What are Battery Energy Storage Systems (BESS)?
By Cummins Inc., Global Power Technology Leader
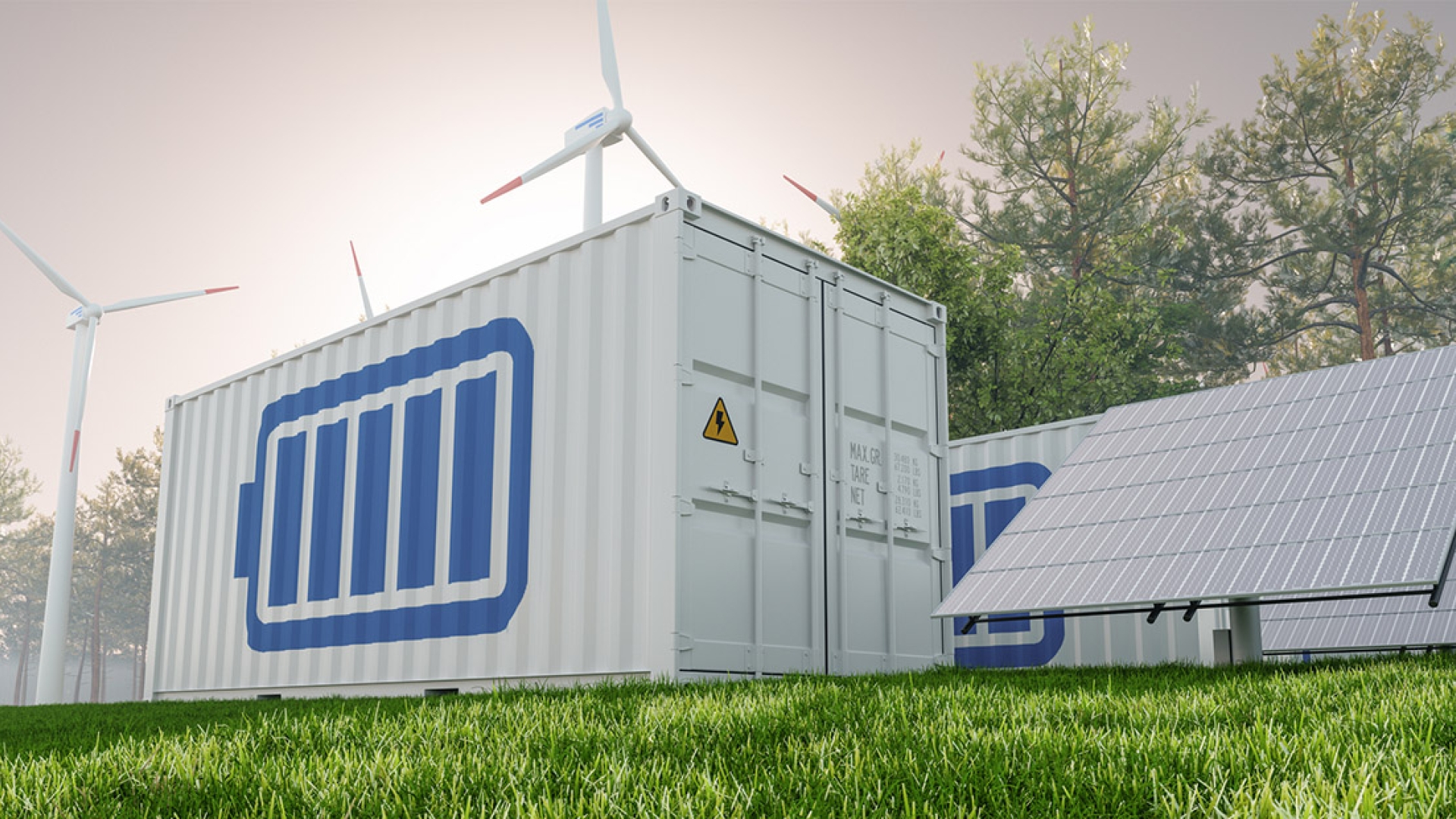
The electricity grid is the largest machine humanity has ever made. It operates on a supply-side model – the grid operates on a supply/demand model that attempts to balance supply with end load to maintain stability. When there isn’t enough, the frequency and/or voltage drops or the supply browns or blacks out. These are bad moments that the grid works hard to avoid.
