Benefits of cold testing vs. hot testing for turbochargers
By Cummins Components Business Unit
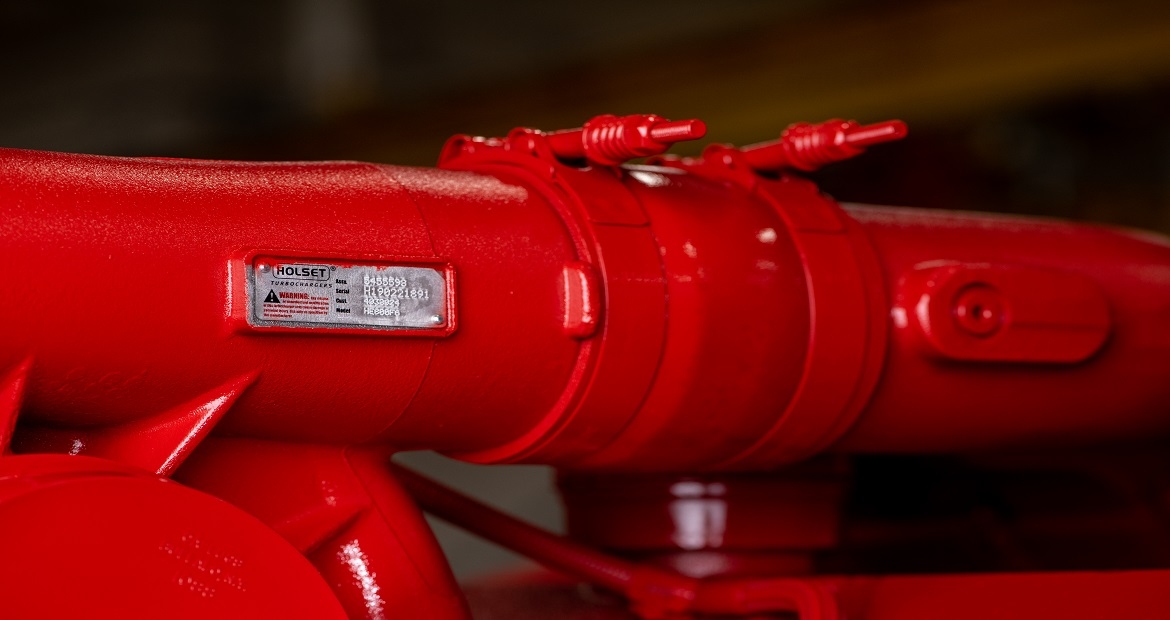
Before a turbocharger is ready to be installed in an engine, it needs to be tested to ensure it works properly with no defects. There are two main methods for turbocharger testing: cold testing and hot testing. This article examines the differences between these testing methods and the advantages of cold testing. As companies search for ways to operate more sustainably, cold testing has emerged as a key procedure to help accomplish this.
Cummins Inc. has found remarkable success in using the cold testing method to test its turbochargers.
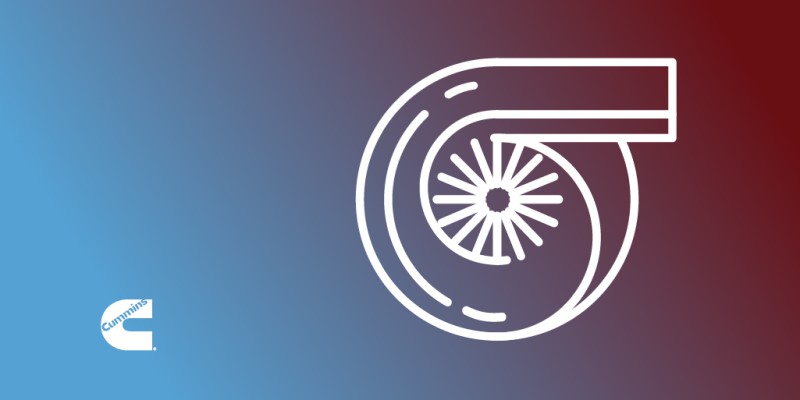
What is the difference between cold testing and hot testing?
