Components of fuel systems in diesel, hydrogen ICE, natural gas and hydrogen fuel cell technologies
By Cummins Components Business Unit
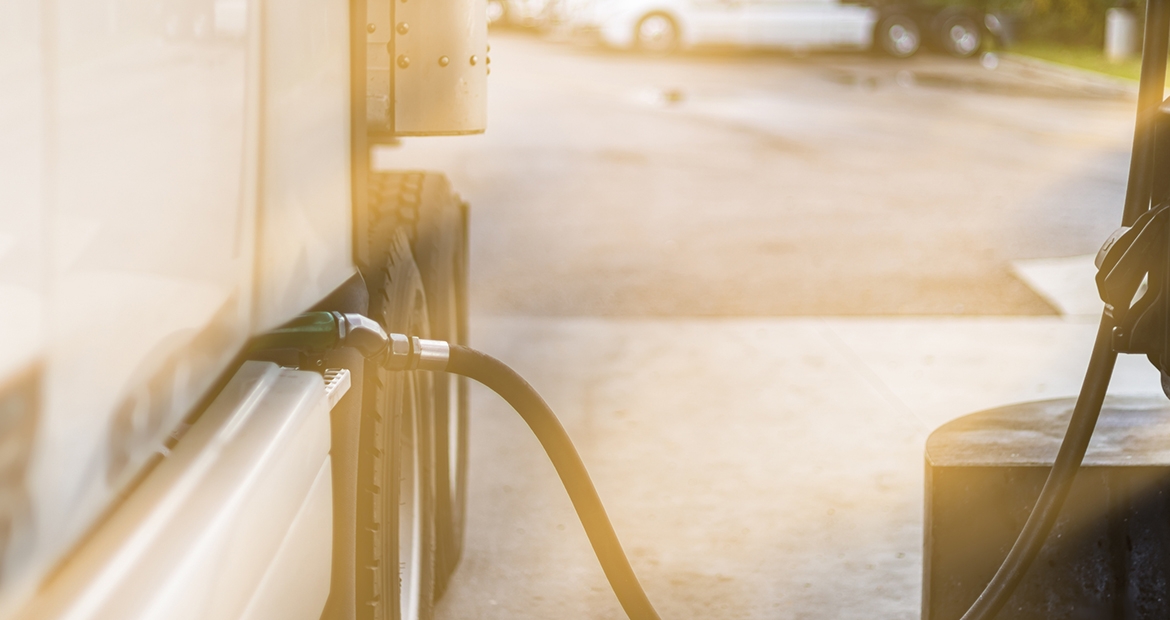
The fuel system is a critical part of any engine, playing a pivotal role in powering vehicles efficiently and effectively. As fuel technologies evolve, a better understanding of the fuel system enables Original Equipment Manufacturers (OEMs) to meet their emission goals, optimize vehicle performance, ensure safety and comply with regulations.
The fuel system is part of the powertrain and includes all components necessary for regulating fuel delivery to the engine. This includes: the fuel tank, pump, filter, injectors and sensors. On the other hand, the fuel delivery system and its components are a subset of the fuel system; it specifically focuses on components directly involved in delivering fuel from the tank to the engine.
This article looks at the key components of fuel systems across different engine types, including diesel ICE, hydrogen ICE, natural gas and hydrogen fuel cells.
Click on the 'blue' spots on this interactive and find out more about the components of a fuel system.
Components of the fuel system in diesel engines
Diesel engines are well-suited for use in heavy-duty applications due to their torque and durability. The fuel system in a diesel engine comprises several key components, including:
Filtration: Advanced filtration technology used in Cummins diesel engines removes contaminants such as debris and water from the fuel before it gets to the fuel injectors. Given the extreme fuel pressures in diesel engines and fine nozzle holes on injectors, fuel quality can significantly affect engine performance and longevity.
Fuel Pumps: Diesel engines commonly use multiple fuel pumps: The low-pressure pump pulls fuel from the tank and delivers it to the high-pressure pump, which then pressurizes and regulates fuel flow to the injectors. In commercial trucks, these pumps are designed to ensure optimal fuel delivery in the most demanding driving conditions. The high-pressure pump is particularly critical in achieving the required injection pressure for efficient combustion.
