Cummins in Action
Cummins in Action
Mining is a risky business. And that's why at Cummins, our global customers' satisfaction and partnership always remains a top priority.
From haul trucks to excavators, learn more about how Cummins products are always in action when performing in mining applications all around the world and why our customers choose Cummins.
Don’t take risks on power. Run the best. Run on Cummins.
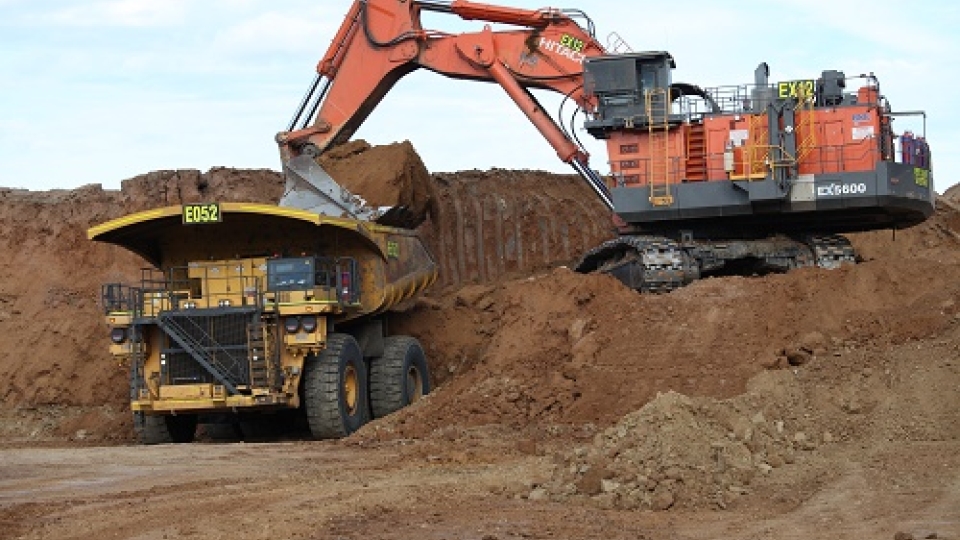
Expanding Cummins footprint at Maules Creek Whitehaven Coal, noted for producing high quality thermal and metallurgical coal, has four operating mines in the Gunnedah Basin which achieved run-of-mine (ROM) production of 18.2 Mt in 2023. More than 100 high horsepower Cummins engines are involved in its three open-cut operations, including the Maules Creek operation which is repowering five Hitac
In February of 2018, a coal mine in Northwest Colorado purchased a Liebherr R 9400 excavator for use at its mining operation. The coal that is unearthed at this site is delivered directly to an adjoining 885 megawatt, coal-fired power station. Mine sites in extreme environments require dependable engines to power their mining applications, which is why this mine called on Cummins to power their Li
In some of the most extreme environments on the planet, mining operations are constantly moving without a break. No matter what, the operation must keep moving every hour of every day. In the mining world, downtime due to any single piece of equipment can result in the loss of tens of thousands of dollars. There are two keys to a successful mine site operation; equipment availability and productiv
Cummins Global Support Team Extends Fuel & Air Filter Hours for Longer Uptime For decades Cummins has been supporting mines across the globe. Our service and support team is filled with talented and dedicated experts that understand how mines work and coordinate efforts both on site and remotely to ensure miners maximize production levels at the lowest possible costs in any envi
Cummins provides more than just engines to serve its fleet of engines at the Julong Mine. The most valuable mineral resources are usually excavated in hard-to-reach locations around the world. This causes difficulty not only for the miners, but also for the heavy machinery used at mine sites. Some of these mines operate at high altitude, where the air quality and severe weather conditions can c
Anglo American mines everything from iron ore to copper, platinum and diamonds across three continents. The one thing they share is a total commitment to using Cummins engines in virtually all their equipment from haul trucks to electrical generators. In this video featuring their Brazilian site, Cummins and local distributor DCML match Anglo American’s commitment with unparalleled support, gen
When Rio Tinto looked to improve life-to-overhaul of the Cummins QSK60 engine powering its Komatsu WA1200-6 loaders, oil filtration efficiency emerged as the key. Rio Tinto has nine 220-tonne, 1892 hp WA1200-6 loaders operating in its vast iron ore operations in the Pilbara, Western Australia, where production reached 330 million tonnes from 16 mines in 2017. A world-first WA1200-6 is workin
A fleet of Cummins-powered Hitachi excavators is pivotal to the success of the $10 billion Roy Hill iron ore mining operations in the red expanse of Western Australia’s Pilbara region. The first iron ore from Roy Hill was shipped in December 2015, and in September 2017 the mine hit a significant milestone, reaching its targeted run rate capacity of 55 million tonnes per annum (Mtpa) for the fir
Eliminating the Obstacles to Longer Engine Life “We operate in a fiercely competitive global business and we will be run down by our competition if we don’t stay ahead of the innovation curve.” These unambiguous words from Chris Salisbury, chief executive of Rio Tinto’s iron ore business, focus precisely on the mining giant’s strategy – a relentless drive for improved productivity, with inno
Data-Driven Maintenance Doubles QSK60-Powered Haul Truck Engine Life Over Past 6 Years, Saving More Than $3.5 Million. Teck is Canada's largest diversified resources company, with major business units focused on copper, steelmaking coal, zinc and energy. Their fleet includes 111 Komatsu 930E haul trucks mostly powered by Cummins QSK60 engines at three of their steelmaking coal operations in Can
Oprima aquí para leer la versión en Español. Everyone in the mining industry knows that the most critical factors for profitability are equipment availability and productivity. In a 24/7/365 operating environment, the loss of a single piece of equipment can cost tens of thousands of dollars. Recently, the Cummins Chile team developed a comprehensive plan to improve equipment availabilit
El sistema de advertencia temprana de Cummins ahorra $ 1.3 millones para mina chilena. Todos en la industria minera saben que los factores más importantes para la rentabilidad son la disponibilidad y la productividad de los equipos. En un entorno operativo 24/7/365, la pérdida de una sola pieza de equipo puede costar decenas de miles de dólares. Recientemente, el equipo de Cummins Chile desa
Cummins QSK60 “Advantage” Solution Delivers Major Environmental And Operational Benefits For Mining Contractor Kalari HSE In Australia’s Bowen Basin. Advantage Cummins. Mining contractor Kalari HSE has taken major steps to reduce carbon and diesel particulate emissions at their South Walker Creek coal mine in Queensland’s Bowen Basin. By upgrading their Tier 1 Cummins QSK60 engines to the
Major Cost Benefits Realized In Global Trials Of New Filter Technology From Cummins Filtration Slashing Maintenance Costs A filter optimization program carried out by Cummins Filtration and Komatsu at Anglo American’s Dawson coal mine in Queensland has resulted in major cost savings through the use of new technology Fleetguard filters to extend service intervals. Cost savings of 60%, thro