At Cummins, our continuous improvement process demands that we look for new and innovative ways to make engines run cleaner, stronger, and longer. We leverage our unrivaled technical understanding of aftertreatment systems to offer the right technology and support to meet constantly evolving emissions standards for on- and off-highway markets, committing millions of dollars every year to R&D to stay in front of these constantly evolving industries.
Aftertreatment technologies play a critical role in mitigating harmful emissions while ensuring compliance with stringent environmental regulations. As a leader in this field, Cummins employs a range of innovative solutions to address the challenges posed by emission regulations.
Click on the 'blue' spots on this interactive and find out more about aftertreatment systems. Click on Dive Deeper to explore in detail.
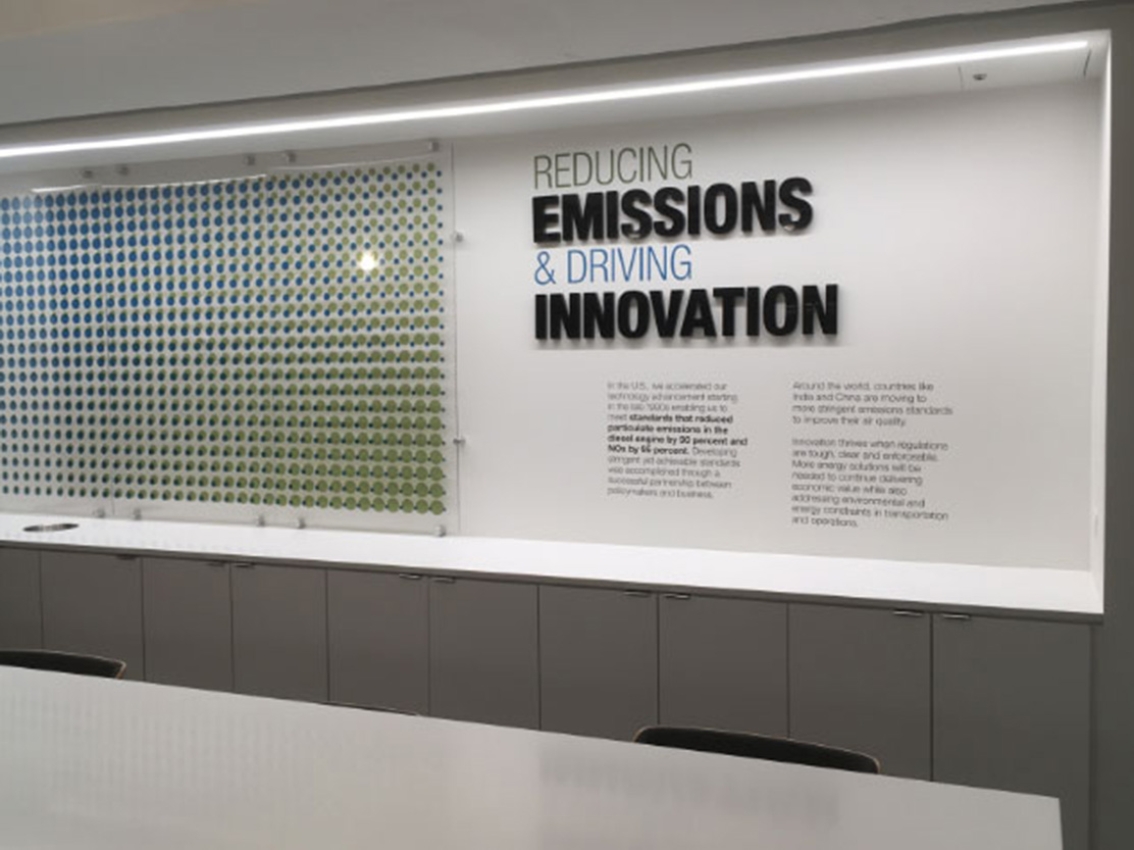
At Cummins, our unwavering commitment to innovation is exemplified through substantial investments in ongoing research and development initiatives. This investment is aimed at staying ahead of evolving emissions standards, exploring new technologies, and enhancing existing solutions. Our proactive approach to R&D ensures that its aftertreatment technologies remain at the forefront of industry standards, providing customers with state-of-the-art solutions.
