A city quarter built on renewable energy opens in Esslingen, Germany
By Katherine de Guia, Communications Specialist - New Power
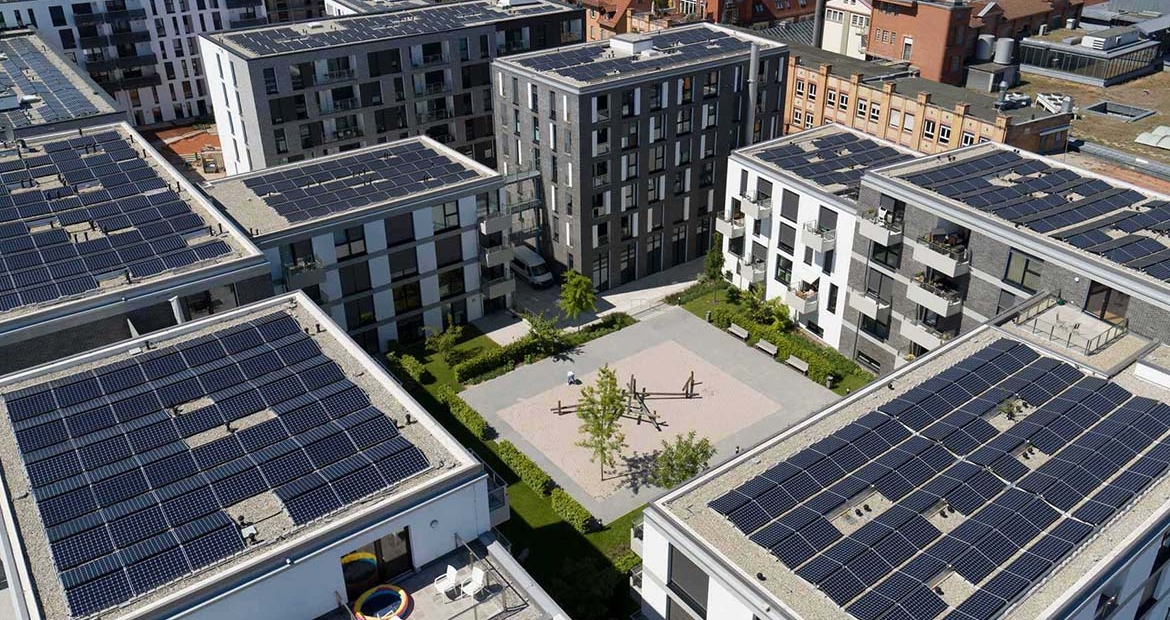
Across the globe are renowned urban quarters – cities within cities that capture the hearts of travelers with their rich history and architecture. New Orleans has the historic French Quarter, Cuba has New Havana and now Esslingen, Germany, has the world’s first largely climate-neutral urban quarter powered by Cummins electrolyzers.
This urban quarter is considered a "lighthouse" project, a small-scale but big-picture project that will serve as a model – or lighthouse – for similar projects in the future. Developed by scientists in Esslingen and Stuttgart and funded by Germany’s Federal Ministry of Economics and Technology and Federal Ministry of Education and Research, this lighthouse project combines hydrogen technology and photovoltaics to create an energy center that fully connects all aspects of infrastructure with everyday urban life.
Named Neue Weststadt (which translates to New West Town), the newly opened quarter spans 100,000 square meters with over 450 apartments, office buildings and commercial space. A city quarter of this caliber has never been attempted before and is a historic milestone for climate-neutral living. It has been three years in the making to transform a former freight yard into the future blueprint for near zero-emission urban centers.
To make New Weststadt and climate neutrality possible, the quarter needed to integrate solar hydrogen technology for use in urban development to achieve an energy supply that should cause zero climate-damaging emissions and reduce energy consumption without reducing the comfort of living.
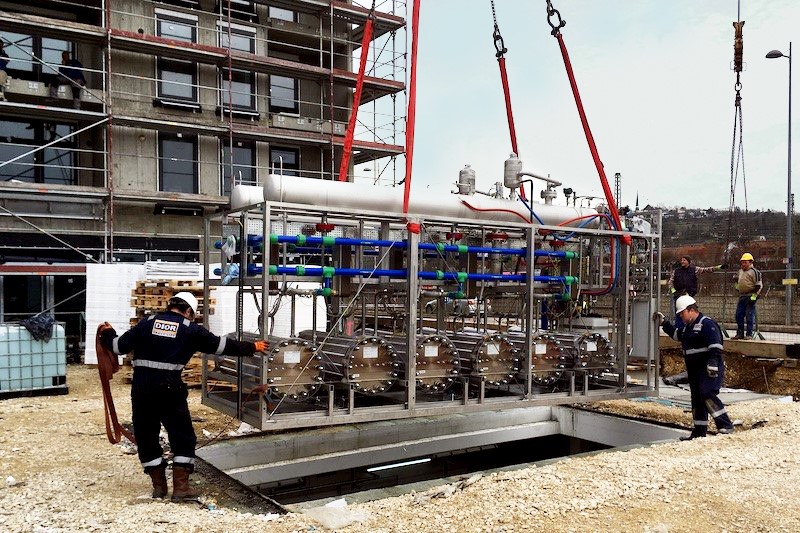
Powering the heart of Esslingen
Photovoltaic (PV) power is the root for the quarter’s renewable energy supply. PV systems are comprised of one or more solar panels combined with an inverter and additional electrical and mechanical hardware to harness energy from the sun to generate electricity. These panels are positioned on the roofs of the buildings in New Weststadt and will work in tandem with the heart of the quarter’s energy center – Cummins electrolyzers.
