What is remanufacturing?
By Cummins Inc., Global Power Technology Leader
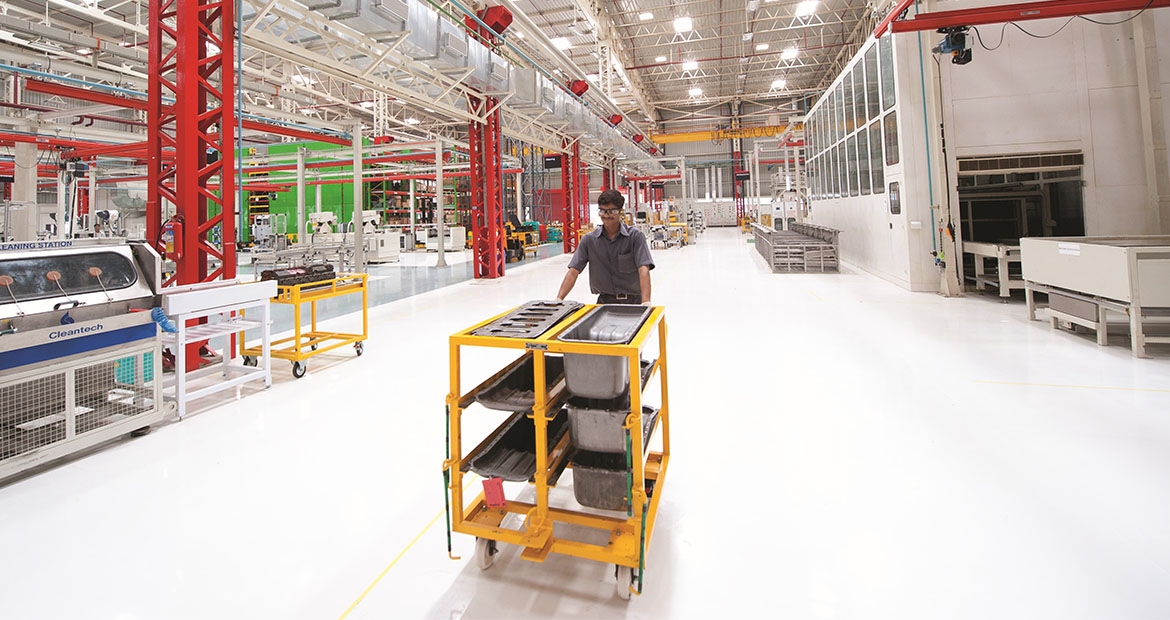
In today's market, remanufacturing of engine parts is gaining traction as an eco-friendly and economically viable option. Remanufacturing extends the lifecycle of an engine, ensuring both environmental sustainability and cost-effectiveness. This article looks at how Cummins Inc. uses remanufacturing for its ReCon® remanufactured parts and engines.
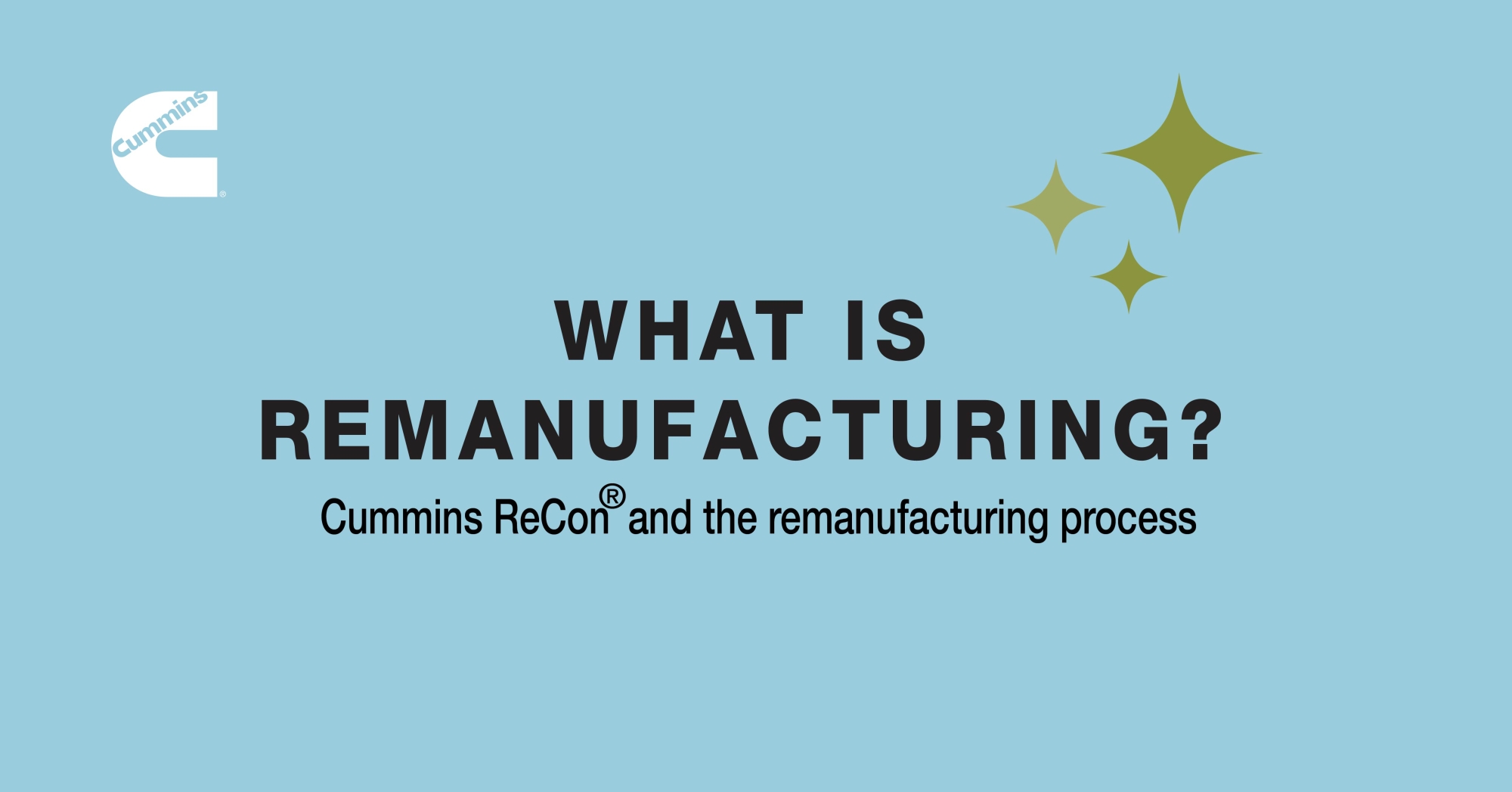
What is remanufacturing?
ReCon parts are those that have originated from a Cummins engine and have gone through disassembly, inspection, cleaning, calibration and testing to ensure they meet the same performance requirements as new Cummins parts. Cummins ReCon parts are then offered for individual sale or used to build Cummins ReCon engines.
Engines reaching their end-of-life are disassembled entirely, ensuring every single component, is prepped for the process. Parts are cleaned utilizing the latest technologies. For instance, laser cleaning is applied for rust removal, while environmentally friendly methods like enzyme cleaning effectively tackle grease, oil and other impurities. Post-cleaning, a comprehensive inspection is conducted on each part, employing methods like ultrasonic inspection and ensuring that every ReCon product aligns with the factory's initial requirements. If an upgrade has been made to the original design, this update will also be added as the engine or part is remanufactured.
Cummins has been perfecting its remanufacturing process for decades. New tools and processes have been added, including additive manufacturing (also called 3D printing), collaborative robots (also known as “cobots,” which are robots intended to physically interact with humans in a shared workspace), laser cleaning and more.
Genuine value begins with the Cummins remanufacturing process. Unlike an engine shop that repairs or rebuilds engines by replacing parts that are broken or malfunctioning, Cummins remanufacturing follows a rigorous process that ensures that every part is examined, cleaned and tested to meet performance requirements. If an upgrade has been made to the original design, this update will also be added as the engine or part is remanufactured.
