Cogeneration examples across industries
By Cummins Inc., Global Power Technology Leader
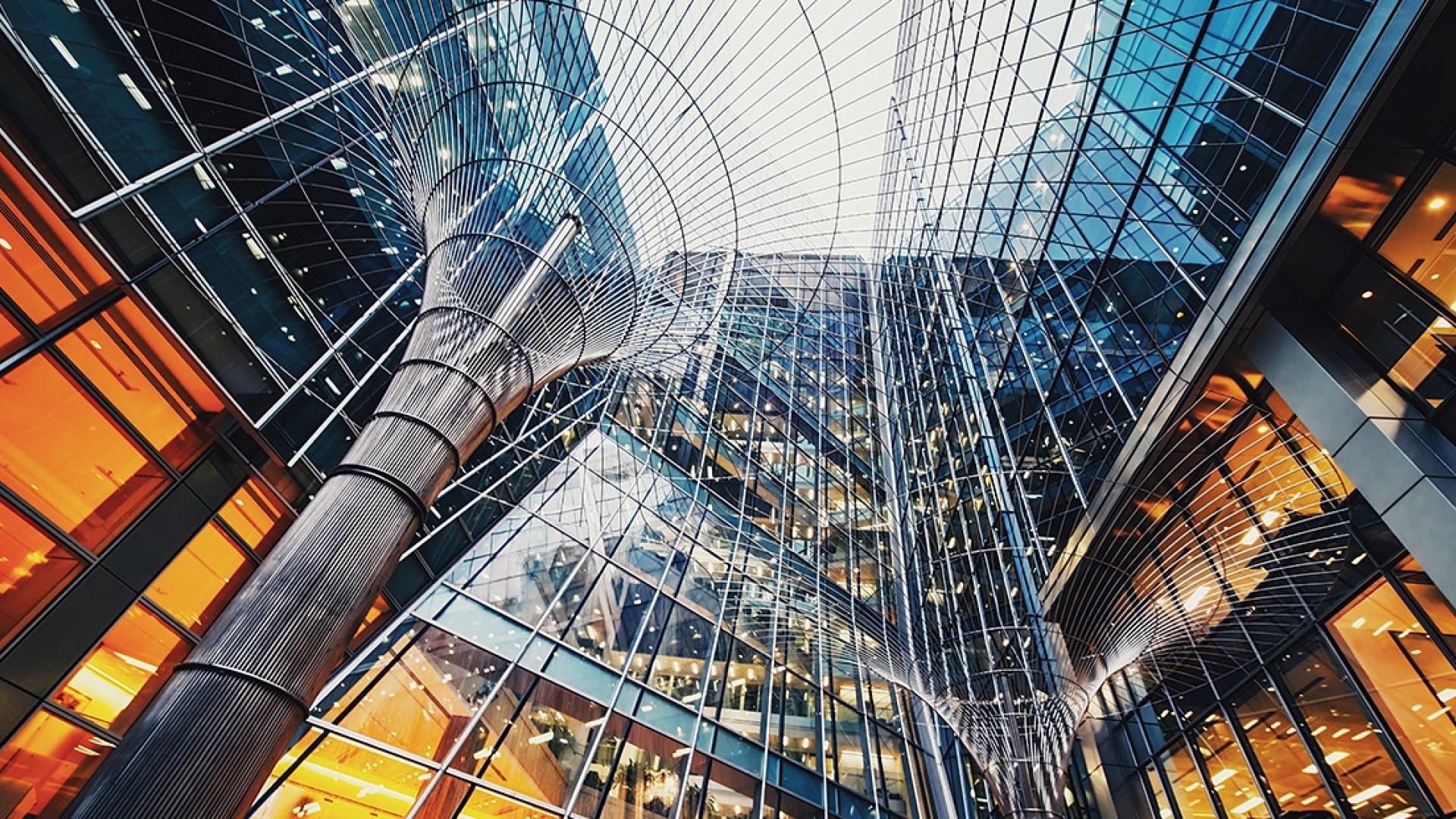
Cogeneration is a well-established power generation technology that is experiencing a resurgence in interest all over the world.
Recent developments have made investing in a cogeneration system a no-brainer for many facility managers seeking to reduce their energy bills and minimize their carbon footprint. These developments include improvements in cogeneration technology, changes in the regulatory environment, and government incentives.
Cogeneration systems are common in many sectors. These include hospitals, nursing homes, universities and a wide range of industrial sectors that involve energy intensive processes. Cement, pulp and paper, iron and steel are some of these industrial sectors. Beyond these traditional cogeneration use-cases, small scale cogeneration recently became an attractive option for smaller energy consumers. This is due to the improvements in heat exchanger and engine technologies. These smaller scale applications include greenhouses, swimming pools and office buildings.
In order to maximize the economic benefits of an investment in a cogeneration system, it is important to carefully assess the energy needs of the facility and evaluate all of the available options.
- Should the cogeneration system cover all or part of the facility’s electricity needs?
- Is it possible to sell excess electricity generated?