Commissioned in May, this installation of our electrolyzers was unique from the start. The HySTAT® 100-10 is typically used for indoor electrolyzer projects, but for New Weststadt, we installed the two electrolyzer systems in the energy center’s lower basement. This required unique design elements for hydrogen zoning, access to the basement and installing the vent line out of the basement to meet safety standards. Cummins adapted to these challenges and was able to install the electrolyzer systems in the basement prior to the closing of the basement roof.
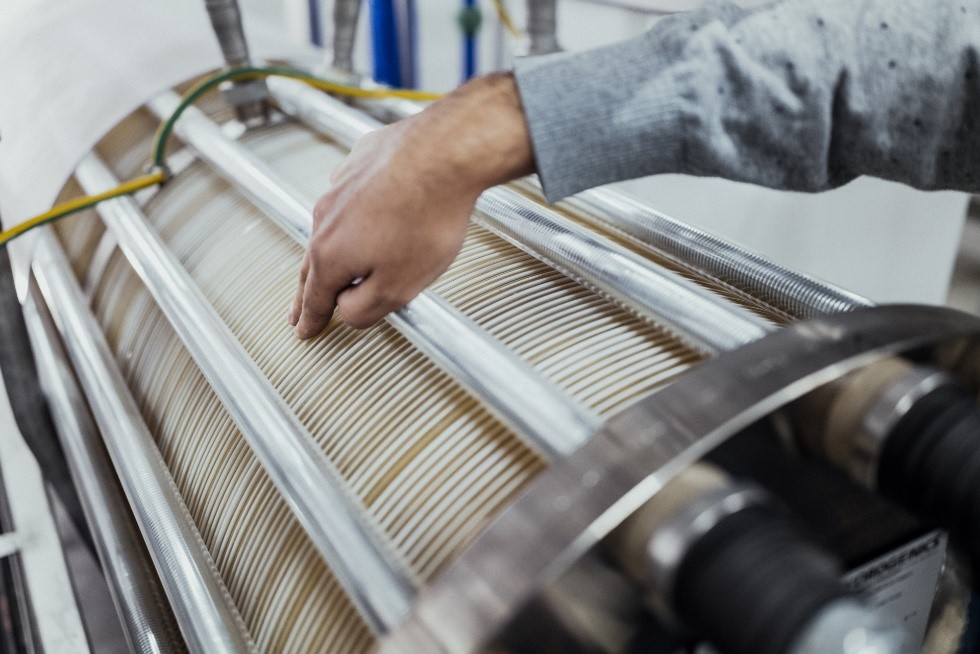
The energy center is located in the middle of New Weststadt and was built as an underground structure to meet urban planning requirements. The two HySTAT® 100-10 electrolyzers have utilities on separate skids (instrument air, reverse osmosis). They are integrated with heat management to recover excess heat from the electrolysis process and with electric management to regulate H2 production from photovoltaic power.
Taking the surplus renewable energy from the PV systems and from the supra-regional generation, the electrolyzers will create green hydrogen through electrolysis. The excess heat generated by the electrolysis process is captured and put back into the power supply, while green H2 is stored for later use according to the quarter’s energy demands.
Connecting power, heat, cooling and mobility
The quarter's connection of the electricity, heating, cooling and mobility sector are all combined at the local level. The crosslinked infrastructure covers the demand of heating and hot water in the buildings and provides cooling energy in the summer through absorption cooling systems.
The stored energy from the electrolysis process can be quickly and easily converted back into electricity in combined heat and power plants. The hydrogen produced will also be fed into the quarter's natural gas grid to contribute to the decarbonization of the gas sector. There are also future plans to build an H2 filling station and a gas grid feed-in station on site.
The linked energy supply is important for long-term and sustainable urban development. This climate district is projected to produce 85 tons of hydrogen per year. A portion of that hydrogen will be stored to use as power for the quarter, while the rest will be loaded into hydrogen trailers and transported to customers in the industrial or public transport sector in Germany.
