Tailored efficiency and optimized performance with Exhaust Throttle Valves
By Cummins Components Business Unit
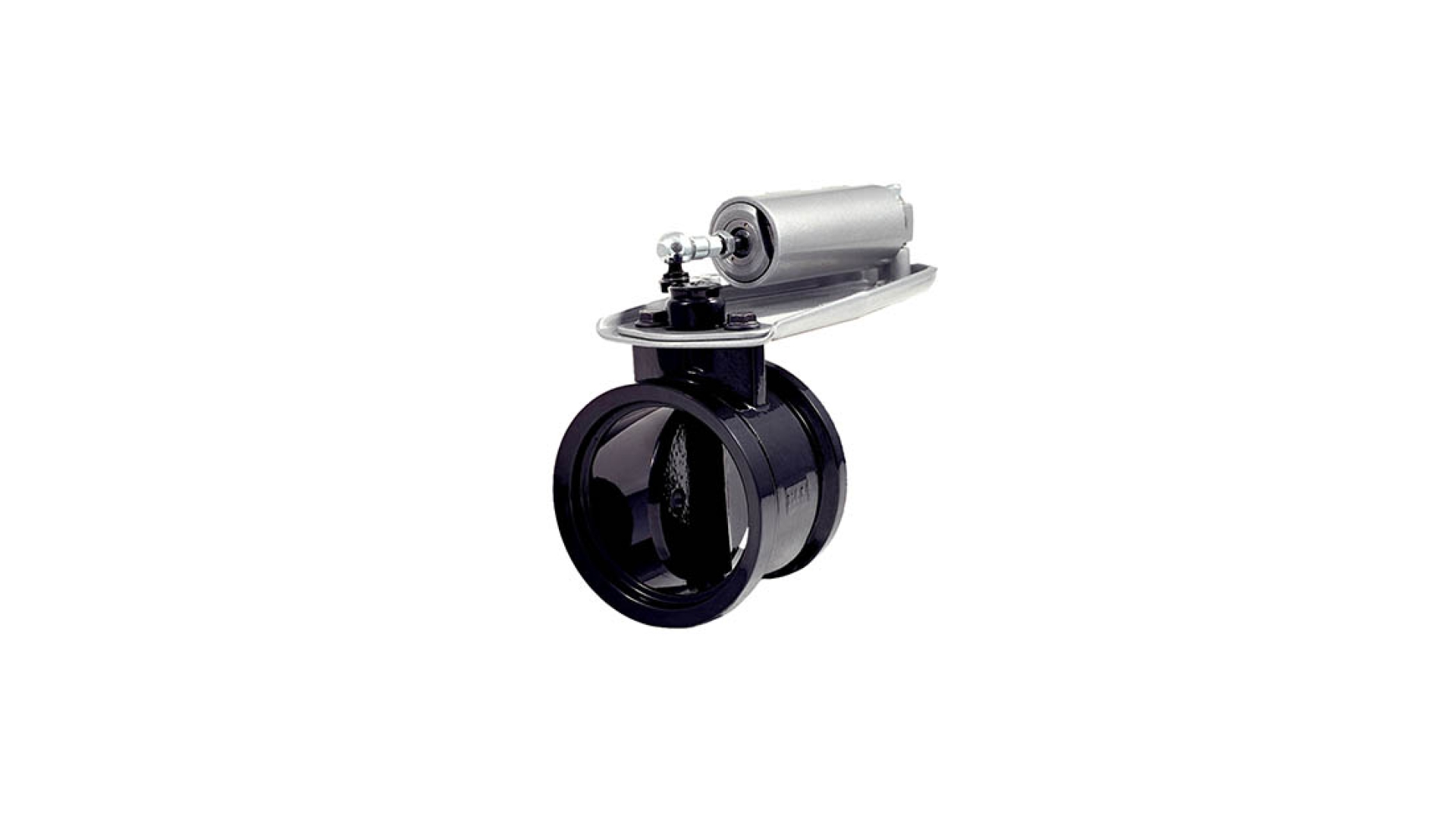
When learning about components that help vehicles run more efficiently and safely, knowing about Exhaust Throttle Valves is crucial. An Exhaust Throttle Valve is a part of the engine that controls how exhaust gases flow out of the engine. It helps reduce pollution by making the engine work hard so it will warm up the aftertreatment system faster. It can also be used as an engine brake by creating resistance inside the engine.
Cummins Components and Software has developed Exhaust Throttle Valves (or Exhaust Brakes) to improve thermal management to enable engine manufacturers to meet strict emission standards. By leveraging advanced air-handling systems, these valves offer a cost-effective, customizable solution with a modular service strategy to reduce ownership costs.
This article explores the role of an Exhaust Throttle Valve and its impact on advancing the efficiency of commercial transportation.