Cold testing and hot testing are the two main testing methods that have different procedures to test turbochargers after their assembly. Cold testing is undertaken after the final assembly of the turbocharger. This technique involves spinning the turbocharger using plant air pressure (unfiltered, pressured air compressed to 80-120 psi) that enables the detection of manufacturing and supplier defects. While cold testing seems simple, it has proven to be highly effective in pinpointing inconsistencies and issues that might go unnoticed by hot testing.
Hot testing is conducted by placing the turbocharger within a dedicated test cell. The turbocharger is then monitored to see if it functions properly within an engine environment in the test cell. Hot testing, therefore, provides insights into the turbocharger's operations in real-world conditions. But it might not be as effective as cold testing in identifying defects. Cold testing focuses on detecting any potential leaks. This precision offered by cold testing, especially in leak detection, is a key advantage over hot testing.
Benefits of cold testing vs hot testing:
- Cold testing is more efficient: By using plant air pressure to spin the turbocharger, cold testing can swiftly detect manufacturing and supplier defects. This streamlined approach not only speeds up the testing process but also minimizes the chance of overlooking potential issues that might arise in the functioning of the turbocharger.
- Cold testing has environmental advantages: Hot testing requires using an engine that burns fossil fuels with carbon emissions. Cold testing, on the other hand uses plant air pressure that leaves a minimal carbon footprint. As the transportation industry continues to search for more sustainable practices, the reduced environmental impact of cold testing aligns well with that goal.
- Cold testing benefits end customers: Cold testing of turbochargers offers heightened efficiency and precision in detecting defects. Turbochargers that undergo cold testing are less likely to encounter issues once they are in the hands of the end-users. This translates to fewer maintenance concerns, reduced downtime, and a more reliable product. By ensuring the quality and durability of turbochargers through cold testing, Cummins Turbo Technology (CTT) can provide a product that meets the high standards and expectations of their customers.
- Cold testing is safer: Hot testing of turbochargers uses diesel fuel which is ignited to heat up the turbocharger inside the cell. This causes inherent risks for operators who are exposed to chemicals such as coolants and oils used in the normal operations. There is also a risk of burns since many parts of the turbocharger get to extreme temperatures during the hot test cycle.
How has Cummins found success with cold testing turbochargers?
Scaling up operations:
Cummins began using cold testing in 2015. Since then, the results have been nothing short of impressive. With an average of 12,000 turbos tested every week, Cummins has not only been able to scale its operations but also maintain stringent quality controls, ensuring that every product is up to par with our standards.
Better detection of defects:
Another significant achievement that stands out in Cummins' use of cold testing is the dramatic reduction in BIS PPM (a way of counting defects made by the production process). Since the introduction of cold testing, there has been a 60% decline in BIS PPM, highlighting the method's precision in detecting and addressing defects. This impressive reduction is a testament to the effectiveness of cold testing in ensuring the quality and reliability of turbochargers.
Reduced cycle time:
Furthermore, the efficiency of cold testing is underscored by the difference in cycle time when compared to alternative methods. While hot testing procedures might take up to 30 minutes per product, cold testing drastically reduces this duration, clocking in at a mere 75 seconds. This expedited process means Cummins can test a higher percentage of products in a shorter time frame, ensuring consistent quality across the board while also meeting the demands of a bustling market.
In evaluating the best turbocharger testing methods, cold testing has numerous benefits over hot testing. With an emphasis on efficiency, environmental considerations, and customer benefits, cold testing offers a streamlined approach to ensure turbochargers are ready for the road. Cold testing has also allowed Cummins to streamline its turbocharger testing. Learn more about our turbochargers and let us know if you'd like us to reach out to you.