Overcoming high-pressure regulator and on-tank valve challenges in commercial transportation
By Cummins Components Business Unit
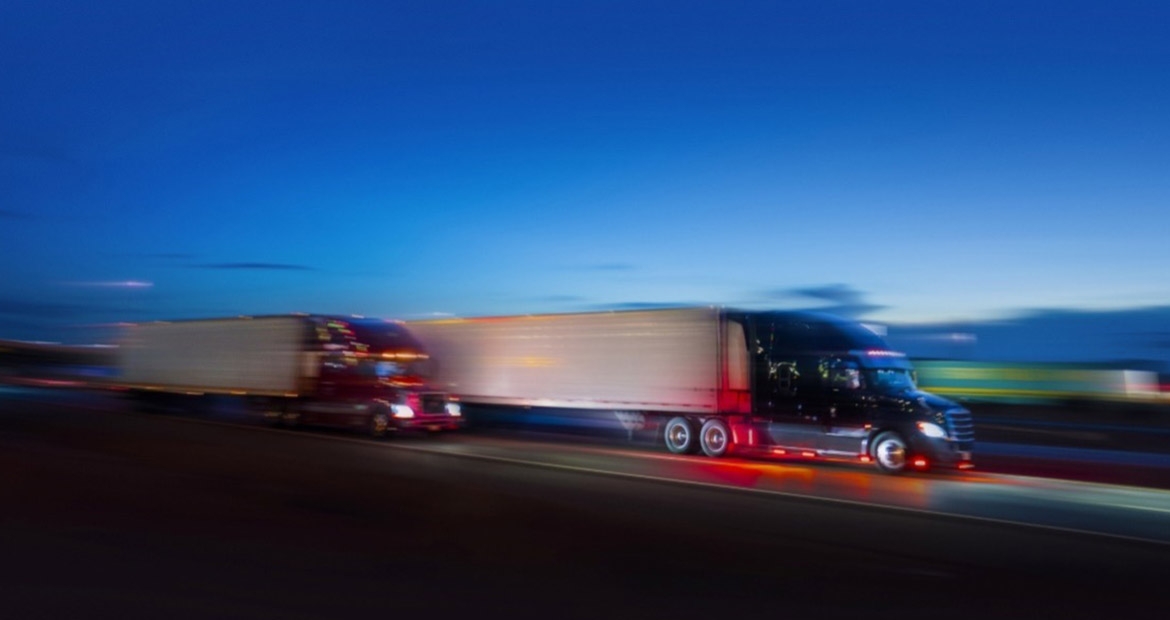
The adoption of gaseous fuels like hydrogen and natural gas is becoming increasingly popular in commercial transportation. Both technologies help reduce emissions and provide worthy alternatives for meeting sustainability goals, especially for heavy-duty cycle trucks. There are, however, two safety considerations to keep in mind when using natural gas and hydrogen technology due to the high-pressure nature of these fuels.
The two essential components that impact the use and safety of these alternative fuels are the high-pressure regulator (HPR) and the on-tank valve (OTV). While both components play a vital role in managing hydrogen delivery to internal combustion engines (ICE) and fuel cells (FCEVs), their production face some key challenges in the industry.
We have explored articles on other critical components like the fuel system, turbochargers, software and electronics. This article explores these two components further and explains how they work. It outlines the critical market challenges they face and sheds light on the implications for engine manufacturers, their supply chains and broader adoption efforts.
Role of high-pressure regulators (HPR) and on-tank valves (OTV)
HPRs play a crucial role in reducing the pressure of gaseous fuels, like hydrogen stored at high pressures (over 10,000 psi), to levels manageable for use in combustion engines and fuel cells. In addition to controlling pressure, HPRs serve as shut-off valves, halting the flow of the fuel when the vehicle is turned off. They also use pressure sensors to aid in performance and diagnostic controls.
OTVs are fitted onto fuel tanks and facilitate the fueling and de-fueling process. They act as safety mechanisms by preventing excessive fuel flow to the engine in case of leaks or failures. Moreover, OTVs have integrated pressure relief devices that activate under high temperatures or fire conditions to vent fuel and prevent explosions and other dangerous conditions.