The electricity grid consists of a massive array of parts including:
- Generators using hydro, thermal, nuclear, gas, oil, coal, solar, wind, tidal, and other power sources.
- Step-up transformers to raise generated voltages to transmission line voltages.
- Long transmission lines.
- Step-down transformers (substations) to bring voltages down to local transmission levels.
- Street transformers to deliver consumer-level voltages (240V, 110V, and 400V three phase).
What it does not traditionally have is any means to STORE electricity to match demand surges. This means that in a grid not equipped with BESS, any excess power generated must be dissipated in the grid. Generators must be kept spinning, ready to be connected the moment demand surges beyond the already connected supply – the “spinning reserve.” In a well-managed grid, the spinning reserve can be 15–30% of capacity to be ready for surges in demand. Battery energy storage systems are tools that address the supply/demand gap, storing excess power to deliver it when it is needed.
This article will discuss BESS, the different types, how lithium batteries work, and its applications.
The BESS Principle
Battery energy storage systems (BESS) are becoming pivotal in the revolution happening in how we stabilize the grid, integrate renewables, and generally store and utilize electrical energy. BESS operates by storing electrical energy in rechargeable reserves, which can later be discharged to power local or grid-scale demand. Perhaps most importantly, these battery-held reserves are ready to switch into grid supply quickly, as demand or frequency/voltage instability trigger them automatically.
Cummins Inc.'s main target with BESS is behind-the-meter support and integration into in-front-of-the- meter grid operational support. This is relevant to both off-grid and on-grid applications, or local integration of renewables at a site, or power backup for unreliable grid connections.
While these storage systems require investment, they offer some enormous advantages that can represent overwhelming benefits. Chief among these is the speed of response. The battery reserves can usually be switched to grid-synchronized AC at astonishing speed – typically within a few cycles
of the AC frequency (50–60 cycles per second or Hz). The highest price of electricity supplied to the grid is a fast-response supply, so the commercial value of the stored power can be 10 to 100 times the normal price.
The right battery technology offers long-term stable reserves – typical lithium-based battery technologies can hold high power levels for years, if necessary. Flow batteries can hold the power almost indefinitely.
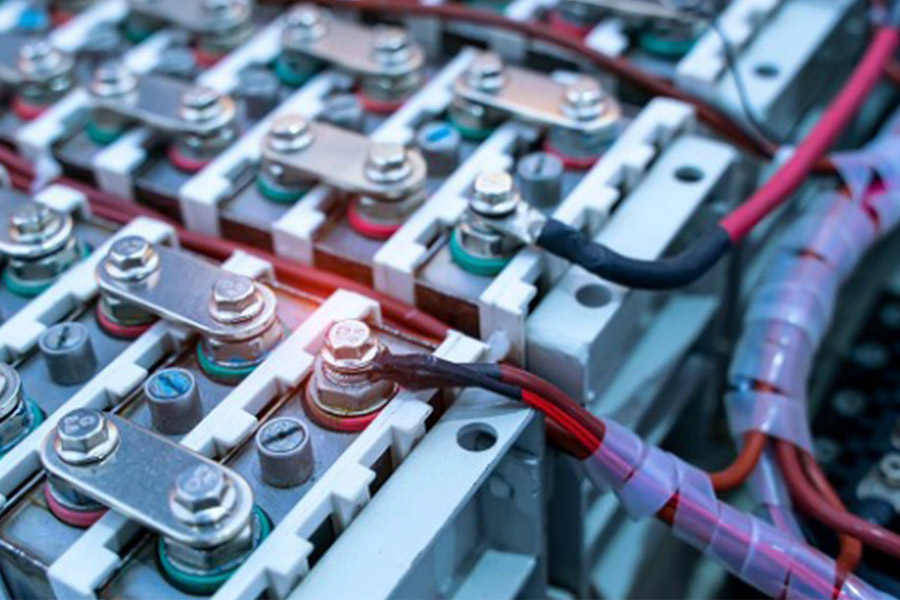
How does BESS work?