- Does it make sense to include solar panels in the investment?
- Should cooling also be provided? (Cogeneration systems that also provide cooling are known as trigeneration systems).
Deciding on the right cogeneration configuration depends on finding a balance between a few parameters. A balance that achieves the best economics, maximizes tax credits and incentives, and incorporates other considerations. Other considerations include space for the plant, environmental regulations, fuel choice, and the need for reliability of supply.
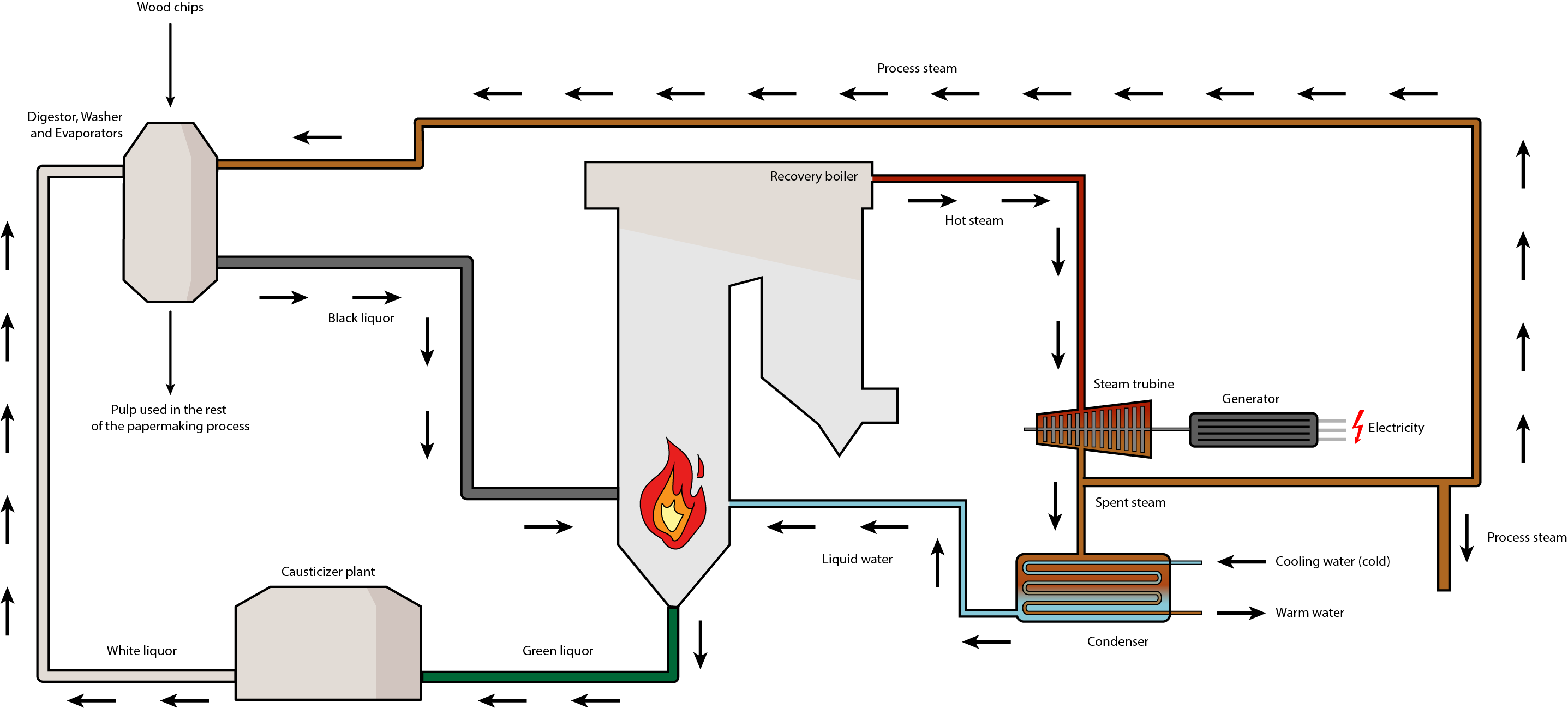
Cogeneration examples in schools, colleges and universities
Educational establishments lend themselves to cogeneration projects, as they require a significant amount of heat as well as electricity. Learning must take place in a comfortable environment, and that comfort costs money. Money that schools and universities could otherwise spend elsewhere; this makes savings on energy costs keenly sought. A typical example is Clark University, in Worcester, Massachusetts, where Cummins Inc. recently upgraded a cogeneration system.
The university was looking to minimize its electricity purchase from the local utility. The university needed the new gas generator set to meet the latest emissions standards and had to install everything in the space occupied by the old boiler. Cummins supplied a C2000N6C 2 MWe QSV91G lean burn gas generator. The generator provides power and heat to the entire campus through the existing system of steam tunnels.
The new generator can cover all of the university’s electrical and heat needs. The University can also export excess electricity to the power grid, resulting in a welcomed revenue stream. The Cummins QSV91G gas generator also features Cummins Power Command controls. The control system allows the university to reduce operations and maintenance costs by remotely monitoring the generator’s performance.
