What turbochargers do hydrogen internal combustion engines (H2ICE) need?
By Cummins Inc., Global Power Technology Leader
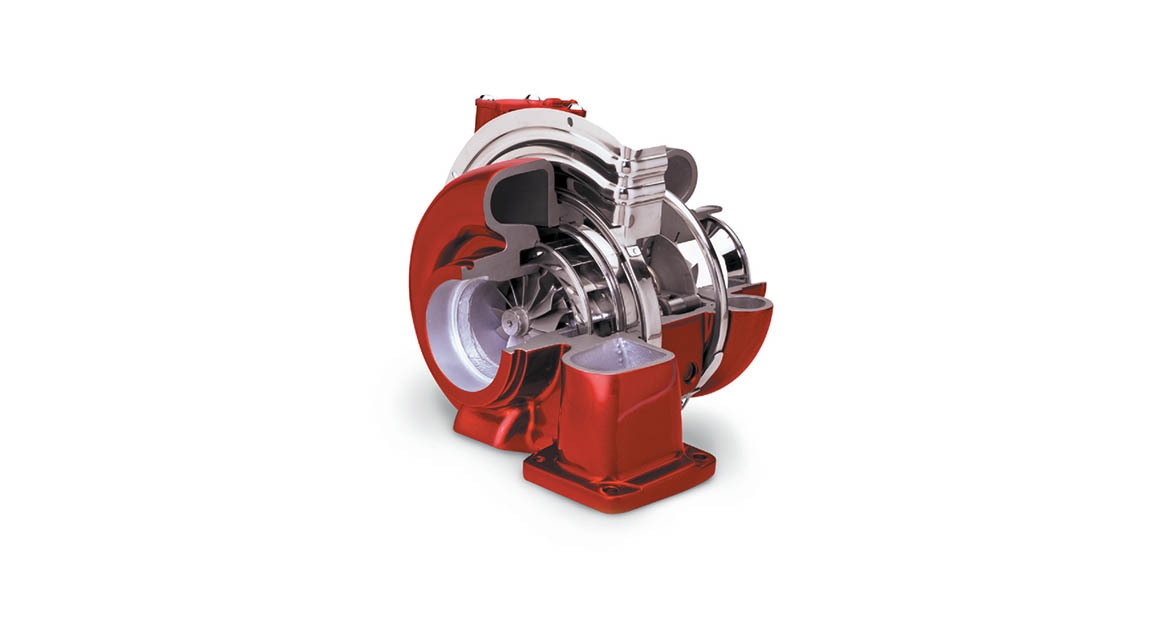
Key Points
- H2ICE familiarity: Hydrogen engines operate like traditional ICEs, easing the transition to cleaner technologies.
- Turbocharger configurations: Advanced turbo systems boost hydrogen engine performance and emissions control.
- Challenges: Higher airflow demands require innovative turbocharging solutions.
- Cummins leadership: Cummins is driving hydrogen engine and turbo innovation for sustainable mobility.
Four-stroke Hydrogen combustion engines (H2ICE) operate on the same principles as traditional engines but are more powerful and efficient. They share components like engine blocks, cranks, and ignition systems with natural gas engines and seamlessly fit into existing designs. This article delves into the role of turbochargers in enhancing the performance and viability of hydrogen engines, showcasing their potential in the evolving energy landscape.
Considerations for turbocharger configuration in H2ICE
Turbochargers enhance the efficiency and power of hydrogen engines by boosting airflow into the combustion chamber, compensating for hydrogen's lower energy density. Cummins' Holset™ turbochargers, with expertise from diesel and natural gas applications, are advancing the technology for hydrogen engines.
Choosing the right turbocharger configuration for hydrogen ICE requires balancing performance and emissions needs. Here are some considerations:
- Turbochargers supply pressurized air to boost engine power by burning more fuel and oxygen. Hydrogen engines require precise air-fuel control for efficiency and performance, making certain turbocharger designs with improved control systems, like variable geometry or electronically controlled wastegates, better suited to reduce nitrogen oxide (NOx) emissions while burning hydrogen.