Both HPRs and OTVs are crucial for the safety and performance in high pressure technologies and are therefore instrumental in the advancement of lower-emissions vehicles. As adoption grows, so will the demand for these components.
Challenges facing manufacturers around HPR and OTV
With the growing adoption of natural gas, FCEVs and H2 ICE vehicles manufacturers must produce greater quantities of HPRs and OTVs to meet growing demand for more vehicles on the road. However, increasing the production of these components comes with the challenges and limitations we must consider.
Meeting stringent pressure requirements:
HPRs directly influence the performance of H2 ICE and natural gas technologies. At present, HPRs are mostly designed for fuel cell applications, which require lower output pressure. However, there is still a significant need for HPRs that can deliver the higher output pressures for direct injection H2 ICE applications. Furthermore, to meet the performance demands, there is a need for HPR’s that can meet stringent pressure tolerances throughout the life of the vehicle.
Cummins components business is leveraging the industry leading skills and tools to address this challenge. We have expertise in fuel regulation for both diesel and gaseous fuel systems with products that include mechanical dump valves, metering valves and check valves which ensure accurate delivery of fuel to the system. Furthermore, Cummins experts are working on designing, simulating and integrating new technologies that are optimized to meet system-level needs.
Supplier limitations:
Smaller suppliers in the market today lack a global presence, leading to challenges in serviceability and troubleshooting, particularly for OTVs. This impacts vehicle uptime, cost and performance issues for customers.
One way in which Cummins is navigating this challenge is through the company’s vast global service network that is capable of supporting service and repair for both components effectively. A global network and supply chain system is necessary to ensure customers have convenient and close access to service locations. With a strong service network and clear service guidelines, repairs can be promptly done which can help increase vehicle uptime.
Cost barriers to adopting technologies:
Higher cost of components like HPRs and OTVs can be a challenge to the adoption of hydrogen technologies. Design complexity, low manufacturing volumes and the extensive certification testing required are key reasons that can drive up costs, making economic justification for adopting these technologies challenging for businesses.
One of the tools to help drive down costs is the use of modular design around a base architecture. Modular designs allow customers to select only the options they need, keeping the base architecture the same. Cummins is exploring these options while also being committed to bringing competitive pricing by leveraging our current product portfolio and global manufacturing footprint in order to reduce cost.
Complex testing regulations and infrastructure:
Before fuel delivery systems can be sold in most markets, they must undergo a rigorous certification process to ensure safe operation. The approval process is dictated by government regulations and industry norms. The infrastructure needed for testing is complex and often region-specific, adding another layer of challenge and costs for manufacturers.
From our many years of work with diesel and natural gas engines, Cummins has extensive testing infrastructure to validate new technologies. Our long-standing relationships with world-class testing facilities to meet the most complex testing needs. Our recent joint ventures with fuel delivery system suppliers also provides access to further testing capabilities that can play a role in mitigating the challenges of testing infrastructures and providing compliant, safe and reliable products to customers.
Evolving regulatory compliance and standards:
The landscape of regulations, industry best practices and standards for HPRs and OTVs is complex and constantly evolving. Compliance with regional regulations such as UN and EU standards requires continuous adjustment and can significantly affect the viability of these components in different markets.
Furthermore, the lack of uniformity in regulatory standards across different jurisdictions complicates the certification process and global distribution of these components. Manufacturers must design and test their products to meet the specific requirements of each market they wish to enter, increasing the complexity and cost of development. This demands a flexible and adaptive approach to product design and testing that considers region-by-region requirements. This adds complexity to the product which drives up production costs and makes manufacturing less streamlined.
Cummins is exploring the best practice of certifying the ‘worst case’ design variants during the certification process. Worst-case variants are design conditions or settings that stimulate worst-case conditions. By testing a component design under the worst-case design condition, it helps to determine how design works across all other conditions and modify it accordingly. By identifying the elements that can go wrong, companies can limit the need for re-testing and re-certification for minor design changes.
The Path Forward
Manufacturers and stakeholders including governments, consumers and businesses interested in increasing natural gas, H2 ICE and FCEV adoption must collaborate to overcome these obstacles, focusing on innovation, cost reduction and regulatory compliance. Such efforts will not only enhance the performance and safety of these lower emissions vehicles but also pave the way for their broader adoption.
Author Profiles
Related Tags