Which engine parts can be remanufactured?
Almost 85% of an engine can be remanufactured. Parts eligible for remanufacturing encompass a broad range from turbochargers, fuel pumps and injectors to actuators and cylinder heads. Certain parts with a predetermined lifespan, or parts for which fatigue detection is challenging, are not included in the remanufacturing process and are scrapped and replaced with a new or ReCon part.
During this process, each Cummins ReCon engine is completely disassembled, inspected, cleaned, tested, painted and brought back to "like new" condition in a Cummins remanufacturing facility, all in compliance with ISO 9001 standards. These newly built engines come with the latest ReCon or new parts warranty and have zero hours/miles.
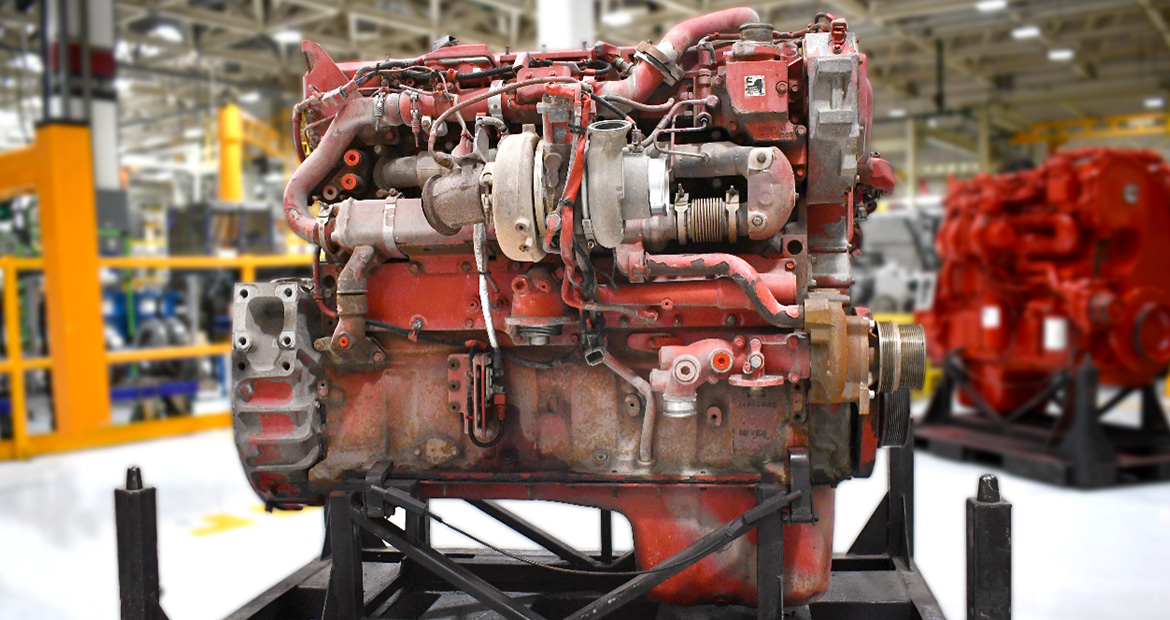
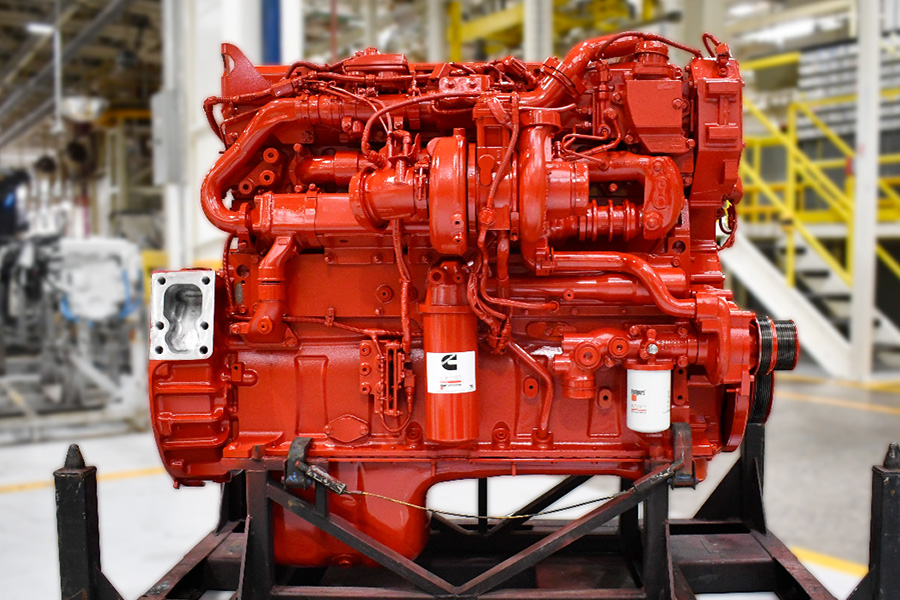
Remanufactured parts and their advantages
- Remanufacturing is crucial for furthering the circular economy, promoting the reuse of materials and addressing environmental challenges like climate change. Cummins is dedicated to the circular economy, focusing on reusing, recycling and remanufacturing materials. This approach reduces waste, conserves resource and supports environmental sustainability. Cummins ReCon engines and parts further highlight this commitment.
- Remanufactured engines retain the reliability and efficiency of new engines but are often available at a lower cost. This cost-effectiveness is due to the reduced need for energy, materials and water in the remanufacturing process. Cummins ReCon parts and engines are affordable, include the newest engineering updates and are backed by a Cummins warranty.
- Selecting Cummins ReCon engines and parts can also speed up delivery times and be more efficient than the extended procedures of disassembling, diagnosing and repairing existing engines.
- Remanufacturing not only ensures product reliability but also promotes sustainability. Opting for remanufactured parts reduces waste and the need for new raw materials. Choosing a Cummins ReCon part or engine supports a more sustainable future.
- Remanufactured products also have a positive impact on industry dynamics and local communities. By reusing existing materials and products, the need for raw materials extraction and waste disposal is decreased, cutting down on carbon-intensive processes associated with these industries. Remanufacturing often creates local jobs, as skilled technicians are essential to ensure that parts are diligently restored to their original requirements.