The energy storage begins at the charger system. This takes the “excess” AC grid or DC solar power and conditions it to recharge the cells. This can be a fast charge or a slow charge, depending on the setup and the current available.
BESS systems can enhance local microgrid efficiency markedly, by time-shifting lower cost power and by smoothly integrating variable sources like solar, wind, etc, for close to full utilization of their output by time-shifting and buffering.
At the battery cell, most commonly one of the lithium types, energy is stored as electrochemical potential, which is supplied as DC potential difference – as opposed to the AC (alternating current) that the grid requires. The individual cells are the building blocks of battery packs, interconnected into packaged cell clusters called packs to build capacity, reliability, and enduring performance. Cells can be cylindrical, prismatic, or pouch construction.
Cylindrical types can allow better cooling circulation but offer lower packing density. Prismatic types stack close and optimize density. Pouch types can be used to conform to more irregular cavities and lacking the rigid enclosure tend to be lighter.
The battery packs are integrated into modules, which are supervised automatically for charge/discharge management, condition monitoring, and cooling. These modules balance performance, safety, and reliability at a granular and automated level, operating as an intermediary between individual cells and the high-level storage system control.
Multiple modules are aggregated and controlled within a containerized power storage solution. Typically termed energy storage units (ESUs) or battery energy storage systems (BESS), these house all necessary components, including:
- Power electronics: Manage the flow of energy in and out of the system, ensuring seamless integration with the electrical grid or standalone applications. This involves the use of inverters and power conversion modules to turn AC into DC to charge the battery AND phase- coupled inverters to return the DC-stored electrochemical potential to the grid as AC. Phase coupling ensures the AC is in-phase with the cycles of the grid connection, to deliver optimal power efficiency.
- Thermal management systems: Regulate temperature to optimize battery performance and longevity.
- Safety mechanisms: Mitigate risks such as overheating or overcharging and handle the rare emergencies that result from system faults.
It’s worth noting that battery charging is NOT free. Typically, the recharge process is around 70–75% efficient. This means for 100 units of excess power available from the grid, the battery stack will uptake 70–75% to be returned as usable power later. The rest is lost as heat.
A steady flow of advances in battery chemistry and fundamental technology is combined with system design and control algorithm innovations. This is done to boost the efficiency, reliability, and budget challenges of BESS, shaping the future of the electricity grid, worldwide.
What are the different types of BESS?
Operational and commercially available BESS setups come in various types, each with unique characteristics that are better suited to particular applications, environments, or operational differences. Although many technological details in the control and battery management systems (BMS) are different, at their core, BESS are classified by the nature of the cell/battery systems they employ. The different types of BESS are listed below:
- Lithium-based systems: These encompass lithium-ion cobalt oxide (LiCoO2); lithium-ion nickel cobalt aluminum oxide (NCA); lithium-ion nickel manganese cobalt oxide (NMC); lithium-ion iron phosphate (LiFePO4); lithium titanate (LTO); and solid-state lithium-ion. Together these are the most common class of BESS due to their high energy density, long deep-cycle life, and relatively low maintenance requirements. They are versatile across all of the operational modes that BESS encounters.
- Flow batteries: Store energy in liquid electrolytes contained in external tanks. They benefit from scalability and long cycle life, making them optimal for large-scale permanently installed energy storage applications. Vanadium redox flow batteries (VRFBs), for example, offer very long duration storage and flexibility in power output.