How exhaust throttle valves work
The Exhaust Throttle Valve is a butterfly-shaped valve located downstream of the turbocharger, responsible for regulating exhaust gas flow. It is operated by electronics, mechanics, or pneumatics, helping with exhaust thermal management and supporting after-treatment systems.
Exhaust Throttle Valves improve thermal management by increasing back pressure. Advanced Selective Catalytic Reduction (SCR) systems require a minimum temperature of 250°C for optimal performance, which Exhaust Throttle Valves help achieve. The throttle valve makes the engine work harder and warm up more quickly by providing increased airflow resistance during the exhaust stroke. It also prompts the fuel system to inject additional fuel, raising the temperature, activating the catalyst, and further reducing NOx and hydrocarbon emissions.
Cummins Components and Software business segment applies this same principle to enhance engine braking—higher exhaust pressure increases engine resistance during braking, helping to slow down the vehicle.
Key exhaust throttle valve components and their functions
External components
- Electric or pneumatic actuator: Operates the valve by delivering torque.
- Actuator bracket: Holds the actuator and provides mounting points for wiring harnesses and heat shields.
- Drive plate: Translates actuator movement into shaft rotation and retains the external spring.
- Spring: Ensures failsafe valve opening in case of power failure and provides preload in the valve assembly.
- Valve body housing: Houses the components, manages exhaust flow, and supports the external spring.
Internal components
- Bush: Holds the valve shaft, controls clearance, and enables low friction for smooth operation.
- Flap: Regulates exhaust gas flow by adjusting the Effective Flow Area (EFA).
- Circlip: Prevents axial movement of the top bush and acts as a failsafe.
- Conical washer: Seals the valve assembly to prevent gas leakage and reduces wear on the shaft.
- Bottom plug: Seals the bottom bush to prevent exhaust leakage and provide safety.
Exhaust Throttle Valves play a crucial role across various engine technologies
The Exhaust Throttle Valves offer a tailored, cost-effective solution for emerging markets, and it is more affordable than alternatives like variable geometry turbos. The Exhaust Throttle Valve is designed with stringent regulations in mind, such as India’s BS6, China’s NS6, and the European Union’s EU6. Cummins is enhancing the Exhaust Throttle Valves' capabilities to support better thermal management and engine braking.
- Diesel technology (Euro 6): Exhaust Throttle Valves are used across all Cummins Euro 6 engine programs. In all of them, an exhaust throttle valve is located downstream of the turbo. When the exhaust throttle valve is actuated in an engine, the valve obstructs the flow of exhaust gas thereby making the engine work harder and increasing the temperature of the gas. The Exhaust flap can also be used during a DPF regen event by raising the exhaust gas temperatures.
- Hydrogen Internal Combustion Engine (H2ICE) technology: H2ICE engines require intake throttle valves, with an architecture and working principle like an Exhaust Throttle Valve. Here too, the idea is to restrict or allow gases to flow to optimize engine performance, reduce emissions, and improve fuel efficiency.
- Fuel cell technology: Fuel cells have three valves that also operate similarly to the Exhaust Throttle Valve, with added capabilities to resist embrittlement and better suppress leakage from hydrogen fuels that are less dense than natural gas or liquids. These valves have tailored sealing system solutions which include additional elastomers and special materials that are compatible with the more intense hydrogen environment.
Exhaust Throttle Valve innovation for future emissions standards
Upcoming emissions regulations like EPA27, CARB27, EU7, and NS7 are driving innovation in aftertreatment technologies, particularly affecting the exhaust throttle. Cummins is at the forefront of these developments.
A new approach, dual dosing, involves a close-coupled SCR system where diesel exhaust fluid (DEF) is injected immediately after the turbo or even directly into it. This exposes the exhaust throttle to DEF before it fully decomposes, causing potential corrosion and engine failure. In response, Cummins Components and Software developed a new generation of high-performance exhaust throttle valves made from DEF-resistant materials and low levels of external leakage is achieved on each exhaust throttle, which is especially important for alternative fuel applications like natural gas and H2 ICE.
To provide cost-effective solutions, Cummins has reduced the use of stainless steel in housings to lower costs, enhanced actuator durability to prevent failures, and adapted to modern emissions standards with our dual-dosing SCR system and exhaust throttles. Cummins Components and Software offer various exhaust throttle configurations, including dual position throttles for fixed control and variable position exhaust throttles for precise back pressure management. These can be electronically, or pneumatically controlled and closed-loop control is available to help maintain the necessary temperature for effective emissions reduction.
As transportation and power generation evolve, Exhaust Throttle Valves will remain vital in meeting stricter emissions standards and improving engine performance. Cummins’ tomorrow.
Author Profiles
Related Topics
Related Tags