What are the challenges with remanufacturing?
One of the main challenges for remanufacturing is the alignment with suppliers. Designing a part or engine that can be remanufactured requires close collaboration with suppliers, not just from a manufacturing perspective but also to ensure mutual sustainability goals. Suppliers must understand and agree to the principles of remanufacturing to create a cycle that both supports the environment and meets customer requirements.
Historically, companies have been hesitant to embrace remanufactured products, often due to misconceptions about quality and longevity. As the global supply base is projected to contract in the future, remanufactured products are a great option to overcome potential supply chain challenges.
The Cummins ReCon business stands at the forefront of this shift to remanufacturing. ReCon engines and parts not only exemplify the fusion of reliability and affordability but also encapsulate the broader vision of a more sustainable future. While challenges remain, particularly in supplier alignment and broader industry acceptance, the benefits of remanufacturing are undeniable. Remanufacturing will play an increasingly pivotal role in shaping an eco-friendly, economically viable, and resilient manufacturing marketplace. Contact your local Cummins distributor or authorized Cummins dealer location to learn more about our ReCon parts and engines and partner with us to achieve your sustainability goals.
Author Profiles
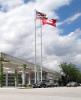
Cummins Inc., Global Power Technology Leader
Cummins Inc., a global power solutions leader, comprises five business segments – Components, Engine, Distribution, Power Systems, and Accelera by Cummins – supported by its global manufacturing and extensive service and support network, skilled workforce and vast technological expertise. Cummins is committed to its Destination Zero strategy – the company’s commitment to sustainability and helping its customers successfully navigate the energy transition with its broad portfolio of products. Cummins has approximately 69,900 employees and earned $3.9 billion on sales of $34.1 billion in 2024. See how Cummins is leading the world toward a future of smarter, cleaner power at www.cummins.com.
Related Topics
Related Tags