Transforming operations: Zach's impact at Cummins
By Cummins Inc., Global Power Technology Leader
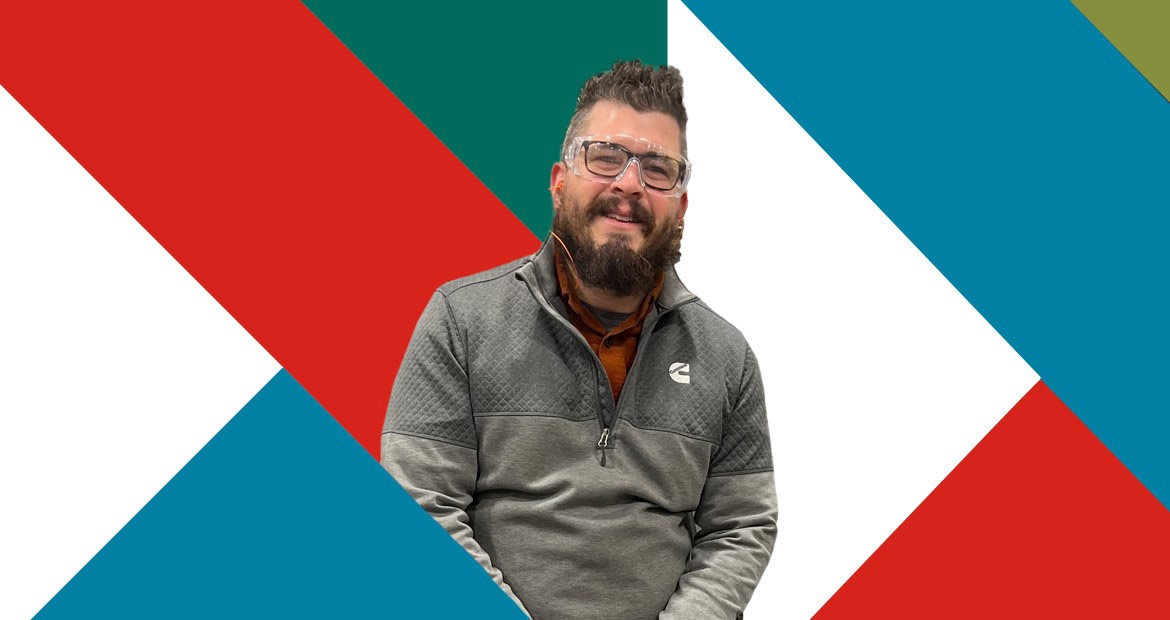
Zach B. made a pivotal decision to step away from the traditional academic path and enter the manufacturing workforce directly after his undergraduate studies, setting the stage for a dynamic career journey. Graduating from Bryant University in Rhode Island with a major in business administration and a minor in psychology, Zach's final class project, which involved developing a business operations plan for a local business, became a turning point in his life. He chose a plastic injection molding and mold-making facility that specialized in products for the medical industry.
His work and professional demeanor throughout the project caught the attention of the business owners, leading to a job offer immediately after graduation. Initially hesitant about stepping directly into the workforce, Zach embraced the opportunity, starting as an engineering apprentice. This position allowed him to explore various facets of the business, from office management to hands-on floor operations, igniting a passion for sales and business development.
Over the next four years, Zach honed his skills in sales and business development, eventually transitioning into a program management role overseeing the molding and tooling divisions. His ability to effectively manage projects and lead teams did not go unnoticed, and three years later, he found himself leading operations and engineering. By 2020, Zach's drive and proven leadership skills led to his promotion to General Manager of the company's Connecticut location. This role was a springboard to his former role , managing North American operations at three plastic injection molding factories located in Connecticut, Chicago, and Tijuana, Mexico. His early leap of faith into manufacturing had clearly paid off.
