What is a dual fuel engine, and its benefits for oil and gas applications?
By Aytek Yuksel, Content Marketing Leader - Power Systems
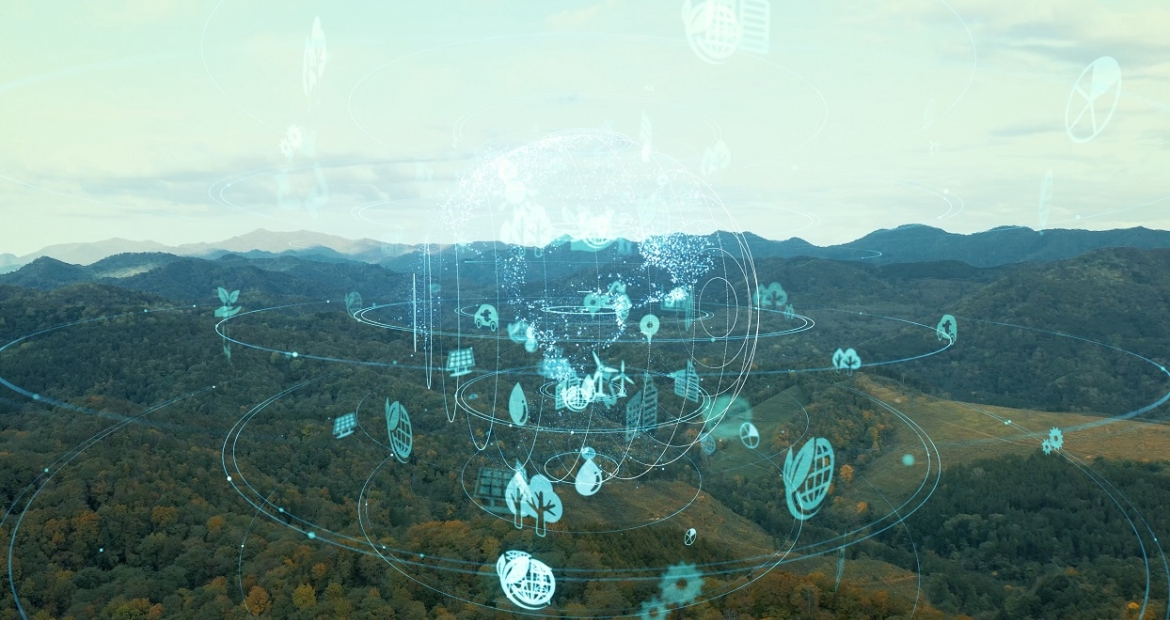
The stone age did not end because the world ran out of stones, and the oil age will not end because we run out of oil1. Instead the oil age will end as we (communities, companies, and governments) speed up the energy transition towards our final destination: 100% renewable energy.
In this energy transition journey there are giant steps we all celebrate, such as the increased use of green hydrogen in rail applications. There are also incremental steps – those that are towards the right direction, those that challenge the status-quo and those that bring us closer to our end goal.
The oil and gas industry is taking incremental steps to reduce its environmental footprint and improve its financial performance. One of these steps is the use of dual fuel engines, which is seen as the right immediate next step. The industry is already utilizing technologies ranging from microgrids to ultra-low emission engines in this journey. Duel fuel engines are the right addition to this portfolio.
Dual fuel engine technology has proven itself over the years in drilling and well servicing applications. Given the increased interest in these dual fuel solutions, this article outlines what dual fuel engines are and their benefits in oil and gas applications.
What is a dual fuel engine and how does it work?
Engines that can operate using a mixture of two different fuels are called dual fuel engines. Frequently, diesel and natural gas fuels are used together within dual fuel engines. Often, dual fuel engines that mix diesel and natural gas can also operate using diesel fuel only if the natural gas is temporarily unavailable.
Beyond natural gas and diesel, some dual fuel engines can also use varying mixtures of biodiesel, landfill gas, bio-gas and other fuels.
Are all dual fuel engines the same?
They are not; the differences among duel fuel engines are far beyond "tomayto" and "tomahto".
While the working principles of dual fuel engines are the same, those that operate dual fuel engines experience remarkable differences in total cost of ownership (TCO) and uptime. Things like natural gas substitution rate, quality of the natural gas, emissions produced, and equipment reliability can all effect operational efficiency.
Substitution rate is a key word associated with dual fuel engines. Substitution rate is the portion of fuel energy provided by natural gas. When comparing dual fuel engines, there are two important considerations regarding substitution rates:
- Load factor: It is important to compare substitution rates of different engines at the same load factor, which is where your engines usually operate. Strictly comparing ‘maximum’ substitution rates of different engines could mislead you, and prevent you from maximizing the benefits of dual fuel engines.
- Diesel fuel consumption: Consider evaluating the diesel fuel consumption rates of the engines while comparing substitution rates. If an engine delivers better diesel fuel economy, then that engine starts the substitution rate comparison with an important advantage.
Check out how dual fuel engines work to learn more.
Benefits of dual fuel engines in oil and gas applications
Within oil and gas applications, drilling and well-servicing operations are where you could commonly see dual fuel engines powering equipment. This is due to the financial and environmental benefits drilling and well-servicing contractors experience with dual fuel engines. Let’s look at these benefits of dual fuel engines in oil and gas applications.
Dual fuel engines reduce the environmental impact of oil and gas operation
Natural gas is often dubbed as ‘the bridge to the renewable future’ in electricity generation markets. In fact, 40% of utility-scale electricity generated in the U.S. comes from natural gas. The rest is evenly distributed among coal, nuclear power and renewables.