- Lead-acid batteries: Have been used for energy storage for over 150 years and are appreciated for their low-cost robustness. Although they offer considerably lower energy density and shorter cycle life compared to more current technologies, they remain relevant for certain applications, such as backup UPS (uninterruptible power supply) power systems and smaller (typically domestic) off-grid installations.
- Sodium-sulfur batteries: Operate at high temperatures and use molten sodium and sulfur as power storage media. They can have high energy density and are well adapted to large- scale applications, such as grid stabilization and renewable/junk-power integration.
- Supercapacitors (or ultracapacitors): Store energy as electrostatic charge and offer the highest possible charge and discharge ability. Although they (currently) have lower energy density than batteries, they excel in applications requiring frequent cycling, such as short- term ballast for smoothing out brief power fluctuations in microgrids.
Pros and cons of battery types
BESS systems can use a variety of battery types with relative advantages and disadvantages that are worth considering. For example, Lithium Iron Phosphate (LFP) batteries offer longer term deep cycle durability than Lithium polymer (LiPo) and they are resistant to dendrite growth so they pose no fire risk. Their day-one capacity is a little lower than LiPo, but after a few hundred cycles they'll hold up better in capacity.
Nickel-Manganese-Cobalt (NMC) batteries, on the other hand, have a shorter deep cycle life expectancy than LFPs but they offer increased power density and considerably better cold weather performance, particularly in charging, which can reduce operating overheads.
It's for these reasons that NMC and LFP batteries are increasingly prevalent in BESS applications.
How lithium batteries work
Lithium batteries function through electrochemical reactions involving lithium ions moving between the battery's positive (anode) and negative (cathode) electrodes, with material motion blocked by a separator that allows ion transport in the electrolyte. Lithium batteries typically contain a cathode (the +ve) formed from a lithium compound such as LiCoO2, NCA, NMC, LiFePO4 and LTO. These remain typical in the newer, solid-state embodiments.
An anode (the -ve) is usually made of carbon (graphite or graphene). Coatings applied to the electrodes aid as barriers to the formation of dendrites, metallic threads that form on the surface of the electrodes and can pierce the separator and cause short circuits. These coatings include polymers or ceramics, depending on the manufacturer.
Between the electrodes there is typically:
- Electrolytes: There are three classes of electrolytes used in lithium battery technology including:
- Liquid electrolyte: A lithium salt dissolved in an organic solvent, often containing flame-retardant additives. The lithium salt is the ionic conductor that transfers charge; the organic solvent delivers high ionic motility and the additives optimize the stability, conductivity, and safety of the electrolyte.
- Polymer-based gel electrolytes: They deliver high ionic conductivity but a much- reduced chance of leakage. The polymer matrix acts as a gelling agent and, by design, they don’t pose a barrier to ionic motility within the solvent. The lithium salt acts in the same way, but gel-type cells offer improved battery safety and cycle life.
- Solid-state electrolytes: New alternatives to liquid electrolytes that improve safety and stability, acting as a barrier against dendrite formation and improving the thermal and chemical stability of the battery. This facilitates higher charge and discharge rates without increased risk.
- Separators: Porous membrane structures that force a physical gap between the anode and cathode, while allowing lithium ions to pass through during charge and discharge. Separators are generally constructed from high-porosity polyethylene (PE), often containing a polypropylene (PP) element to improve robustness.
During charging, lithium ions are electrically “pushed” from the positive electrode to the negative electrode through the electrolyte and become adsorbed onto/into the anode carbon. Electrons flow from anode to cathode in the outer circuit during charging. The charge current pushes electrons from anode to cathode. During discharge, these ions move back to the positive electrode, releasing electrical energy, and current flows in the outside circuit from cathode to anode. This ionic movement is greatly assisted by the crystalline structures within the electrode materials and energized by the flow of electrons through the external circuit in both charge and discharge.
The voltage and capacity of lithium batteries vary with the electrode/electrolyte chemistry and internal design, with voltages ranging from 3.6 V to 3.7 V per cell. Capacity relates to the amount of electrolyte and the size and construction of the electrodes. The discharge rate depends on many details and the internal safety systems in the cell and the battery. These prevent overcharging, over- discharging, and thermal runaway.