When asked how he ascended the corporate ladder so swiftly, Zach points to his academic background, particularly his studies in psychology. “I almost think it should be a prerequisite that people going into management have a basic understanding of how the human brain and human emotions work so you can communicate with people effectively,” he says, adding that technical knowledge and aptitude are critical. According to Zach, insight into how people think, react and are motivated is universally applicable across managerial roles and can significantly enhance communication and team dynamics.
Zach joined Cummins Inc. in October of 2023. Currently, as the Operations Manager of Components and Service Parts for Cummins Valvetrain Technologies, Zach's daily routine involves an early start, reviewing overnight shift reports and preparing for a series of meetings focused on safety, quality, delivery and cost metrics. His leadership style is deeply influenced by participative management, where he leads by example. One of his first initiatives upon taking his current role was to re-implement the 5S system, a workplace organization method that had not been actively practiced at the plant since the 1990s. Under his guidance, both salaried and hourly employees spend time each day organizing and cleaning their workspaces, starting with the engineering offices and extending to the production areas.
“I don’t ask my employees — direct labor or salary — to do anything I wouldn’t do myself,” Zach says. “We clean together. I’m with the team on my hands and knees, scrubbing a dirty bench covered in oil. And I do it alongside my engineer or production supervisor to demonstrate to all labor employees that nothing in the business is beneath any of us. We do whatever it takes to create a clean and safe working environment for each other.”
Zach's commitment to improvement is not limited to cleanliness and organization. He has introduced and actively monitors Overall Equipment Effectiveness (OEE), a key performance indicator in manufacturing, to gauge and enhance productivity. Initially, his department’s OEE was at 55%, but through consistent efforts eliminating downtime, it has been making steady progress towards the goal of 85%. This metric serves not only as a measure of current productivity but as a benchmark for continuous improvement.
Moreover, Zach is dedicated to cultivating a robust safety culture within the plant. By focusing on proactive measures rather than reactive responses, he aims to minimize disruptions and ensure a safer work environment for all. His approach to safety, like his management style, is inclusive and collaborative, seeking buy-in from every team member to foster a shared commitment to better practices.
“You have to build that safety culture and get buy-in from everyone in the building,” he says. “It's not a matter of being perfect; it's just about being safer than we were yesterday.” Every day, his teams work to improve something, make something cleaner or safer, or fix a process so that people leave workspaces in the same or better condition than when they arrived.
The culmination of Zach's efforts was evident during a recent high-level visit from Cummins leadership team. The visit showcased the daily standards maintained by Zach and his team, impressing the senior leaders with the sustained improvements achieved in a short time.
“Cummins has a good culture,” Zach says. “We’re focused on our employees, we’re focused on safety and we’re focused on doing the right thing no matter what. It reinforces why we have such a good product and why I like them so much I own them myself. When our plant begins to focus on the daily little wins — like this leadership visit — we begin to build our own micro-culture of excellence, and that’s what we’re focusing on.”
Zach's personal connection to Cummins runs deep, evidenced by his enthusiasm for the brand, which extends beyond professional admiration to personal passion. Owning three pickups equipped with Cummins diesel engines, he finds great satisfaction in knowing he contributes directly to the products that fuel his hobby. This personal investment in the brand complements his professional role, merging his career with his personal interests in a uniquely fulfilling way.
Author Profiles
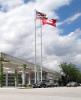
Cummins Inc., Global Power Technology Leader
Cummins Inc., a global power solutions leader, comprises five business segments – Components, Engine, Distribution, Power Systems, and Accelera by Cummins – supported by its global manufacturing and extensive service and support network, skilled workforce and vast technological expertise. Cummins is committed to its Destination Zero strategy – the company’s commitment to sustainability and helping its customers successfully navigate the energy transition with its broad portfolio of products. Cummins has approximately 69,900 employees and earned $3.9 billion on sales of $34.1 billion in 2024. See how Cummins is leading the world toward a future of smarter, cleaner power at www.cummins.com.
Related Topics
Related Tags