Cogeneration examples in district heating
Scandinavia, Russia and Eastern Europe have long used cogeneration as a means to heat apartment blocks in district heating schemes. Excess heat from local power stations provides the surrounding community with heat via an extensive network of steam pipes. In colder climates, hot water has even been piped under roads to keep them snow-free in winter.
Cogeneration is an efficient option for multi-family residential buildings, where the heating system is communal.
District heating schemes remain an attractive option to this day. They are an effective way to reduce the carbon footprint of entire neighborhoods.
The Hongqiao Business District in the west of Shanghai, for example, covers an area of about 86 km2. The district is a showcase of low-carbon living, featuring a vast cogeneration project. Phase one of the project covers 1.43 km2. It addresses all the heating cooling and part of the power needs of the area, which is home to an international trade center and a high-end business district.
In this project Cummins is supplying a complete power solution centered on eight silenced C1400N5C 1400kWe QSK60G lean-burn gas generator sets; there are also absorption chillers and auxiliary gas boilers. The combined cooling, heating and power model will meet the entire cooling and heating load of the business district, and part of its electrical load as well.
Cogeneration examples in hospitals and nursing homes
Hospitals and nursing homes are big users of electricity, heating, and cooling. This makes them ideal for cogeneration. Additionally, hospitals need standby power. This is because any interruption to the electricity supply could risk loss of life. Therefore, onsite power generation is a consideration for all hospitals.
Standby power can be woven into a cogeneration scheme. This ensures the hospital can have the most cost-effective option to meet its energy needs. Moreover, it also ensures the power supply is always reliable. A mix of utility and independent electricity supplies is a desirable option for critical services, making maintenance shutdowns easier.
An example would be Australia’s Royal Children’s Hospital; in this project, Cummins installed a trigeneration system. Within this system, natural gas generators provide electricity, heating and cooling, and diesel generators provide critical standby power. The trigeneration system supplies baseload power, heating, and cooling via an absorption chiller. Alongside, the grid supplies the peak electricity. In case of a power outage, the diesel generators can kick in to work in tandem with the gas generators covering life safety loads ensuring power continuity.
Key to the choice was Cummins’ ability to integrate the generators rather than having separate electrical systems. As one of Australia’s greenest hospitals, the reduction in CO2 emissions inherent in cogeneration was also a major factor in determining the specification of the system.
Cogeneration examples in industrial plants
The case for cogeneration in industry is strong, as many industrial processes require steam and/or heat. In addition, many industries produce waste gases. Those gases are increasingly the focus of environmental legislation. Utilizing these gases to fuel the cogeneration plant is a win-win solution.
One such example is the Columbus Water Works, where biogas generated as a by-product of wastewater treatment was used as a fuel source to run the cogeneration plant. Cummins installed two 1.75 MWe C1750 N6C QSV91 dual-fuel lean-burn gas generator sets. These power generators are able to run on either biogas or natural gas, as required.
Similarly, at the Syracuse, Utah, Wastewater Treatment Plant, Cummins upgraded gas generators and provided a cogeneration solution. The new solution eliminated the environmental concerns associated with the plant’s gas flaring. The cogeneration system provided useful heat for the digesters and hydronic heaters operating on site.
In other industrial situations, reliability of the electricity supply is a concern. This is especially applicable in the developing world. Factories working to complete orders cannot afford to have frequent outages due to unreliable local grids.
Cummins installed a trigeneration system at a Nigerian Bottling Company factory to supply steam, cooling, and electricity. The system solved the difficulties posed by the frequent grid power outages. The bottling company also sells surplus electricity to the local utility. Additionally, Cummins organized the supply of compressed natural gas (CNG) to run the generators, as there is no natural gas network nearby.
Interested to learn more about cogeneration? You might also like:
- What is cogeneration, its benefits and how does cogeneration work
- Three situations that maximize the advantages of cogeneration applications
- Three key benefits of cogeneration
- Types of cogeneration using gas turbines, engines, and fuel cells
Cogeneration technology is suitable for a wide range of industries and facilities beyond those described. These include almost any sizeable building requiring heat for a large part of the year, and almost any industry needing heat as part of its process. The potential for reducing fuel and electricity costs makes the technology an attractive option for many applications.
Author Profiles
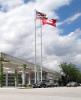
Cummins Inc., Global Power Technology Leader
Cummins Inc., a global power solutions leader, comprises five business segments – Components, Engine, Distribution, Power Systems, and Accelera by Cummins – supported by its global manufacturing and extensive service and support network, skilled workforce and vast technological expertise. Cummins is committed to its Destination Zero strategy – the company’s commitment to sustainability and helping its customers successfully navigate the energy transition with its broad portfolio of products. Cummins has approximately 69,900 employees and earned $3.9 billion on sales of $34.1 billion in 2024. See how Cummins is leading the world toward a future of smarter, cleaner power at www.cummins.com.