Systems within a BESS
A battery energy storage system (BESS) is typically composed of the following:
Cell raw materials and construction
Lithium-ion batteries are made in three basic forms – rigid cylindrical, rigid prismatic (square or rectangular section), and nonrigid pouch cells. The raw materials for all of these typically include:
- Ionic lithium salts: Allows motility of charge within the cell
- Organic solvents: Act as charge carriers to allow current to flow between the electrodes. This can be liquid, gel, or solid depending on the battery technology.
- Cobalt: Used in cathodes for stability
- Nickel, manganese and aluminum in cathodes: Used to reduce cobalt use
- Graphite: These are present in typical anode structures, but this is evolving towards silicon for higher capacity and robustness
- Binders (typically polyvinylidene fluoride (PVDF), polyvinyl alcohol (PVA), carboxymethyl cellulose (CMC) or styrene-butadiene rubber (SBR)): Integrates and toughens the electrode materials
- Porous separators of PE and PP: Isolate the electrodes and allow ion movement
- Case materials – steel, aluminum, or polymer tubes (for cylindrical and prismatic cells), and heat-sealed polymer films for pouch cells: The cell casing seals in the electrolyte and ensures electrical and physical isolation of the chemistry. In a few cases in which thermal isolation is paramount, ceramic cases can be used – and in aerospace applications lightweight composites such as carbon fiber are used.
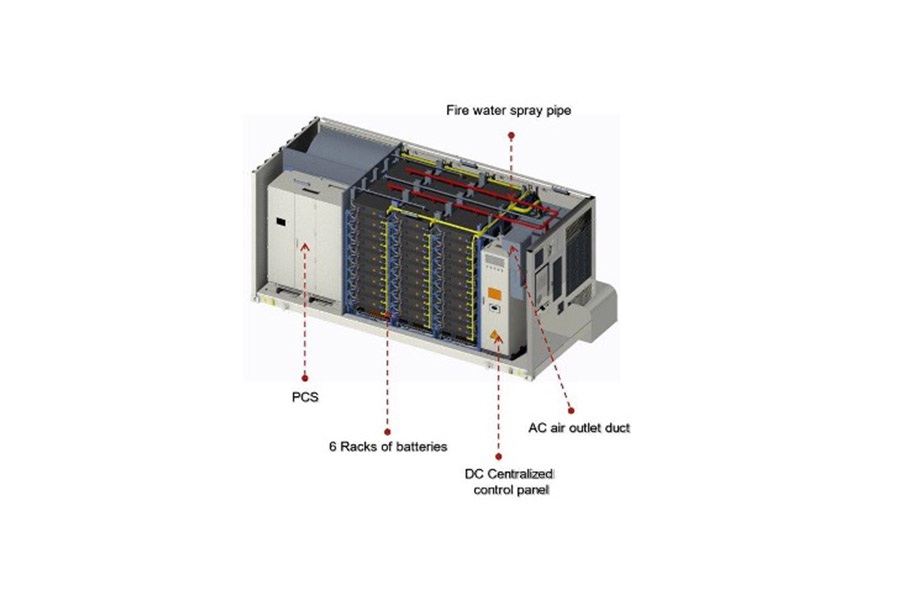
Other components
A functioning BESS container system or installation also consists of the following:
- BESS controller: This system oversight runs power allocation, manages charging, and has operational oversight and safety control.
- Structural frameworks and enclosures: Used for housing and retaining battery modules.
- Battery management systems: Monitor and control battery performance, ensuring safety and efficiency.
- HVAC cooling systems: regulate temperature within the container, preventing overheating during high charge or discharge periods to enable optimal operation.
- Grid synchronized inverters: Convert DC power from batteries into frequency- synchronized AC power for grid connection or other applications.
- AC to DC converters (rectifiers): Deliver grid AC as battery-friendly DC voltage for charging.
