What type of turbocharger do natural gas engines need?
Key takeaways:
- Natural gas turbochargers are specifically designed for natural gas engines.
- Natural gas turbochargers are optimized for high-altitude performance, crucial for markets like China.
- Natural gas turbochargers offer lower total operational costs and better compliance with emissions regulations.
By Cummins Components Business Unit
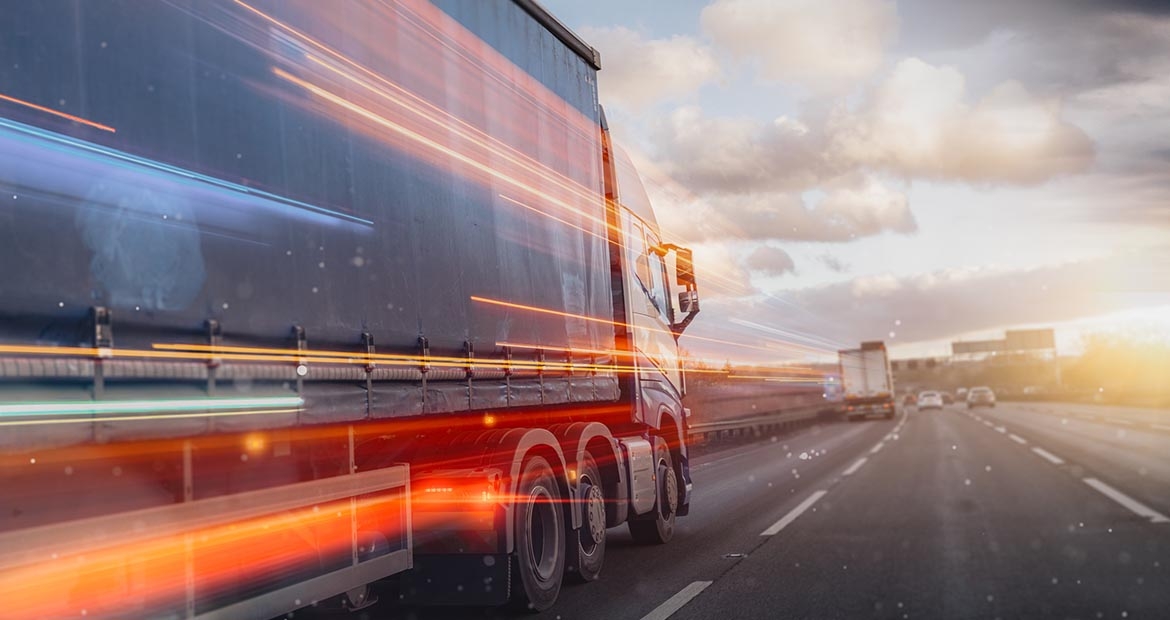
At Cummins Inc., we’re constantly looking for ways to advance sustainable transportation solutions. As the industry shifts to lower-emission fuels to reduce pollution, natural gas engines are one critical pathway to cleaner mobility. Cummins is therefore working to innovate component-level technologies supporting natural gas engines.
Understanding how natural gas engines work and the components enabling their optimal operation can help provide a better view into the future of engine technologies. One such critical component is the turbocharger. Cummins Turbo Technologies has spent decades designing and manufacturing Holset® turbos for natural gas engines.
In this article, we’ll explain a bit more about natural gas turbos, their performance and some of the benefits and challenges these components have.
Do natural gas engines need different turbos?
Yes, natural gas engines require different turbochargers than diesel engines due to their higher operating temperatures and distinct air-to-fuel ratios. Unlike diesel engines, which operate with a lean burn and a higher air-to-fuel ratio, natural gas engines require a stoichiometric burn. This means the mixture of oxygen and fuel is balanced precisely (1:1 air-to-fuel ratio) for efficient combustion, ensuring no unburnt fuel or excess oxygen remains. Consequently, natural gas engines require smaller turbochargers since less air is needed for stoichiometric combustion compared to the leaner burn in diesel engines. For example, a diesel engine might need an HE500 turbo, but a natural gas engine could use an HE300 or HE400 due to its lower air requirements.
Natural gas engines also influence the size and core requirements of the turbocharger. In diesel engines, turbocharger efficiency is a key focus, whereas, in natural gas engines, the primary considerations are achieving the required mass flow rate and meeting exhaust gas recirculation (EGR) demands.
Cummins addresses these specific needs by reducing back pressure at the turbine stage and enhancing the bypass capability of turbochargers with our twin-entry dual wastegate turbocharger technology.
Additionally, the more intense temperatures and pressures within natural gas engines necessitate changes to the turbocharger’s components and materials. Natural gas turbos, for instance, are built with high-temperature materials at the turbine stage to resist thermal fatigue and feature water-cooled bearing housings to protect the rotor system under extreme conditions.
Things to consider with turbochargers for natural gas engines
Turbochargers for natural gas can deliver power and performance for your applications. But two main considerations remain:
- High-Altitude Performance: In markets like China, which is a leader in natural gas applications, engines often operate at higher altitudes. These conditions can create low-cycle fatigue due to changes in turbine inlet temperatures, adding more thermal load to the turbo.
- Material Selection: High temperatures of the natural gas systems demand advanced materials, which can drive up costs. So, customers need to strike the right balance between performance and cost savings.
Cummins leverages its expertise in diesel and natural gas engines to deliver specifically designed turbocharger components that enhance the performance and durability of natural gas systems. While initial costs for natural gas turbochargers may be higher, the total cost of operation is often lower due to cheaper fuel and increased reliability. Additionally, natural gas engines equipped with the right turbochargers are better positioned to meet stringent emissions regulations.
At Cummins, we're not just responding to challenges; we're leading the way with proactive solutions. Natural gas will play a key role in reducing emissions across the transportation industry. As global regulations tighten, we're focused on developing engines that offer environmental and cost benefits.
Author Profiles
Related Topics
Related Tags