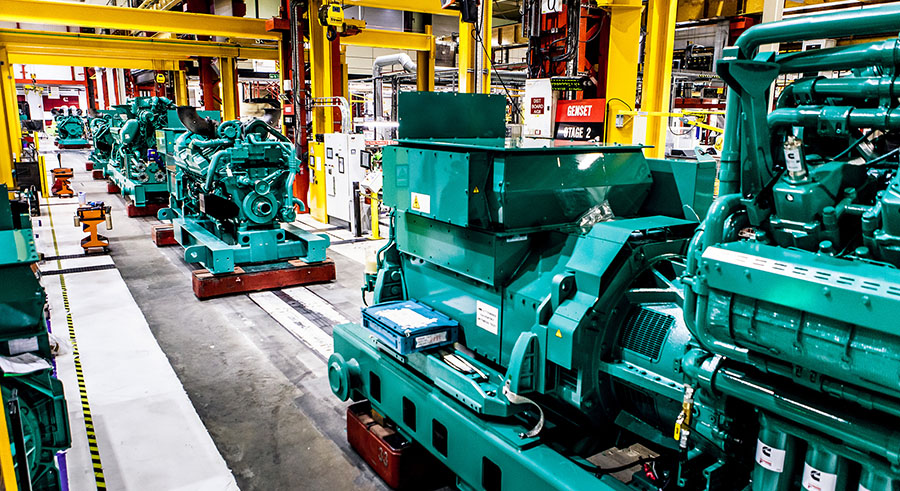
Many of these generator sets are installed as back-up emergency power sources for datacentres that house ‘cloud’ computing systems. “Our products serve some of the largest computing companies in the world – names that will familiar to all of us,” said Dave.
Daventry ships its products all over the world but its biggest markets are North America and China. No other plant within the Cummins empire matches Daventry for the scope of its output, and it is a world centre of excellence for mining engines.
Crucial to the success of Daventry has been the opening in June 2021 of the enormous Cummins UK Logistics Centre just a mile or so away.
Everything that’s needed on the production line is delivered just in time, every 30 minutes. “It has been a fantastic success,” says Dave, who was one of the Cummins executives lobbying hard for it to be located close to the factory.
Components and materials are sourced from around the world: cylinder heads from Mexico; machine castings from India; aluminium from Finland. But the biggest source is from the UK and Europe.
“We have some great long-term relationships,” said Dave. “These suppliers include family businesses where we began with the grandfather and now, we’re onto the third generation.”
One of Daventry Plant’s proudest achievements is its strong ties with the local community around Daventry. In recent times, Cummins has awarded grants to local projects and the team from the Daventry plant have pitched in on a pumping system for a local reservoir, building benches and planters, clearing towpaths and repurposing pallets to make fold-up stalls for local schools. During Covid, the Cummins canteen provided free meals to disadvantaged children.
Dave Barker says leaving Cummins will be a massive wrench (no engineering pun intended) but the outdoors-loving Yorkshireman is looking forward to spending more time sailing, cycling and hiking.
“I’m immensely proud of this place. I’ve been here more than half my working life, arriving as an engineer from the aviation sector in 1991 not knowing the front end of a diesel engine from the back. Quite simply, I’ve had the best job in Cummins.
“It’s been an amazing journey, with an incredible team behind me, and I think we’ve demonstrated why Daventry is a jewel in the crown. If whoever takes over from me keeps that spirit of innovation and the can-do attitude, this place will keep moving mountains and doing Cummins proud.”
Author Profiles
Cummins Europe, Global Power Technology Leader
Cummins Inc. opened its first site in Europe in 1956. Today it has 12 manufacturing sites and more than 10,800 employees in the region. Cummins works hard to provide advanced technologies supported by a long-established service network across Europe. Cummins is committed to investing in Europe through Research and Technology, ensuring Cummins’ technical experts are developing innovations of the future.