Research and Development Initiatives
Pioneering Future Technologies
Cummins doesn't merely aim to meet current emissions standards; we strive to pioneer future technologies that anticipate and exceed upcoming regulatory requirements. Our forward-thinking R&D teams explore groundbreaking solutions, pushing the boundaries of what's possible in aftertreatment technology. As part of our commitment to sustainability, we're also dedicated to extending Extended Useful Life (EUL) requirements.
Continuous Improvement and Optimization
At Cummins, the heart of our R&D efforts lies in the continuous improvement and optimization of existing aftertreatment solutions. Through rigorous testing, analysis-based design, advanced system simulation tools, data analysis, and feedback from real-world applications, Cummins fine-tunes its technologies to ensure optimal performance, quality, durability, and environmental impact.
Adaptive Solutions for Varied Applications
Cummins understands that different industries and applications require tailored solutions. That's why we design our aftertreatment technologies to be fit for application, with a keen emphasis on durability and reliability. Our solutions can withstand diverse operating conditions, ensuring optimal performance and compliance with global requirements. By prioritizing durability and adaptability, Cummins delivers aftertreatment technologies that excel in any environment around the globe.
Collaboration and Industry Partnerships
Cummins actively engages in collaborative efforts and industry partnerships to foster a culture of shared knowledge and expertise. By working alongside other leaders in the field, we leverage collective insights and pool resources to address industry-wide challenges and drive innovation collaboratively.
Integration of Advanced Materials and Manufacturing
In pursuit of excellence, Cummins explores the integration of advanced materials and manufacturing processes. This approach not only enhances the performance of our aftertreatment technologies but also contributes to sustainability goals by optimizing resource usage and minimizing environmental impact.
Customer-Centric Solutions
Cummins places a strong emphasis on delivering customer-centric solutions. Through R&D, we actively seek and incorporate feedback from our customers, ensuring that our aftertreatment technologies align with user needs, operational preferences, and industry-specific requirements.
Aftertreatment Technologies
Selective Catalytic Reductions (SCR)
SCR reduces nitrogen oxide (NOx) emissions by injecting a urea-based solution into the exhaust stream, where it reacts with NOx over a catalyst to form harmless nitrogen and water vapor.
Diesel Particulate Filter (DPF)
Cummins' DPF technology significantly reduces particulate emissions, enhancing air quality. It is a key component in meeting particulate emission standards.
Advanced Sensors and Controls
Smart control systems enhance the overall effectiveness and reliability of aftertreatment systems, ensuring optimal performance under diverse operational scenarios.
Diesel Oxidation Catalyst
Cummins' diesel oxidation catalyst (DOC) is designed to reduce carbon monoxide (CO) and unburnt hydrocarbons in the exhaust stream. It plays a crucial role in achieving cleaner emissions by promoting the oxidation of these harmful compounds.
SCR Catalysts
SCR catalysts utilize advanced porous wall structures and efficient catalyst materials to facilitate the selective catalytic reduction process. This results in the conversion of nitrogen oxides (NOx) into nitrogen and water vapor, aligning with emission reduction goals.
Combination Systems
Cummins' combination systems integrate multiple aftertreatment technologies to provide comprehensive emission control. By combining SCR, DPF, and other components, these systems deliver optimized performance across various operational conditions, ensuring compliance with emissions standards.
Natural Gas and H2ICE Boxes
Our Three-Way catalyst systems are used for natural gas engine applications and oxidize exhaust gas pollutants (HC and CO) and reduce nitrogen oxides into harmless components. Our Hydrogen combustion engine (H2ICE) systems use technologies similar to diesel systems such as SCR to reduce oxides of nitrogen, and particulate filters in order to meet the worlds most stringent emission standards.
Diesel Exhaust Fluid (DEF) Dosing
Precise injection of Diesel Exhaust Fluid (DEF) into the exhaust stream of engines equipped with SCR systems helps reduce nitrogen oxide emissions.
Thermal Management Technologies
Electric heaters and hydrocarbon dosers are used to optimize the performance of aftertreatment systems by maintaining the temperature of exhaust gases within the optimal range for efficient emission reduction reactions.