Engine modularity: Flexible valvetrain solutions for global markets
By Cummins Components Business Unit
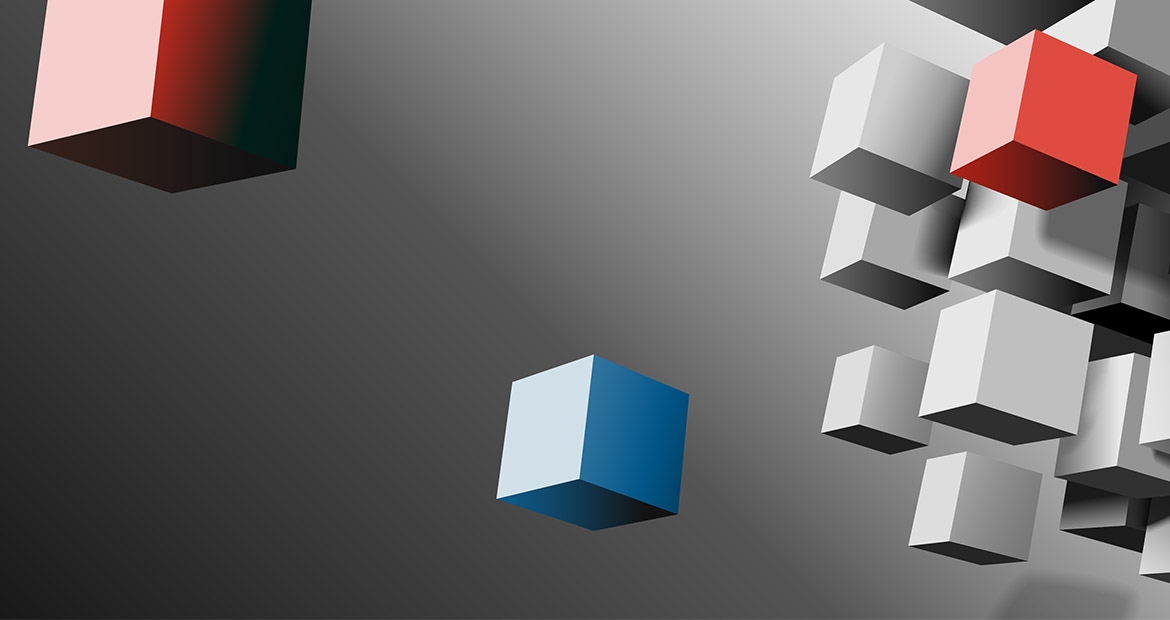
Engine and vehicle OEMs are faced with the difficult task of streamlining their engine platform and adjusting it for global markets – each with its own emissions regulations and power requirements. To allow for more flexibility, our engineers have been working on “future-proofing” engines with in-engine modular valvetrain technologies to allow engine platforms to be adjusted to varying global markets, emission regulations and alternative fuel types such as natural gas and hydrogen.
“What we are doing is creating a modular valvetrain. A valvetrain that can do it all - I’ll call it a Swiss Army Knife valvetrain. A valvetrain that can do engine braking. It can do Cylinder Deactivation. It can do Late Intake Valve Closing to improve fuel economy. It can do decompression for start-stop cycles. Having a valvetrain that is modular and can meet all the OEM’s requirements as the emissions get tighter and tighter over the next 10 years," said Gabe Roberts, Director - Product Development, Cummins Valvetrain Technologies.
Engine Braking – Scaling Up or Down
As the commercial vehicle industry continues to evolve, so does the Jacobs Engine Brake®. For over 60 years, we have been developing, designing and producing engine brakes for most of the world’s vehicle OEMs, and the technology has evolved to meet specific requirements for each market such as the U.S., Europe, China and India. The compression release engine brake is the standard in the heavy-duty industry and is applied not only to commercial vehicles but in agricultural and other off-road applications as well.
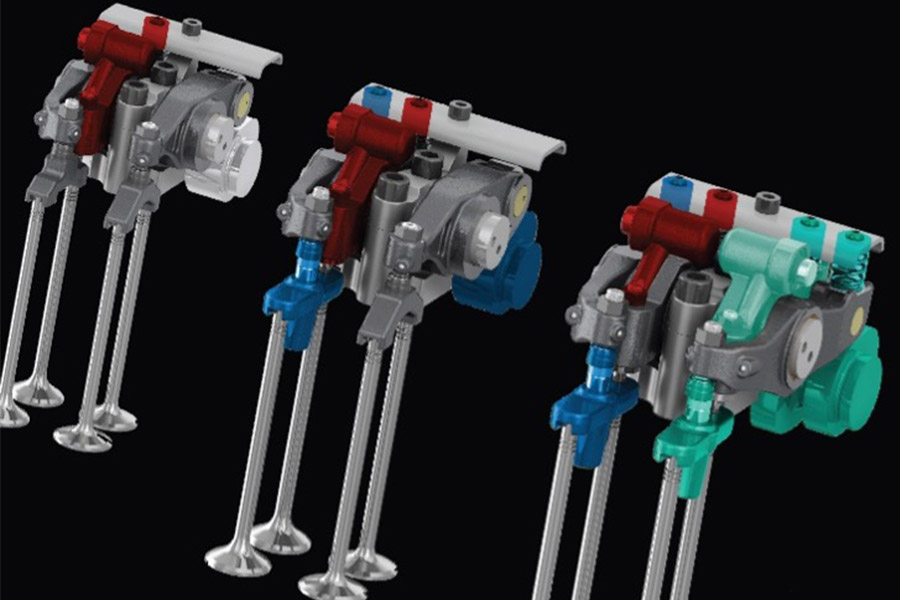
With the ever-increasing globalization of our customers, where the engine platforms are used across the world, and only customized on emission technology and general performance per market area, OEMs are looking for flexibility in the technologies provided.
