Enabling miners to achieve the lowest cost of production sustainably
By Cummins Inc., Global Power Technology Leader
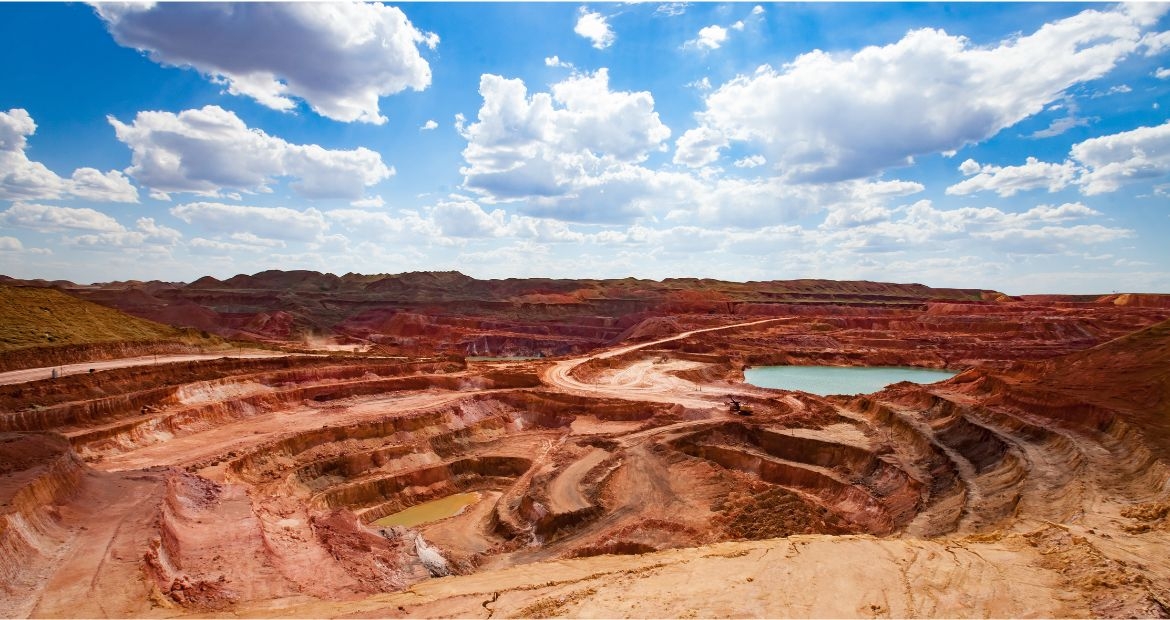
For the past decade, mining operations have been focused on lowering cost of production, merging together Total Cost of Ownership (TCO) and amount of production achieved.
Today, a third factor is impacting the equation: sustainability. Lowering costs and boosting production only go so far, considering the increasing importance of protecting the environment and the communities where mines operate.
While the factors contributing to the ability to sustainably achieve the lowest Cost of Production (COP) are extensive and complicated, it’s important to understand the many areas where a miner’s choice in engine manufacturer can have significant impact.
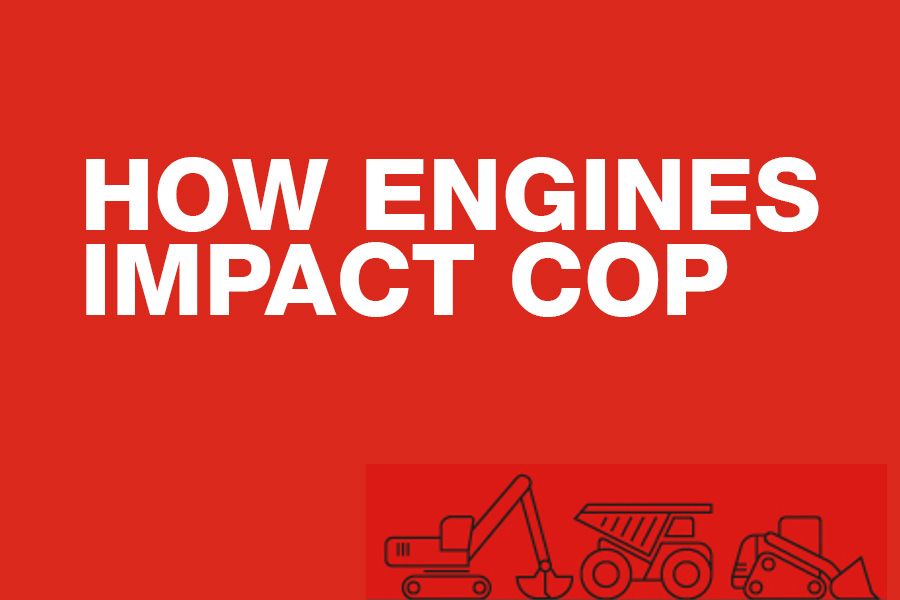
How does your choice of mining engine affect the cost of production?
To start, production cost is impacted by many contributing cost and production factors.
Cost factors
Mining engines affect fuel and repair and maintenance cost factors.
Fuel:
Fuel maps and calibrations, the calculated rates at which fuel is consumed when engines are running, are application-specific, and Cummins Inc. works with end-users to achieve the best fuel economy by matching the right engine technology to the proper horsepower and torque for specific elevation and duty cycles. As one example, in 2022 one Cummins mining customer was able to achieve a 7% fuel economy improvement, saving 17 million liters per year in fuel and $16 million a year through custom calibration and optimized speed settings across the fleet. This initiative also resulted in a reduction of 45,900 metric tons of carbon dioxide equivalent.