Every aspect of this virtually climate-neutral city quarter was designed to work as a holistic system through the energy center and monitored using a digital information network and energy management system (EMS). The EMS is meant to increase self-provision of localized renewable energy, while interacting with the quarter’s power grid in an energy-efficient manner and minimizing CO2 emissions.
A blueprint for the future of climate-neutral living
The first of the apartment buildings was completed two years prior to Neue Weststadt’s official opening, and residents have already begun living in their new, climate-neutral homes.
Local public transport is being redesigned to replace existing diesel buses with electric hybrid buses, a wider range of public and semi-public charging stations for electric vehicles are being installed and preparations are being made for a second expansion to build a H2-filling station.
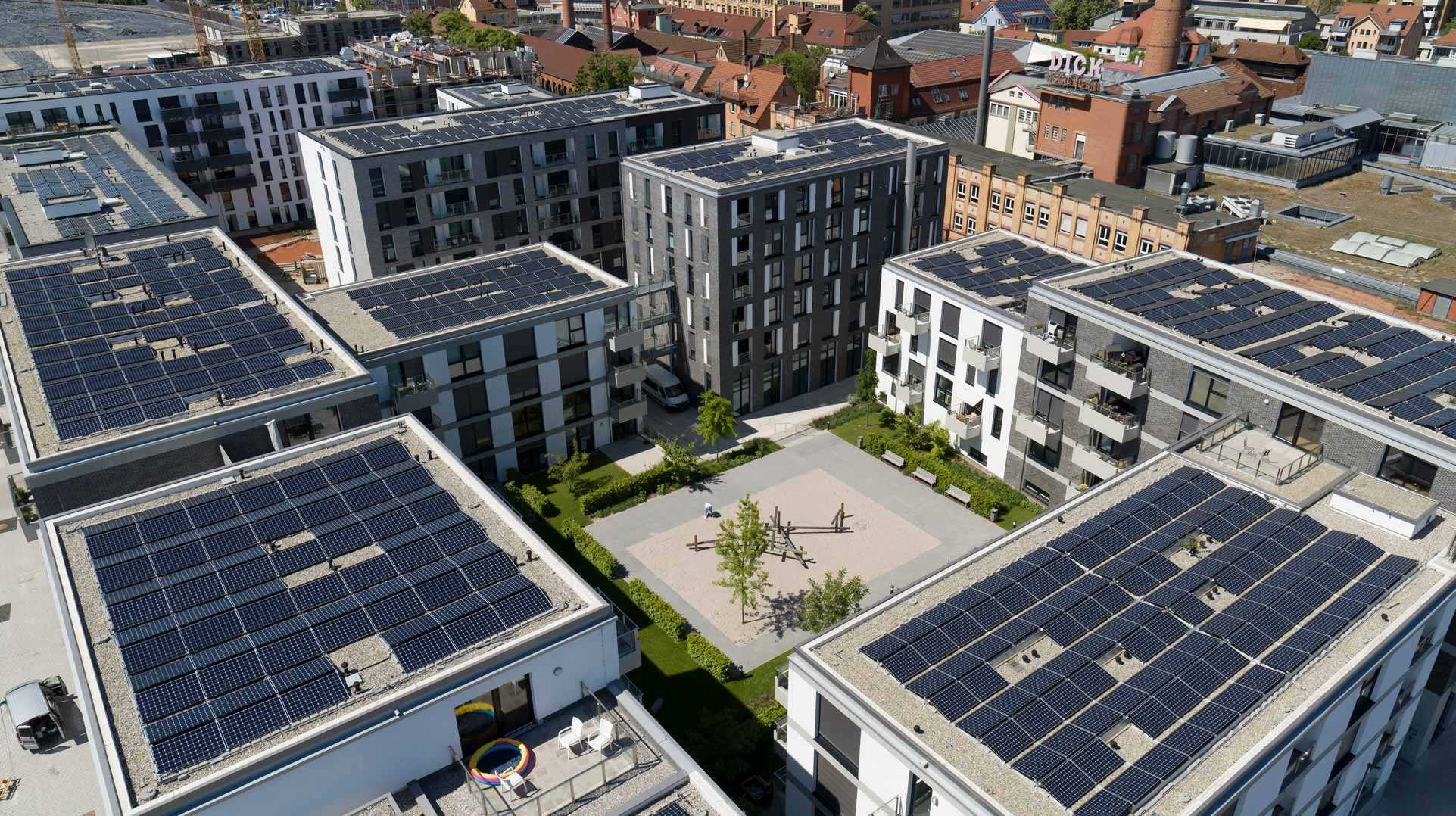
The Klimaquartier Neue Weststadt project developed into a truly unique urban quarter and is now a beacon and blueprint for future climate-neutral urban quarters. It’s official opening on June 22 was just the beginning, and we are excited to see how a community built on renewable energy will undoubtedly influence the future of climate-neutral living.
Author Profiles
Katherine de Guia, Communications Specialist - New Power
Communications Specialist - New Power
Related Tags