Up- and down-scaling is important with minimum impact on the basic elements of the engine. Cummins Valvetrain Technologies’ answer to that trend is to supply “future-proofed” valvetrain designs right from the start of the engine design. This means that within the same hardware space claim several technology steps can be realized: standard compression release braking for markets that need just that, or upscale towards High Power Density® (HPD®) in markets or applications that require higher performance or are looking at the optimization of the complete drivetrain by eliminating the need for driveline retarders. We accommodate this by ensuring these steps are easy to integrate, even in the future, so development and validation efforts are minimized, and different options can be incorporated at engine build for different needs.
Emissions – Meeting Ever-tightening Regulations
To help OEMs meet global emission regulations, our engineers have worked to solve this issue inside the engine with a modular technology approach. In fact, many of our emission-related technologies make use of our well-proven engine brake technology but are applied in a new way to offer in-valvetrain emission technologies. One example is cylinder deactivation (CDA), which makes use of the same collapsing valve bridge hardware that is also used for HPD. Using the same logic, CDA offers deactivation of several cylinders when engine loads are low, effectively enabling a six-cylinder engine to run as a 3-cylinder (or less) engine, providing important fuel economy (CO2) benefits and NOx reduction. CDA is a technology that is expected to play an important role in NOx reduction for the next U.S. emission regulations and is part of a “Keep It Hot” aftertreatment strategy, along with meeting future Green House Gas rules (GHG).
While NOx reduction is the more immediate focus of North American regulations, in Europe CO2 reduction is what matters most for upcoming emission regulations. The differences between these two markets have evolved from the duty-cycle standards that have been developed separately in both markets, creating a challenge for OEMs – how to accommodate a technology that meets both regulations within the same global engine platform. Our answer to that is a modular system. Late Intake Valve Closing (LIVC), or any form of Variable Valve Actuation (VVA) can be integrated into that same valvetrain as well. VVA can provide both “Get It Hot” and ‘Keep it Hot’ strategies and allows for simplification of the aftertreatment systems downstream of the engine. In short: both CDA and VVA are options to improve both NOx and CO2 for different drive cycles, and both are designed by our engineers at the start of the engine’s development.
Yet another technology that can be combined within the valvetrain is Active Decompression Technology® (ADT®), which is focused on start-stop applications. This is a technology that sees interest not only from heavy-duty applications (also non-road) but also medium-duty and light-duty applications where it enables further levels of driveline electrification. ADT offers a faster and smoother transition from eMotor to ICE modes in hybrid powertrains.
Demand for Fuel Economy
OEMs are progressively taking an overall vehicle system approach when looking for further fuel consumption reductions. This is important as all components work together; if one element of the system is overlooked, it may work against other improvements that depend on that element. The engine is just part of that system, as is the after-treatment system, the transmission, the axles, etc. When looking for every drop of fuel to be saved, one must look at the overall system interaction. We take a system approach, and when we design our modular technologies, we make sure we understand how it works together with the rest, and what can be done downstream of our technology to make it even better.
Most of the technologies discussed above have a focus on the emission levels coming out of the exhaust pipe, and they do offer fuel economy improvements to certain levels as well. CDA is the best example of that, but also ADT can provide fuel consumption reductions when applied correctly. But it doesn’t stop there. From a system perspective, minimizing friction within the engine is one thing that is talked about a lot, and a way to achieve this is by specifying lower-viscosity engine oils. This seems like an easy thing to do, but as engine oil is the main medium for valvetrain actuation, suppliers like us must make sure that the functionality, performance, and durability of these technologies are not jeopardized. With our in-house solenoid developments and advanced simulation and testing capabilities, we make sure to follow suit. As all our technology is concentrated on in-valvetrain solutions, further optimization and weight reduction of the overall vehicle is possible too (another element of the “system”), yet again allowing for further fuel consumption reduction.
Valvetrains that are consistent in their performance over the lifespan of the vehicle are important as well: any deterioration due to part wear that negatively impacts either emission levels or fuel consumption must be minimized. An example of technology that allows for that is lashless technology. Already mainstream in passenger cars, lashless valvetrains eliminate the need to set lash on the valves by introducing Hydraulic Lash Adjusters (HLAs). The advantage of such a system is a very consistent engine operation, during its full life. Previously incompatible with an engine brake, we have designed Fulcrum Bridge and Spring Bridge technology that now opens the door to HLA introduction in heavy and medium-duty engines for any application.
Author Profiles
Related Tags