What is the Electronic Control Module (ECM)?
By Cummins Inc., Global Power Technology Leader

Understanding what helps modern engines operate at their peak performance requires an understanding of their key components. The following article explains the crucial role of an engine's Electronic Control Module (ECM) and how it optimizes the performance, efficiency, and reliability of on-highway and off-highway applications. To know more about the ECM, dive into the details of how the Electronic Control Module (ECM) functions.
Role of the Electronic Control Module (ECM) in engines:
In modern engine design, the ECM is like a minicomputer located in the heart of an engine. The ECM ensures the smooth operation of the engine by monitoring and collecting data from sensors positioned throughout the engine and vehicle. This data flow allows the ECM to not only optimize engine performance but also adjust critical parameters like fuel consumption and ignition timing, thereby playing a pivotal role in enhancing engine efficiency while reducing fuel usage.
The ECM also conducts diagnostics, a vital tool for mechanics and technicians to conduct preventative maintenance or troubleshoot if issues arise. In the event of an engine malfunction, the ECM records a series of unique fault codes that are specific to the problem. Technicians can access these codes, providing them insights into the nature of the problem, and enabling quick repairs.
Overall, the ECM functions as the engine’s brain as it continuously assesses, adjusts, and records the performance of engine processes. By choosing engines equipped with ECMs, operators can ensure their vehicles remain efficient and dependable, keeping them on the road or at a job site for longer.
What are the components of the Electronic Control Module (ECM)?
Microcontroller: The microcontroller acts like the central processing unit in a computer. It controls and coordinates the actions of all other components in the system. As the brain of the ECM, it receives raw data from various sensors located throughout the engine. The microcontroller processes this data and converts it into actionable insights. This allows the engine to respond to different operating conditions and demands. For example, the microcontroller can help adjust the ignition timing to optimize the combustion process and reduce the release of pollutants.
Memory: The ECM’s memory includes read-only memory (ROM) and random-access memory (RAM). ROM is the permanent storage for crucial software like the ECM’s operating system and firmware, which controls the ECM's basic operations. RAM temporarily stores data about the engine's current state, enabling the ECM to adjust engine performance in real time. For example, at the time of fault code occurrence, the ECM can record critical engine parameters (sensor values) like engine speed, Intake Air Manifold temperature, coolant temperature and store this information in ROM. This stored information can be accessed later by service technicians providing them much deeper insights into the nature of the problem.
Input/Output (I/O) ports: The I/O ports are the ECM's communication channels. They connect with the vehicle's sensors and other components and help enable data flows. For example, the ECM receives data about engine speed and temperature from sensors. It then adjusts fuel intake valves or ignition timing as needed, thereby reducing fuel consumption.
Analog-to-Digital Converter (ADC): Microcontrollers need information in digital format for processing information. The ADC converts analog signals from the vehicle's sensors into digital signals for the ECM. It may change the analog signal from a temperature sensor into a digital format, helping the ECM to control the engine's cooling system. By providing analog temperature data the ADC converts the information to digital format to ensure that microcontroller can understand engine temperature values and take corrective actions, so that the engine is running at optimal temperature. This in turn reduces emissions and improves the life of the engine.
Voltage Regulator: The voltage regulator maintains the steady voltage supply from the vehicle's battery to the ECM. A constant voltage supply is essential for the ECM to perform tasks accurately and reliably like maintaining optimal engine speed under various load conditions. This helps reduce emissions by ensuring that the electrical system of the engine is running efficiently.
Clock: The clock synchronizes the microcontroller within the ECM. By keeping the ECM's operations timed correctly, it ensures smooth engine operation. It helps determine the precise firing of spark plugs, a vital action for proper engine combustion. If the spark plugs do not fire at the right time it can result in incomplete combustions which can lead to increased emissions.
Power Capacitor: The power capacitor stabilizes the ECM's voltage supply during sudden changes or voltage spikes. This stability is critical for maintaining the ECM's accuracy and reliability. For example, when a truck suddenly accelerates, the power capacitor can throttle the voltage being sent to the ECM to ensure it is not overloaded and that it continues to function correctly.
How do the components of the Electronic Control Module (ECM) vary across vehicle technologies?
The fundamental components of an ECM are similar in diesel, hydrogen internal combustion engine (ICE) powered vehicles, battery electric vehicles (BEVs) and fuel cell electric vehicles (FCEVs). However, the ECM components in BEVs and FCEVs must be designed to manage high voltage and high current applications.
In an electric vehicle, the ECM controls and monitors various systems, including the electric motor, battery functions (e.g., state of charge and state of health), charging systems, DC-DC and AC-DC converter.
In an FCEV, the ECM also controls and monitors systems such as the hydrogen supply, air system, thermal and water management systems, and storage system.
Cummins offers a range of Electronic Control Modules to suit a variety of applications. Cummins’ ECMs can work with diesel, natural gas, battery electric, fuel cell technology as well as after-treatment systems.
Author Profiles
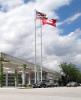
Cummins Inc., Global Power Technology Leader
Cummins Inc., a global power solutions leader, comprises five business segments – Components, Engine, Distribution, Power Systems, and Accelera by Cummins – supported by its global manufacturing and extensive service and support network, skilled workforce and vast technological expertise. Cummins is committed to its Destination Zero strategy – the company’s commitment to sustainability and helping its customers successfully navigate the energy transition with its broad portfolio of products. Cummins has approximately 69,900 employees and earned $3.9 billion on sales of $34.1 billion in 2024. See how Cummins is leading the world toward a future of smarter, cleaner power at www.cummins.com.
Related Topics
Related Tags