Three ways Cummins connected solutions help reduce fleet costs and environmental impact
By Cummins Inc., Global Power Technology Leader
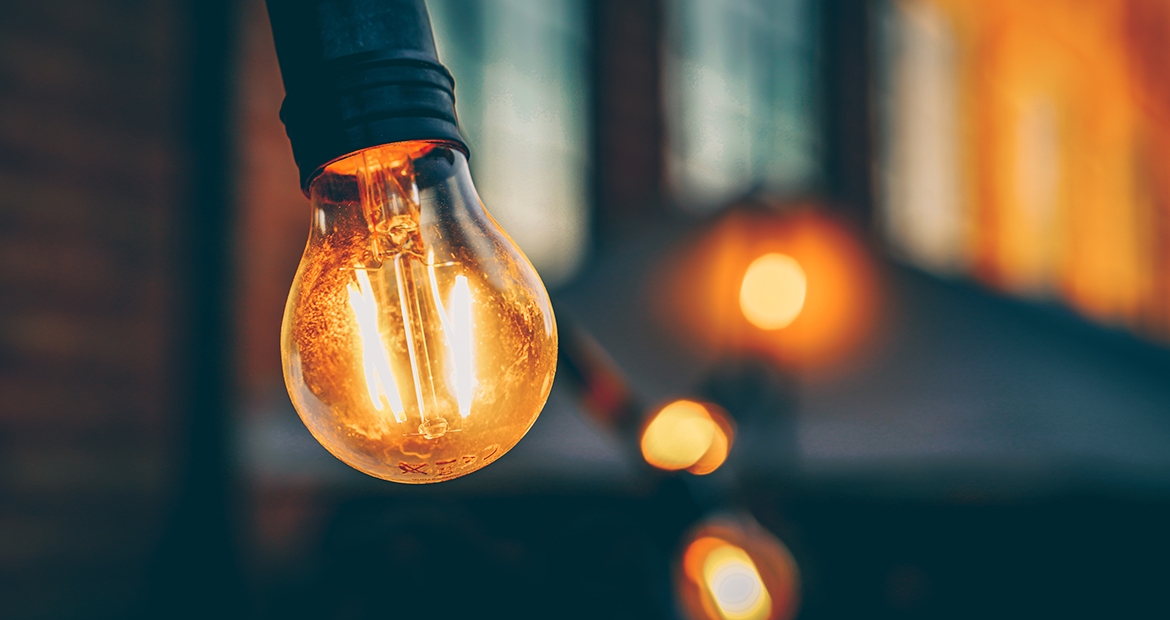
Rising costs related to fuel, trailers, parts, insurance, wages and more all keep truck fleet managers on the lookout for ways to meet market demands more efficiently. In response to these escalating expenses, Cummins has proactively implemented measures to address the rising costs.
Digital technologies can play an important role in the journey to reduce costs. But did you know they can also make a positive impact on the environment? Consistent with Cummins’ Destination Zero strategy to go further, faster to reduce the greenhouse gas and air quality impacts of the company’s products, here are three examples:
1. Remote monitoring
Using digital technology, Cummins customers can monitor engines in real-time using the company’s remote diagnostics software that provides engine and component health alerts.
When a potential engine problem is detected, fleet managers are notified with recommended actions, severity, and timeframe. This feature has proven to be essential for customers in China to comply with the government’s requirement for onboard emissions reporting hardware in heavy duty commercial vehicles as part of its programs to fight climate change.
Detailed information about emerging maintenance or repair issues is communicated up to 90 days before anticipated failures, potentially avoiding costly unplanned service stops or breakdowns while in-mission. Detecting anticipated failures early means they can be addressed during planned service events.
Reducing fuel consumption related to tows and detecting potential failures of key components early supports Cummins’ goal of positively impacting the environment. For instance, nitrous oxide (NOx) and particulate matter (PM) sensors that impact exhaust can be monitored and maintained, directly contributing to the goal of a sustainable future.
2. Over the air programming
Intelligent trim parameter adjustments can optimize engine performance and fuel efficiency.
Cummins is developing configurable engine trim parameters for speed governance, idle time, torque exchange, and more which can have an impact on the environment, safety, and profit margins. Instead of having to visit service centers to have trims adjusted manually, telematics-based software will enable fleet managers to adjust trims over the air to meet real-time conditions, such as rising fuel costs and climate change.
Over-the-air parameter updates and calibration updates not only help to optimize engine performance so vehicles run at their best, but they can also benefit the environment by improving fuel efficiency and eliminating the fuel, emissions, and cost of downtime involved in taking trucks to a service station for manual calibration by a technician.
3. Service technology
Improved diagnostics technologies enable faster, more accurate service events, better planned maintenance, and faster parts procurement.
Using Cummins digital service tool, Guidanz, customers can take advantage of a Fast Track Repair feature whereby traditional diagnostic assessment steps can be skipped. Vehicles can move directly into necessary repair work accelerating service speed and reducing downtime. Operators get back to work sooner while service providers improve shop efficiency.
While vehicles are being serviced, the same predictive technologies can be used to analyze engine performance data and identify additional preemptive service needs. Without this capability, service needs may not be detected until a fault alert was triggered or a component failed, requiring the vehicle to make another trip to a service shop. Fewer trips to service centers mean reduced fuel consumption, emissions, and downtime, which results in a reduction in costs and environmental impact.
The above three-prong digital technology suite from Cummins can support customers over the life of their vehicle while setting the stage for continued innovation through data and analytics. Learn more about turning insights into uptime with PrevenTech, optimizing engine performance with OptiTech, and accelerating service events and job-order workflows with Guidanz.
Author Profiles
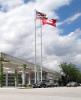
Cummins Inc., Global Power Technology Leader
Cummins Inc., a global power solutions leader, comprises five business segments – Components, Engine, Distribution, Power Systems, and Accelera by Cummins – supported by its global manufacturing and extensive service and support network, skilled workforce and vast technological expertise. Cummins is committed to its Destination Zero strategy – the company’s commitment to sustainability and helping its customers successfully navigate the energy transition with its broad portfolio of products. Cummins has approximately 69,900 employees and earned $3.9 billion on sales of $34.1 billion in 2024. See how Cummins is leading the world toward a future of smarter, cleaner power at www.cummins.com.