"Environmental considerations are a key reason many businesses, including drilling and well-servicing operators, choose natural gas over other fossil fuels,” said Patricio Escobar, Cummins' Oil and Gas Market Segment General Manager. “Those that choose to replace diesel with natural gas experience several critical environmental and operational benefits.", he also said.
Here are three of these environmental considerations.
- Reduced diesel fuel refining and transportation: Diesel fuel goes through a long journey to get from the wellhead to your fuel tank. By using the available on-site gas in your dual fuel engines, you also reduce the need for those operations to process and deliver diesel fuel to your site. This, in turn, reduces the associated environmental impacts of transportation and refining.
- Reduced flaring: Another key environmental advantage achieved through the use of on-site natural gas, is the reduction of flaring. The excess natural gas burned through flaring can be redeployed to power the dual fuel engines on a well site.
Dual fuel engines deliver financial savings through reduced diesel fuel consumption
Fuel cost is one of the primary expense line items for drilling and well-servicing operations. Dual fuel engines bring financial savings in the form of reduced operating expenses (OpEx).
Here is how reduced operating expenses come to life.
- Substituting the diesel fuel with natural gas fuel: As mentioned previously, diesel fuel goes through a longer journey in reaching the engines on a well site. This journey includes oil production, oil transportation, diesel production at a refinery, storage, transportation, and delivery to the pump truck. All these steps within diesel’s journey come with additional costs. Meanwhile, natural gas produced at the wellhead can be processed on location and delivered to the engines. Using available on-site natural gas instead of diesel, results in operational savings for drilling and well-servicing contractors.
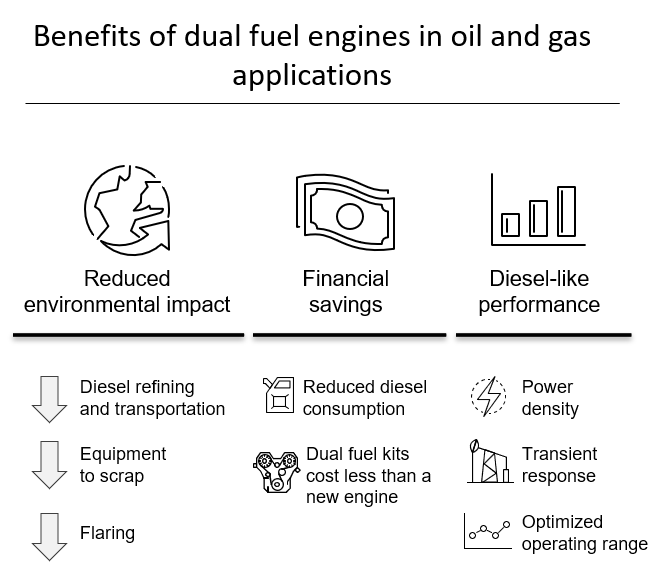
Dual fuel engines operate with diesel-like performance
Historically, one key reason diesel engines have been the top choice among oil and gas applications has been their solid performance. Diesel engines are known for their longevity and diesel fuel offers very high power density. These are still very much accurate. Meanwhile, natural gas engines have changed over the years too. Let’s look at engine performance from three aspects:
- Power density: Power density is an engine’s power output per unit of engine volume. For example, for large displacement engines, you would often see larger natural gas engines deliver power output comparable to smaller diesel engines. In other words, diesel engines have higher power density than natural-gas only engines. Meanwhile, there are also diesel engines upfitted for dual fuel applications. This combined with the electronic controls within the engine allows a dual fuel engine to feature diesel-like power density while operating in dual fuel model.
- Transient response: Transient response performance is an engine’s ability to respond to varying power demands of the operation. Many oil and gas applications require transient response capabilities that 100% natural gas engines often have trouble accommodating. Meanwhile, selected dual fuel engines can offer comparable transient performance with their diesel-only alternatives.
- Optimized operating range: Engines often run at a standard duty cycle per the application they are used in. Applying a new technology, like dual fuel, can sometimes require changes to that operating pattern to achieve the maximum fuel savings. The dual fuel engine's optimization resolves this issue by ensuring the maximum substitution rate of natural gas in the ideal operating range required by oil and gas applications. This maximizes the portion of fuel energy provided by natural gas, leading to improved performance in oil and gas applications.
If you already have engines ready to be upfitted, dual fuel kits will save you money
Many oil and gas applications already use engines that are ready to be upfitted using dual fuel kits. This is a great starting point, because you can now save money and help the environment by choosing a dual fuel kit over a new dual fuel engine.
- Financial benefits: The dual fuel kit costs less than buying a new engine and requires minimal changes to the existing engine, resulting in reduced equipment integration efforts. This reduces the total capital required to upgrade your fleet and achieve operating and sustainability goals.
Interested in more oil and gas perspectives? You might also like:
-
Drilling pads with lower OpEx, reduced carbon footprint and higher safety
-
Reducing greenhouse gas emissions of engines in the oil and gas sector for improved sustainability
To learn more about oil and gas power solutions, visit our webpage.
References:
1The Economist (Jul 24, 1999). Fuel cells meet big business [Article]. Retrieved from https://www.economist.com/
Author Profiles
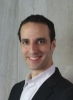
Aytek Yuksel, Content Marketing Leader - Power Systems
Aytek is a marketing leader at Cummins, focusing on technology and thought leadership. Since joining in 2008, he has held various marketing roles and now shares insights on markets, technologies, and energy transition. Aytek lives in Minneapolis with his wife and two kids.
Related Topics
Related Tags