- Transformers: Serve to raise or lower voltage levels to match grid or local system requirements.
- Cooling systems: Many elements of a BESS setup require temperature control for good function.
- UPS: The BESS system can operate as a high capacity uninterruptible power supply (UPS).
- Fire suppression systems: Detect and extinguish fires to safeguard the installation.
BESS applications
BESS installations fit a wide variety of applications across various sectors including:
- Grid stabilization and frequency regulation result from fast response to sudden changes in demand or supply on the local (or wider) grid. This allows BESS installations to contribute to the stabilization of frequency and voltage by soaking up excess energy during periods of reduced demand (or oversupply) and releasing stored power during elevated demand.
- Renewable energy integration requires the buffering of supply at its peak and the smoothed availability of power that results. BESS installations store the otherwise useless oversupply that is typical of solar and wind power. Smoothing out the destructive fluctuations in renewable energy removes the “junk power” effects of oversupply and disruption. This allows greater penetration of renewable energy into the grid that does not rely on thermal resources to compensate for brief (or longer) collapses in supply.
- Peak shaving and load management are key BESS services that can reduce electricity costs by storing energy during off-peak hours when prices are low and discharging it during peak hours when prices are high. This peak shaving helps to alleviate strain on the grid during periods of high demand and reduces the need for expensive peaking power plants. In distributed microgrids, this implies less fuel (diesel) will be required, and generator stress and maintenance costs will be lowered.
- Microgrid support is similar to peak shaving, in that a BESS can provide backup power, load balancing, and grid support services. This enhances the reliability and resilience of microgrids, ensuring uninterrupted power supply and optimizing the use of renewable and thermal energy resources.
- EV charging infrastructure is greatly enhanced by BESS, supporting the deployment of EVs by providing more responsive fast-charging capabilities and managing peak demand. The integration of large numbers of EVs into the grid without overloading existing infrastructure is the greatest challenge that electricity networks face, and BESS is critical in managing peak demand safely.
- BESS can provide uninterruptible power for critical industrial and commercial facilities, ensuring seamless operations during grid outages or blackouts and reducing electricity costs through agile demand response.
- BESS can be installed in homes, making the behind-the-meter more effective/lower cost by storing excess energy from solar panels or during high-supply, low-demand hours, available for later use.
- BESS can provide reliable power in remote or off-grid locations where access to the electrical grid is limited or unavailable. They are used in applications such as telecommunications, remote monitoring, and rural electrification projects.
Why BESS is crucial for on-demand energy storage systems?
BESS plays an increasingly crucial role in self-healing, anti-fragile electricity grids. They help integrate renewable energy sources, improving energy efficiency and enhancing voltage/frequency reliability and overall system resilience.
Careful application of BESS removes the operational limit that otherwise applies to electricity grids in accommodating intermittent (solar, wind, tidal, wave) power sources that are otherwise considered junk power when oversupply happens. The spinning reserve requirement limits most grids to 15–25% intermittent sources. Whenever BESS acts as a buffer, however, this spinning reserve can be the BESS system, with no wasted energy. This versatile scalability makes BESS indispensable in the transition towards a more sustainable and resilient energy future.
Interested in more from Cummins? You might also like:
• In-Depth exploration of Cummins Microgrid testing lab, the Power Integration Center (PIC)
Author Profiles
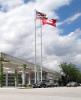
Cummins Inc., Global Power Technology Leader
Cummins Inc., a global power solutions leader, comprises five business segments – Components, Engine, Distribution, Power Systems, and Accelera by Cummins – supported by its global manufacturing and extensive service and support network, skilled workforce and vast technological expertise. Cummins is committed to its Destination Zero strategy – the company’s commitment to sustainability and helping its customers successfully navigate the energy transition with its broad portfolio of products. Cummins has approximately 69,900 employees and earned $3.9 billion on sales of $34.1 billion in 2024. See how Cummins is leading the world toward a future of smarter, cleaner power at www.cummins.com.
Related Topics
Related Tags