- Minimizing lag and enabling a lean burn is critical for reducing NOx emissions and improving engine performance. This drives the need for optimum low transient response which enhances vehicle drivability and helps enable the transition to low-carbon fuels.
- Using a large single turbocharger in hydrogen engines gives a lot of power at high speeds but loses power and responsiveness at low speeds. On the other hand, a smaller turbo works well at low speeds but can't provide adequate cylinder pressure at higher speeds, restricting peak power. Both single-turbo setups reduce overall engine performance because they struggle to manage the air-fuel mix needed for hydrogen engines.
- A two-stage turbo system, on the other hand, uses two turbos, arranged sequentially: a small high-pressure (HP) turbo for quick boost and torque at low speeds, and a larger low-pressure (LP) turbo for smooth power at higher speeds. This setup reduces the pressure on a single turbo and better matches the engine's fuel needs. It also uses a wastegate as a relief valve to control and regulate boost pressure from a turbocharger.
- A variable geometry turbocharger (VGT) has adjustable nozzles that change the airflow characteristics of a turbocharger based on engine conditions. This helps optimize boost pressure, improve efficiency, and reduce emissions by providing precise control at different speeds.
- An electric turbocharger (e-turbo) uses electricity to control airflow into the engine, offering quick boost response independent of engine speed. It also adds extra power to the rotor (in addition to the exhaust) to improve engine performance and response.
Each turbocharger type has its pros and cons—e-turbos can be complex, and two-stage systems may pose installation challenges. However, hydrogen combustion engines offer a promising, familiar, and practical path to decarbonizing fleets, potentially transitioning more quickly than BEVs or FCEVs.
Challenges for turbochargers in H2ICE
While hydrogen technology offers a path to lower emissions, it faces several challenges:
- Power density: Hydrogen requires significantly more airflow than fossil fuels, demanding larger and more complex turbocharging systems.
- Transition barriers: While Cummins is addressing technical challenges, diesel remains the industry standard, and cost-competitive hydrogen systems are still emerging.
- Investment needs: Developing hydrogen-compatible engines and advanced turbochargers requires significant R&D and infrastructure investments. Cummins is focused on innovation that balances performance with affordability.
- Turbo trade-offs: Single-stage systems are simpler and cost-effective but struggle to provide the necessary airflow for hydrogen combustion engines. Two-stage systems offer higher power densities and better performance across a broader range of conditions but are more complex.
- Airflow demands: As engines evolve from diesel to natural gas to hydrogen, demands on air handling systems increase. While natural engines require lower airflow than diesel, hydrogen engines need higher airflow than diesel, necessitating advanced turbocharging solutions to handle these variations.
Cummins’ role in advancing turbocharger technology for H2ICE
In 2023, Cummins unveiled a heavy-duty concept truck with the X15H hydrogen internal combustion engine. In the turbo business, Cummins collaborates with OEMs to integrate next-generation turbochargers into hydrogen engines.
Cummins' collaboration with Accelera™ by Cummins - the zero-emissions business segment of Cummins – also provides unique insights into the future of mobility, accelerating the transition from fossil fuels toward a decarbonized world.
Author Profiles
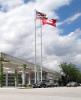
Cummins Inc., Global Power Technology Leader
Cummins Inc., a global power solutions leader, comprises five business segments – Components, Engine, Distribution, Power Systems, and Accelera by Cummins – supported by its global manufacturing and extensive service and support network, skilled workforce and vast technological expertise. Cummins is committed to its Destination Zero strategy – the company’s commitment to sustainability and helping its customers successfully navigate the energy transition with its broad portfolio of products. Cummins has approximately 69,900 employees and earned $3.9 billion on sales of $34.1 billion in 2024. See how Cummins is leading the world toward a future of smarter, cleaner power at www.cummins.com.
Related Topics
Related Tags