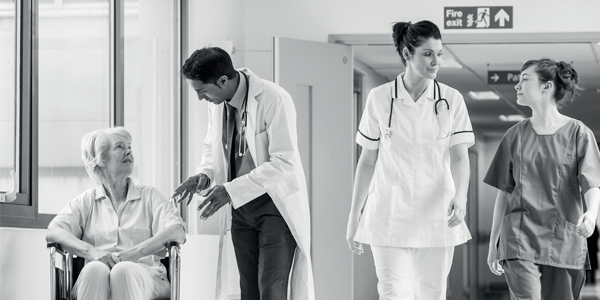
Overview |
||
---|---|---|
Challenge: | Design and install new generators, digital controls, paralleling switchgear and transfer switches for life-safety and supplemental power at one of the largest private medical centers in Louisiana | |
Solution: | Cummins installed one 1750 kW diesel generator and five 1750 kW lean-burn gas generators equipped with PowerCommand® digital controls, paralleling switchgear and transfer switches. In addition, Cummins provided design, installation, technical support, installation reviews and commissioning services. | |
Result: | Cummins was chosen as the vendor for this project due to our ability to provide a completely integrated design, product and service solution including generator sets, unique paralleling configuration, digital controls, switchgear and transfer switches. |
Our Lady of the Lake Regional Medical Center
Our Lady of the Lake Regional Medical Center is a dominant institution in healthcare in the greater Baton Rouge area. It is also the largest private medical center in Louisiana, with 763 licensed beds. It treats approximately 25,000 patients each year in the hospital and serves about 350,000 persons through outpatient locations. The Louisiana Quality Foundation recently conferred its Level III Louisiana Performance Excellence Award on the medical center, so it is no surprise that it turned to another quality manufacturer, Cummins Power Generation, to design and install new generators, digital controls, paralleling switchgear and transfer switches for life-safety and supplemental power.
Cummins Power Electronics enhance system reliability
Several factors influenced the organization’s choice of Cummins. One of these can be characterized as redundant reliability, but not because of the number of generators. Rather, Cummins Power Generation’s switchgear and paralleling configuration provide customers with a unique approach to ensuring operation of the generator sets.
In most backup systems, a control mechanism acknowledges an outage and signals the generators to start. Correspondingly, once power is restored, the control senses the change, ensures the stability of the supply, disengages the generators and reconnects the load back to the grid. Meanwhile, the generators are allowed to cool down and then shut off. Yet, what if the automatic control failed and would not start the generators? That is where the Cummins approach is unique, because each generator can be brought on line manually — a form of fail-safe operation.
With PowerCommand® digital paralleling systems, the master control system and the generator paralleling controls operate independently, but interface directly for optimum system control. In a normal black-start condition, system start signals are sent directly to each generator set and to the digital master control (DCM). The PowerCommand® generator sets independently start and accelerate to rated speed and voltage. The “first start sensor” integrated into the generator controls is used to monitor each generator set as it is started, choosing the first unit to reach operating voltage and frequency, and then allowing that unit to close to the system bus.
A backup control in each generator set is provided in the event that the first start sensor system fails. The second (and all other) generator set paralleling control(s), upon sensing that bus voltage is available, switches on its synchronizer within the PowerCommand® Control and forces the generator set to synchronize to the system bus. When safe paralleling conditions are reached, the PowerCommand® Control closes the paralleling breaker and switches off the synchronizer function. The PowerCommand® Control then communicates with the other generator sets in the system to share the available real and reactive load on the system equally. The Digital Master Control provides signals to add loads to the system in steps so that the system is not fully loaded until all the generator sets have closed to the system bus. Each major component in the paralleling system includes sufficient controls and logic to operate completely autonomously in the event of failure of other system components. This is known as true distributed control.
The generator sets with their paralleling breakers are also autonomous as a group and synchronize, parallel and load share with each other, regardless of the performance of other equipment in the system. Each utility service to the system has an independent control to monitor its condition and control operation of the power transfer system. In other systems, loss of a single component in a single control can cause total system failure. All PowerCommand® controls are designed and interfaced to work together, and the number of system components is reduced, so the entire system is more reliable.
Hurricane-zone back-up power
The need for additional reliability was heightened by the geographic location of Baton Rouge in the “hurricane zone.” This factor was not overlooked when the Cummins team counseled their customer to choose lean-burn, natural gas units as part of the solution. When Hurricane Katrina hit the Gulf Coast, many areas were without power for over a week. The average on-site diesel storage tank typically provides fuel for only 8–24 hours, while natural gas offers an almost limitless supply of fuel that is not interrupted by hurricanes. The Cummins Power Generation solution provides the advantages of both fuel types.
A diesel power generation solution designed for future success
The Cummins diesel generator is designated for life-safety backup power and engages almost immediately when an outage occurs. The lean-burn, natural gas generators provide supplemental power should it be needed in an event. In addition, they can be used in the future to offset the costs of energy during peak periods. There is a growing market for lean-burn natural gas-generated backup and supplemental power. Natural gas provides customers with lower operating costs than diesel. It also allows flexibility, given there is no need to change installed equipment should a customer elect to use the equipment for peak shaving or cogeneration. In addition, minimizing diesel power to the true life safety requirements of the facility allows for maximum power availability.
Overview Challenge: Red Cross Hospital in Cordoba, Spain needed to replace an older outdated backup genset with a new gens...
Overview Challenge: Krankenhaus Bozen (KH BZ) Antagen Societa Consortile needed to build a new hospital facility in Bolzan...
Overview Challenge: Design and install an emergency standby power system as part of a major upgrade at AnMed Medical Cente...