Fuel Rail: The fuel rail is a manifold responsible for distributing fuel to the injectors. It ensures even and efficient delivery of fuel across all engine cylinders. Furthermore, the fuel rail enables the fuel system to deliver the optimal fuel pressure across a range of engine operating conditions, which is crucial for consistent engine performance and emissions reductions.
Pressure Sensor: Located in the fuel rail, these components are essential for maintaining the appropriate fuel pressure, which is critical for maintaining engine integrity and performance. The pressure sensor measures the fuel pressure and communicates with the engine control unit (ECU) to fire the injectors long enough to deliver the correct amount of fuel. The fuel pressure sensor can also be used to detect issues with the fuel system, such as leaks.
Mechanical Dump Valve: Many common rail diesel fuel systems have a mechanical dump valve (MDV) located in the fuel rail. The MDV is a spring-loaded valve that is forced open when fuel pressure exceeds a pre-set limit. It acts as a safety device to release pressure if it exceeds safe limits and protects the fuel system components from damage. Some diesel engines even possess electronic dump valves which can be used for improved fuel pressure control.
Fuel Injectors: Fuel injectors deliver precise amounts of fuel into the combustion chamber with spray patterns that ensure optimal mixing of fuel and air. This precision is vital for efficient combustion, maximizing fuel efficiency and reducing emissions. In commercial vehicles, the performance of fuel injectors directly impacts engine efficiency, power output and emission levels.
Plumbing: Both metallic and non-metallic fuel lines seal and transfer fuel throughout the system. Appropriately sized fuel plumbing is critical for meeting engine application demands and preventing leaks. In commercial vehicles, robust plumbing is essential to withstand the rigors of long-distance travel and varying operating conditions.
Components of the fuel system in natural gas and hydrogen ICE engines
Natural gas and hydrogen ICE engines will play a critical role in the shift to reducing emissions. One benefit of these engines is that they fit the same envelope as a diesel engine, requiring less change to the vehicle. Gaseous fuel systems have fewer components than an equivalent diesel fuel system but are still critical to delivering optimal performance and meeting stricter emissions.
Filtration: Filtration in natural gas and hydrogen ICE vehicles cleans the fuel and removes compressor oils. This is critical for the performance and longevity of the engine. For example, in natural gas-powered trucks, compressor oils adversely affect the fuel system.
On-engine Shut Off Valve and Pressure Regulator: Since natural gas and hydrogen engines are expected to deliver diesel-like performance, on-engine pressure regulators may be used to regulate the fuel pressure delivered to the injectors. This ensures accurate fueling at any engine operating condition. Shut-off valves may also be integrated into the regulator. These valves prevent fuel flow to the engine when the vehicle is shut off.
Injectors: Gaseous fuel injectors ensure the correct amount of fuel enters the combustion chamber. For instance, in hydrogen ICE vehicles, the injector is designed to handle the unique properties of hydrogen while still meeting engine performance demands.
Components of the fuel system in hydrogen fuel cell vehicles
Hydrogen fuel cells represent a cutting-edge approach to sustainable transportation. Their fuel systems include:
Fuel Injector / Proportion Control Valve: Fuel cells may opt for either an injector or proportional control valve to regulate the flow of hydrogen to the fuel cell stack. It ensures the precise amount of hydrogen is delivered to the stack to react with oxygen and generate electricity, which provides power to the vehicle.
Ejectors: These help to recirculate unused hydrogen back to the fuel cell stack. This is critical for increasing efficiency and ensuring durability of the fuel cell.
Hydrogen Re-circulation Pump: Working in conjunction with the ejector, this pump recirculates unused hydrogen from the fuel cell stack back into the system.
Purge Valve and Water Drain Valve: These components are responsible for removing excess water and non-hydrogen contents to maximize the efficiency of the system.
Pressure Relief Valve: This is a safety device that protects the fuel cell stack from excessive fuel pressure. It is a critical component in all hydrogen fuel cell vehicles for safe operations under all conditions.
Shut Off Valve: This valve allows fuel flow into the injector and acts as an on/off valve that closes when the engine is shut off.
The fuel system is an integral part of any engine; each component ensures the efficient and safe operation of the engine. Cummins is at the forefront of developing low-emissions engine technology. As technology advances and the demand for cleaner fuel options increases, understanding these components and how they optimize engine performance is vital.
Author Profiles
Related Tags