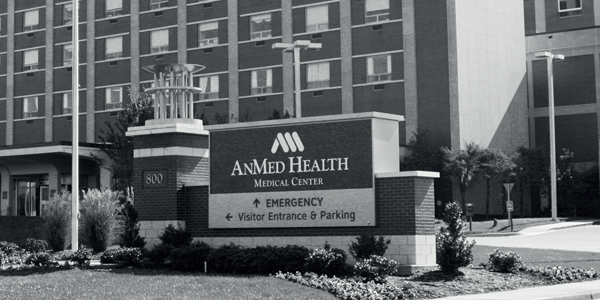
Overview |
||
---|---|---|
Challenge: | Design and install an emergency standby power system as part of a major upgrade at AnMed Medical Center in Anderson, SC | |
Solution: | Cummins installed three 2000 kW diesel fueled generator sets, transfer switches and digital master control (DMC). Prior to installation, a factory “witness” test was conducted at the Cummins plant in Fridley, Minnesota. | |
Result: | The major upgrade at AnMed Medical Center required considerable teamwork and collaboration amongst hospital management and engineering staff as well as numerous external firms. That teamwork has paid off with a state-of-the-art electrical system for AnMed Health Medical Center that protects patients and staff. These first-class results have won national recognition with a VISTA Award for Infrastructure. |
AnMed Health Medical Center
The AnMed Health Medical Center in Anderson, South Carolina, has been serving its community for over 100 years. Following several major expansions in recent decades, hospital executives recognized the need to upgrade the center’s electrical power system infrastructure to meet increased energy demands, improve overall power reliability and ensure the facility met or exceeded the latest NEC code requirements.
The hospital developed detailed specifications and sought bids for a comprehensive upgrade to its electrical plant, including a new emergency power system. Cummins Power Generation won the competitive bidding process and was selected as the primary supplier for a complete emergency standby power system. Another advantage was that the engineering firm AnMed hired to work on the project, PerryCrabb, was already familiar with Cummins Power Generation systems
The comprehensive upgrade also included:
• An expanded central utility plant
• Normal and essential power distribution risers for all eight floors of the hospital
• New distribution risers for data and telecommunications
• A high-rise fire alarm system
• A customized power monitoring and control system
Designing the new emergency standby power system: a complex undertaking
As the director of engineering at PerryCrabb emphasized, when you’re working on a complex design, you need to figure out what is feasible. As a result, there were several detailed discussions about a preliminary system design and the sequence of operations in the planned power system with the Cummins regional manager for Power Electronics. The regional Cummins distributor, then brought in its technical salespeople as well as engineers from the Cummins manufacturing plant to design exactly how the generator sets, transfer switches and digital master control (DMC) equipment would interact with utility power.
Testing and installation
A factory “witness” test was then conducted at the Cummins plant in Fridley, Minnesota. Cummins engineers built a custom “mimic” printed circuit board to simulate how the utility power would interoperate with the Cummins digital master control (DMC), and they also tested all the DMC inputs and outputs.
Then came the actual installation of the generator sets and DMC equipment. Cummins Atlantic took the lead, managing a complex series of interactions with multiple vendors, including Square D and Schneider Electric. The new system was built alongside the one being replaced. The plan called for loads to be gradually transferred from the old system to the new one, and then the old one would be dismantled.
One crucial change was the replacement of an old single-branch emergency power system with a new three-branch system. The older system had been grandfathered in, but the overall upgrade was the opportunity to comply with the current code requirements, which are mandated by the National Electrical Code (NFPA 70) and the Health Care Facilities Code (NFPA 99).
A four-hour “blackout” test was the final step in the installation. This test is mandated by NFPA 110 acceptance test requirements to ensure functional performance of the life safety and critical branches. Chuck Parker, Director of Engineering Services for AnMed Health, said:
“Our acceptance test went beyond the NFPA requirement. We pulled the plug completely on utility power. Because we had sized the Cummins power system to support both emergency and non-emergency loads, the generator sets picked up the entire load; the lights never blinked.”
With this lawless test result, AnMed managers were confident that they had a robust, safe system that could do the job for which it was designed.
A back-up power solution ready for growth
With the new system of three 2000 kW generator sets, paralleling switchgear and automatic transfer switches in place, the hospital now has enough emergency power to handle the loads of the entire facility. But foresight planning for the new emergency power system also took into consideration the need to handle increased loads in the future. A fourth generator set can be easily installed — without interrupting service or adding to the wiring or switchgear — to maintain N+1 redundancy. Closed-transition automatic transfer switches eliminate disruption for testing or anticipatory transfers.
Solving complex problems great teamwork
Successfully executing such a major upgrade to a century-old facility under tight deadlines while the hospital continued to function was a complex planning and logistical challenge. As Chuck Parker explained, “We were replacing the entire electrical system. We moved all the normal, non-emergency circuits over to the new system one at a time. Then we made one big transfer of the emergency circuits for the new construction part of the project, and then another big switch for the older part of the hospital. To make this happen, the different vendors and contractors supported each other and worked together very well.”
First-rate results: increased safety and national recognition
That teamwork has paid off with a state-of-the-art electrical system for AnMed Health Medical Center that protects patients and staff. These first-class results have won national recognition with a VISTA Award for Infrastructure. Since 1993, the American Society for Healthcare Engineering (ASHE) of the American Hospital Association (AHA) and the American Institute of Architects Academy of Architecture for Health (AIA/AAH) have recognized design and construction initiatives across the United States through the VISTA award program.
Chuck Parker summed up the significance of the award: “The VISTA award was a testament to the difficulty of the challenge, the quality of the design and the excellent teamwork among all the people and companies involved.”
Overview Challenge: Red Cross Hospital in Cordoba, Spain needed to replace an older outdated backup genset with a new gens...
Overview Challenge: Krankenhaus Bozen (KH BZ) Antagen Societa Consortile needed to build a new hospital facility in Bolzan...
Overview Challenge: Design and install new generators, digital controls, paralleling switchgear and transfer switches for ...