For autonomous trucks, Cummins can optimize calibrations even further, allowing for smoother, more efficient engine operation than when driver to driver variability is involved.
Cummins Tier 4 engines offer up to 3-5% better fuel efficiency than Tier 2 engines, with no compromise to engine power and reliability. This significantly reduces fuel costs.
Sustainability Bonus: Less fuel consumption leads to fewer emissions. In the project mentioned above, the customer slashed 45,900 metric tons of carbon dioxide equivalent by improving fuel economy. Plus, all Cummins high-horsepower engines are approved for use with unblended renewable diesel (or HVO), as well as varying blends of biodiesel.
Repair & Maintenance:
Extended service intervals can greatly reduce unnecessary downtime and wasted consumables. Cummins will work with end-users to conduct a TCO analysis for new engine purchases, calculating whole life schedules based on equipment usage and determining recommended service intervals for various components.
Another way that Cummins extends service intervals is through condition-based maintenance, made possible through advanced digital solutions, PrevenTech® for Mining and Fleetguard FIT. This allows miners to reduce consumables, such as coolant and filters. Costs can add up quickly for routine oil and filter changes, so why dispose of anything prematurely?
Preventing progressive damage and potential failures through PrevenTech is another way to protect finances—and production. Through advanced telematics, proprietary algorithms and customizable alerts, PrevenTech alerts operators when something is wrong—or trends are pointing to a future failure—allowing miners to act proactively. For example, when a fuel injector fails, it can lead to progressive damage if not fixed promptly.
Considering that quality mining engines can be rebuilt up to 3-4x before the core reaches its end of life, it’s important to consider the engine manufacturer’s rebuild process. Cummins has 13 Master Rebuild Centers (MRCs), including our newest state-of-the-art facility in Poland, and all engines rebuilt by Cummins receive all current product updates and a new zero-hour warranty.
For operators looking to manage costs even more precisely, Cummins offers a Cost per Hour (CpH) contract, providing a fixed or level cost for maintaining Cummins engines over the anticipated running hours.
Sustainability Bonus: Extending service intervals leads to a reduction in consumables, ultimately sending less waste to landfills. Cummins also recycles and rebuilds parts when possible, further reducing environmental impacts.
Production factors
While managing costs is critical, it means nothing without maximized production. Mining engines also affect production, specifically where payload, cycle time, availability and utilization converge.
Payload:
Cummins has an engine for every mining need, including our 4,400 hp QSK95, recognized for the highest power on the market for the highest load capacity.
Cycle Time X Availability X Utilization:
Cummins’ engines are built with uptime as the priority. Unlike some alternative options, Cummins mining engines are designed as industrial engines first, including industrial grade components made to run at 50+% load factor.
This commitment to industrial-grade design enables our engines to perform in extreme conditions. Our customers operate in high altitudes from Chile to the Tibet region of China, as well as extreme temperatures from the Canadian arctic to the Australian outback.
Just as Cummins’ extensive network and remote monitoring solutions slash R & M costs, they also boost availability. Specifically, Cummins has an extensive inventory of service engines available to keep miners running during maintenance cycles, and our 13 high-horsepower Master Rebuild Centers, 600+ distributor locations and 3,700+ high-horsepower technicians are strategically located around the globe to serve mining customers quickly and effectively.
Bottom line, Cummins has built its 100+-year legacy on providing the world’s most reliable engines. In fact, an Arizona mine site experienced 43% improvement in mean time to failure and 69% improvement in mean time to repair after switching from non-Cummins engines to Cummins engines.
Sustainability Bonus: As miners crush production, they can be confident that Cummins Tier 4 engines —utilizing advanced selective catalytic reduction (SCR) technology—emits 90% less harmful emissions today compared to engines produced before the year 2000.
Sustainability
As mining companies strategize to meet both near- and long-term sustainability targets, Scope 1, 2 and 3 emissions all come into play.
As Cummins continues to innovate, our power solutions will continue to positive impact our customers’ Scope 1 emissions.
Beyond our industrial mobility power solutions, Cummins is also powering mine site infrastructure optimization, enabling mine sites to reduce Scope 2 emissions through flexible, autonomous energy management solutions.
And as a power technology company serving the world in many ways, we take our own sustainability practices very seriously, impacting our customers’ Scope 3 emissions. Since 2014, we have partnered with customers on more than 700 fuel economy projects, saving them $11 billion in fuel costs and avoiding 30.5 million metric tons of CO2.
View Cummins 2022-2023 Sustainability Progress Report to learn more about the significant progress Cummins is making in environment, social and governance & economic arenas, including our PLANET 2050 environmental sustainability strategy.
Author Profiles
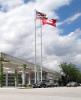
Cummins Inc., Global Power Technology Leader
Cummins Inc., a global power solutions leader, comprises five business segments – Components, Engine, Distribution, Power Systems, and Accelera by Cummins – supported by its global manufacturing and extensive service and support network, skilled workforce and vast technological expertise. Cummins is committed to its Destination Zero strategy – the company’s commitment to sustainability and helping its customers successfully navigate the energy transition with its broad portfolio of products. Cummins has approximately 69,900 employees and earned $3.9 billion on sales of $34.1 billion in 2024. See how Cummins is leading the world toward a future of smarter, cleaner power at www.cummins.com.
Related Topics
Related Tags